The Development of CF Aluminum Die-Casting for Superthin Walls
Yamaha mastered its controlled filling (CF) aluminum die-casting technology at the dawn of the 21st century. Long seen as an exciting next-generation technology that would broaden the possibilities of Monozukuri, CF die casting continues to be further developed and refined today. This casting technology has opened up new realms of freedom for the design and production of large parts, allowing us to create frames and other aluminum parts that are lighter and more attractive to the eye, thereby bringing Yamaha motorcycles numerous advantages.
At our aluminum casting worksites, dynamism and delicacy go hand in hand. The red-hot metal and rising steam often steal the show, but pouring the molten aluminum into its mold requires a keen sense and touch, like a master chef in the kitchen. From the degree of vacuum and the temperature within the mold to the volume and speed of the injected molten aluminum, everything must be carefully controlled to maintain a delicate balance. Using the latest in casting analysis technology helps ensure each process is optimized.
But to meet the demanding requirements set down for the new MT-09, Yamaha’s CF aluminum die-casting technology took yet another step forward.
Thinner and Thinner
The targets for the new MT-09 were very high; some might say they were “too high.” The development team was firm in their determination to greatly enhance the agility of the ride, and achieving this meant that lightening the chassis became a top priority. On top of that, they wanted not a slight reduction, but a significant one.
So the design, material and manufacturing departments put their heads together, working to take Yamaha’s CF aluminum die-casting technology further in order to meet the goal. The result of their work was a new frame weighing a whopping 2.3 kg lighter than the previous model’s. Mission accomplished.
“The sections that needed to be thick were made thick, but whatever could be made thinner, we did without exception.”
You can’t see the strength and flexibility of a frame with the naked eye, but a cross-sectional view instantly reveals its secrets. Although it is a single cast piece, the thickness of the various sections rises and falls like a shallow waves—the thinnest sections are a mere 1.7 mm thick. The thinnest sections of the previous model’s frame were 3.5 mm, making the new one over 50% thinner.
Of course, the engineers knew right from the beginning that they would face challenges. “Because some sections were just so thin, everybody could easily imagine the molten aluminum struggling to flow into the narrow spaces of the mold.”
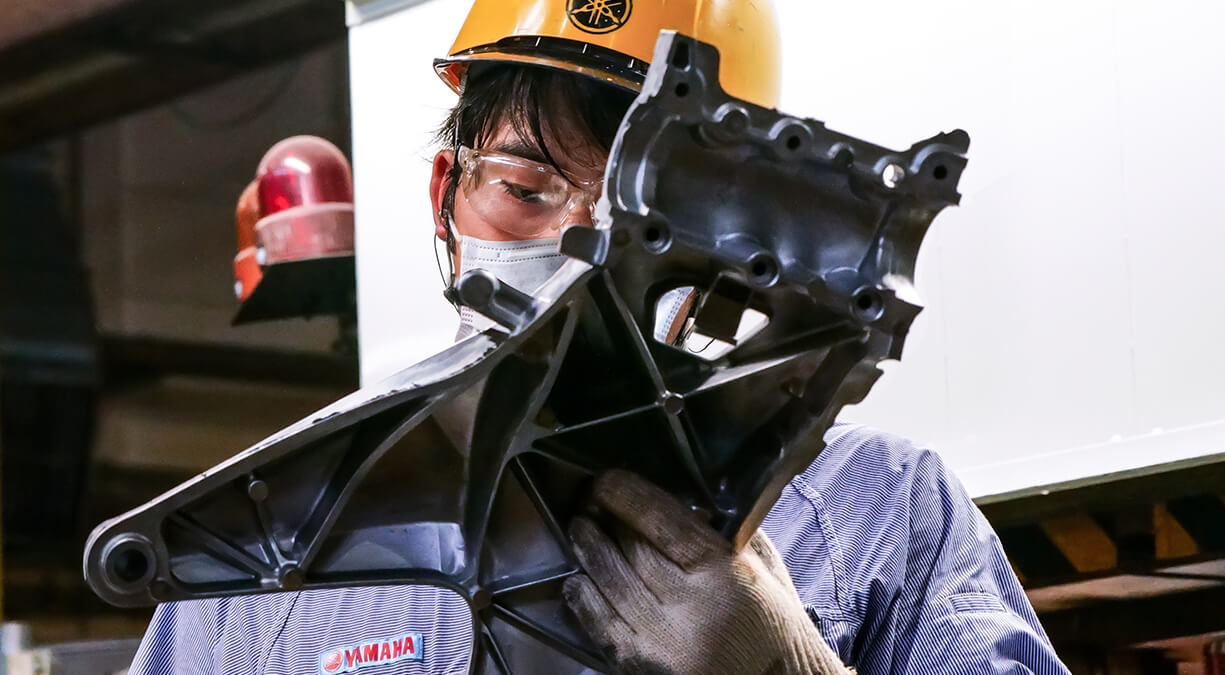
Today’s Work is Tomorrow’s Starting Line
In order for the molten aluminum to smoothly pass through the 1.7 mm passageways inside the mold without hardening, the mold temperature had to be kept high and the filling speed had to be even faster. Selecting an oil-based, heat-retaining release agent suitable for high temperatures is what allowed the mold temperature to remain high during the casting process. Additionally, the passageways for the entire casting design—from the ingate to the venting system—were reviewed from the ground up and the latest in flow analysis and modelling technology used to determine the ideal flow for the aluminum inside the mold.
At a pre-production meeting for the new MT-09 held to get input and opinions from everyone involved, one of the team members made a suggestion: “Since the requirements we’re trying to clear are so high this time, I think this presents a good opportunity to connect what we’re doing now to future Monozukuri. So let’s incorporate all kinds of new ideas and technologies, and try to create a new starting line for the next generation of motorcycle frames.” The response was enthusiastic and even led to the idea of downsizing casting machines at the headquarters with an eye on future use at Yamaha’s casting facilities overseas. In fact, compared to what was planned before, much smaller machines ended up being used successfully.
“We proved that as long as we can achieve high-speed filling, we can create high-quality castings.”

Where We Must Excel
For those charged with creating the frame, what they could never let go of was their fastidious care for its exterior appearance. The designers strive to produce smooth and beautiful three-dimensional lines, but at the same time, they were constantly describing the frame’s exterior qualities as, “A structural body that inspires riders to have fun.” Much of the frame on the previous model was covered by exterior bodywork, and the approach was quite different with the new frame.
“We decided to make everything part of the bike’s overall design appeal. Of course, we kept the attractive, unbroken lines but we also removed any visible gaps.”
The engineers proudly state that metalworking aluminum is one field of manufacturing that Yamaha must always excel in. This drive and dedication can be seen in the selection of raw aluminum, for example. Some 90% of typical aluminum die-cast parts and products are made from a specific aluminum alloy. However, at Yamaha, our Monozukuri process begins with careful selection of the raw materials first based on the role of the part. This too is an important aspect of our craftsmanship.
“There’s unfortunately no easy way to simply see how thin, strong or flexible our aluminum frame is. But when riders experience the bike’s agile ride, we’re confident they will understand what we accomplished through that.” Almost twenty years have passed since the advent of CF aluminum die-casting technology, and the subsequent advances made with the technology in the quest to meet the MT-09’s “too high” targets are sure to be seen in hindsight as important milestones in Yamaha’s manufacturing history.
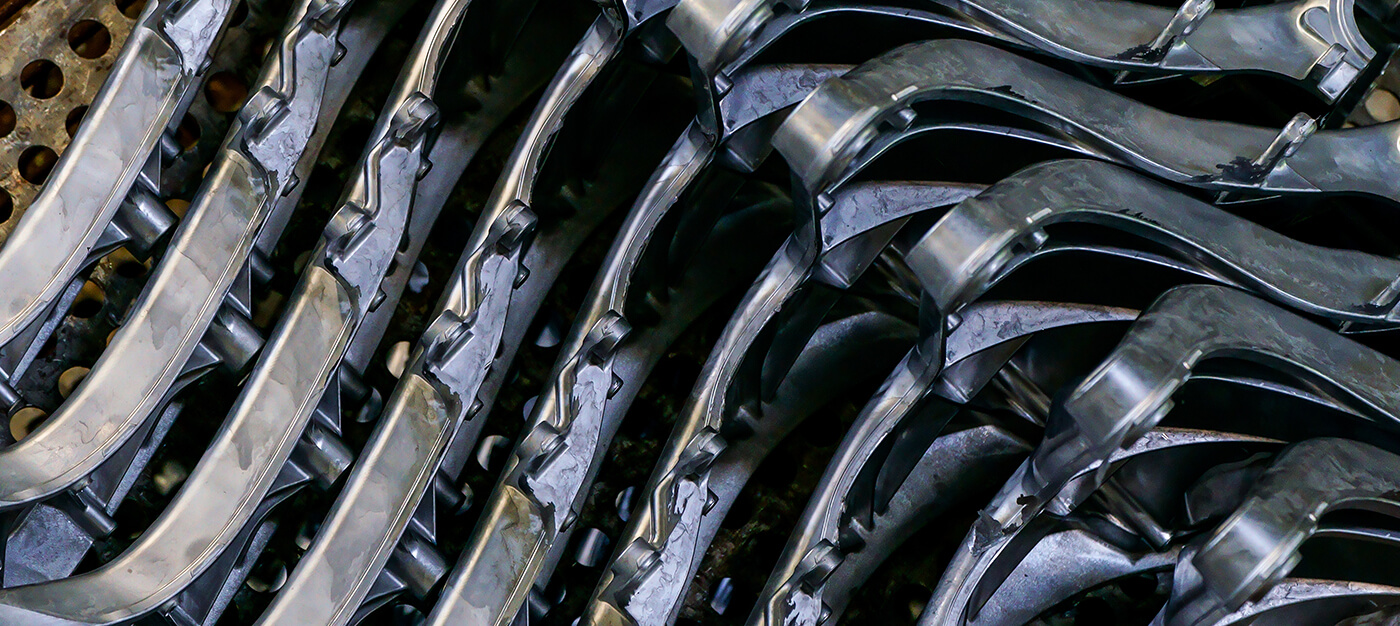