「超肉薄」を実現したCFアルミダイキャストの発展
CFアルミダイキャスト技術をヤマハが「ものにした」のは、21世紀に入って間もない頃だった。「ものづくりの可能性をひろげる次世代テクノロジー」として期待を集めたこの生産技術は、いまなお留まることなく進化と発展を繰り返している。大型部品の製造と形状自由度の高さを持ち味とするこの鋳造技術は、フレームをはじめとするアルミ部品の軽量化や美しさなどでヤマハモーターサイクルにさまざまなアドバンテージをもたらしてきた。
アルミ鋳造の現場には、豪快さと繊細さが同居する。真っ赤な業火と立ち上る水蒸気ばかりに目を奪われるが、金型にアルミ溶湯を流し込む工程の繊細さなどはまるでシェフの指先、舌先のようである。絶妙なバランスでシンクロする金型の真空度や温度、そして溶湯の吐出量と速度。それらすべての最適は最新の解析技術に下支えされている。「MT-09」が求めた高すぎる要求値に応えるため、CFアルミダイキャストがまた一つ進化を果たした。
薄くできる
部位は
容赦なく。
「MT-09」の要求値は高かった。高すぎる、と言っても過言ではない。「アジャイル(俊敏)な走りを飛躍的に進化させる」という開発の決意は固く、それを実現するために車体の軽量化は最重要課題としてクローズアップされた。しかもその要求値は「ごっそり、削ぎ落とす」というレベル。この高い要求に応えるため、設計、材料、工法の各部門は三位一体でCFアルミダイキャストの進化に取り組んだ。やがてその成果として、前モデルとの比較で骨格合計2.3㎏もの軽量化を実現してみせた。まさに「ごっそり」という表現に相応しい成果だった。
「必要なところには十分に厚みを持たせる。ただその一方で薄くできる部位については容赦なく削ぎ落とした」。目に見える逞しさやしなやかさではないが、フレームの断面を見れば一目瞭然。一体成型でありながら、各部位の肉厚が波のように変化する。最も薄い部位はじつに1.7mm。前モデルの最低肉厚が3.5mmだから半分以下の数字だ。一方で、当初は困難も予測されていた。「あまりにも薄すぎて、金型の細いエリアで溶湯が流れにくくなることが容易に想像できた」からだ。
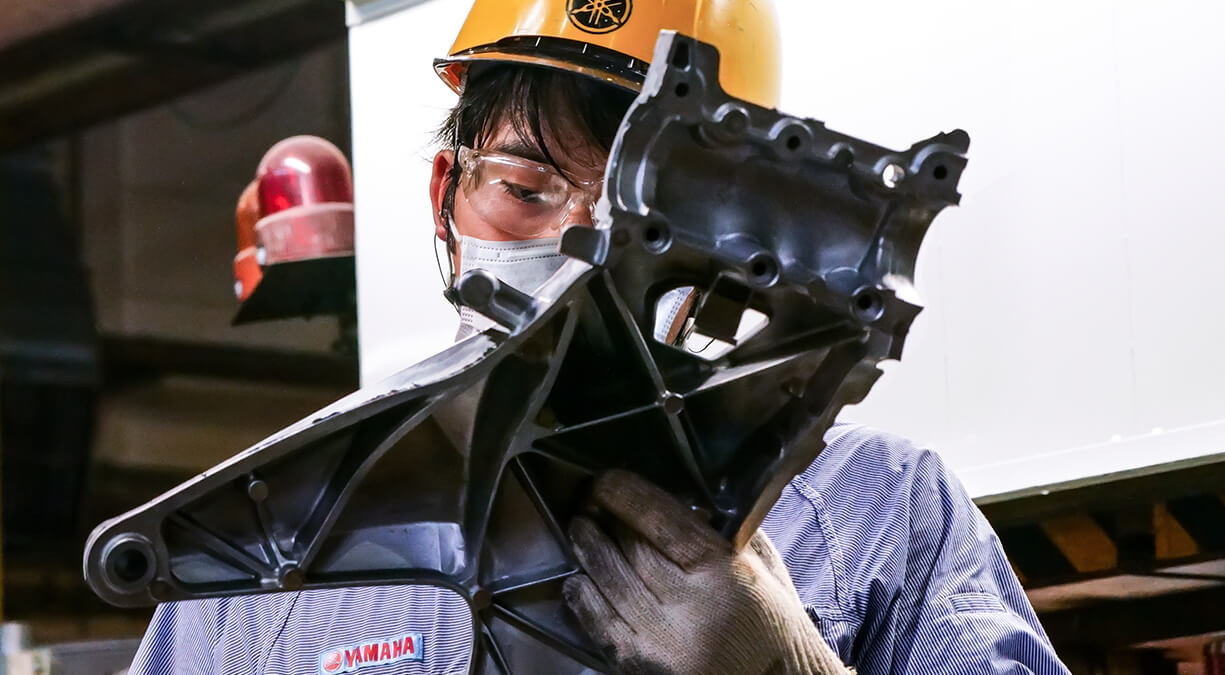
未来への
起点となる
シゴトを。
金型の中のわずか1.7mmという狭い通路。アルミを固まらせることなくその狭き門をスムーズに通過させるためには、金型の温度を高い状態のまま維持すること、そして溶湯の充填速度をさらにもう一段上げることが必要だった。保温性の高い油性離型剤を採用したのは型温度を高く維持するため。また、溶湯の注入から排出までの流路を根本的に見直すとともに、最新の解析技術を用いて溶湯の流れの最適化にも取り組んだ。
「MT-09」の生産準備を前に自由な意見交換の場があった。その中で、メンバーの一人からこんな意見が上がった。「(高い要求値に向き合う)この機会を将来のものづくりにつながるチャレンジとしたい。新しい発想、新しい技術をどんどん織り込んで、次世代のフレームづくりの基点となるような仕事にしていこう」。議論は熱を帯び、海外製造拠点への展開を見込んだ鋳造機のダウンサイジングというアイデアも生まれた。実際、以前に比べればかなり小ぶりの鋳造機が使用されることになり、それでも「高速充填を実現できれば高い品質の鋳造が可能であることを証明できた」という。
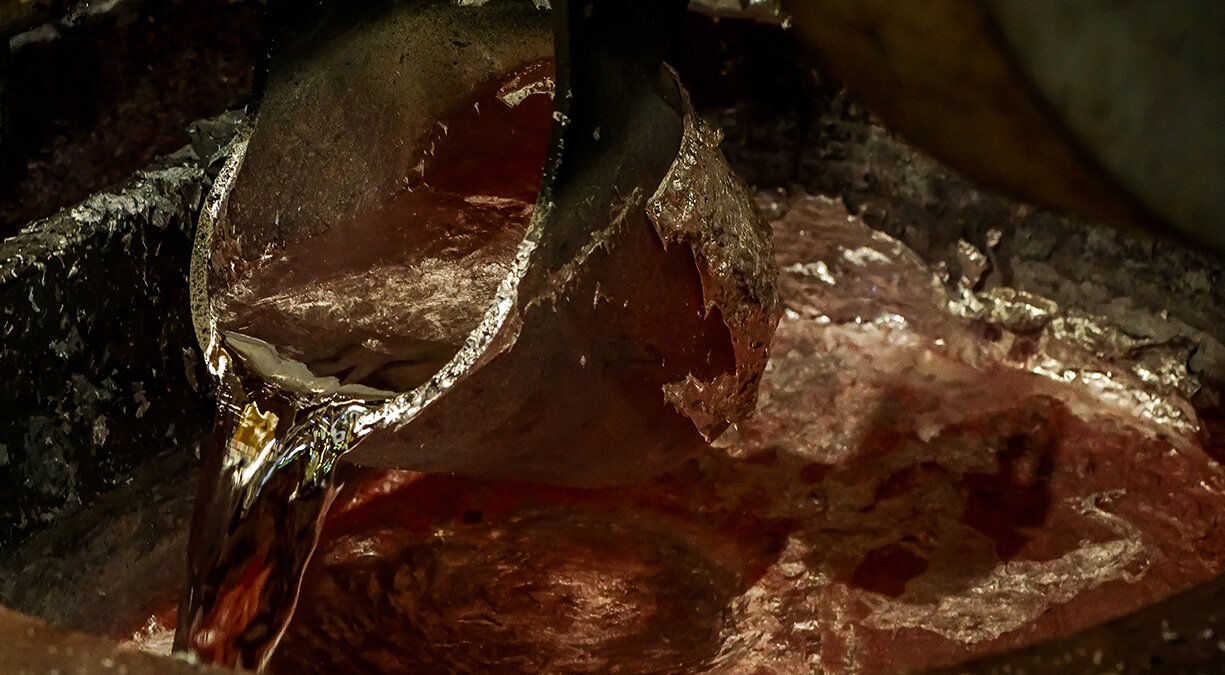
絶対に
負けられない
領域。
フレーム製造の現場にとって、最後まで気を抜くことができなかったのは外観品質だった。デザイナーは、滑らかな三次元曲線の美しさを求めると同時に、「遊び心をくすぐる見せる構造体」という言葉を使って外観品質に執着した。前モデルのフレームは外装部品で覆われる部分も少なからず存在したが、新モデルでは「いわば造形のすべてが意匠。継ぎ目のないきれいな曲線の再現はもちろん、わずかな隙きも見せられなかった」という。
「アルミは、ヤマハにとって絶対に負けられない領域の一つ」――。口々にそんな自負がこぼれ出る。たとえばアルミの原材料選び。一般的なアルミダイキャスト製品では、そのおよそ9割で特定のアルミ合金が使われている。しかしヤマハの鋳造現場では、用途に応じた原料の厳選からものづくりがスタートする。これもクラフトマンシップの発露の一つと言えるだろう。
「私たちが作ったフレームが、どれほど薄く、強く、しなやかなのか。それを見ていただける機会はない。ただ、オーナーの皆さんは、アジャイルな走りを通じて体感し、理解していただけるはず」。CFアルミダイキャスト技術は、その誕生から間もなく20年が経とうとしている。「MT-09」の高すぎる要求値に向き合うことで獲得した新たな技術は、未来への大きなマイルストーンとなるはずだ。
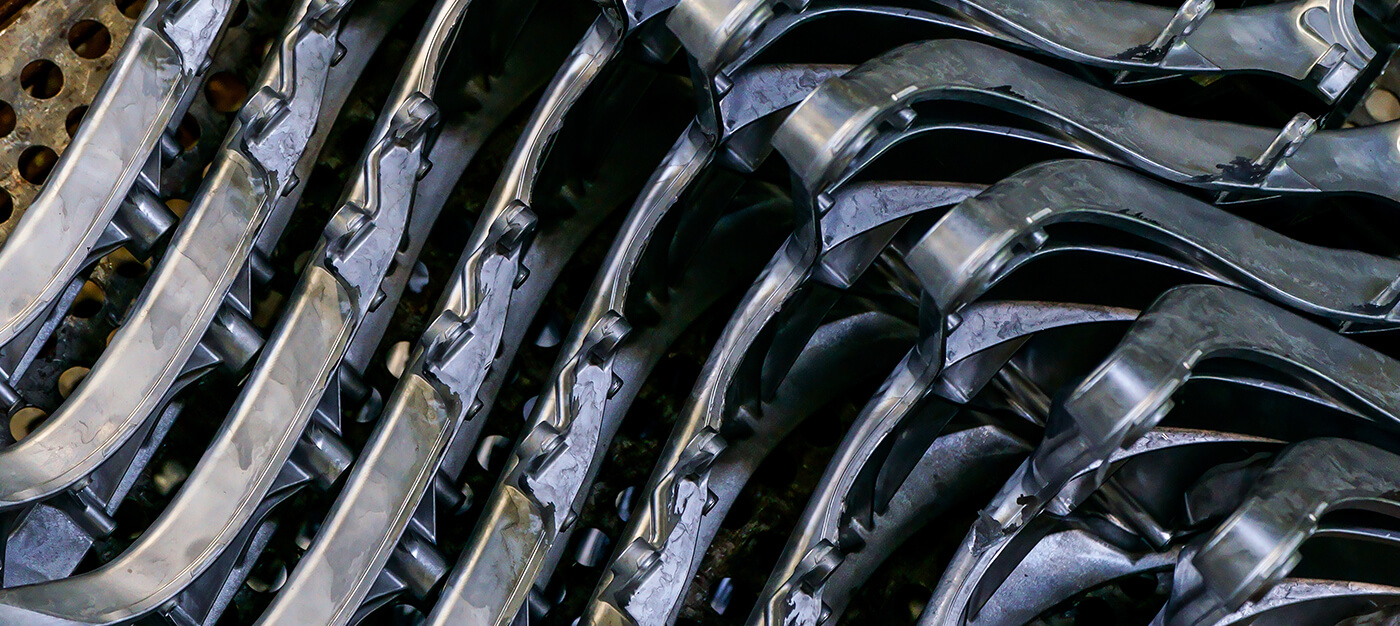