Audio System by Yamaha:Development Story
This page introduces Development Story of Audio System by Yamaha
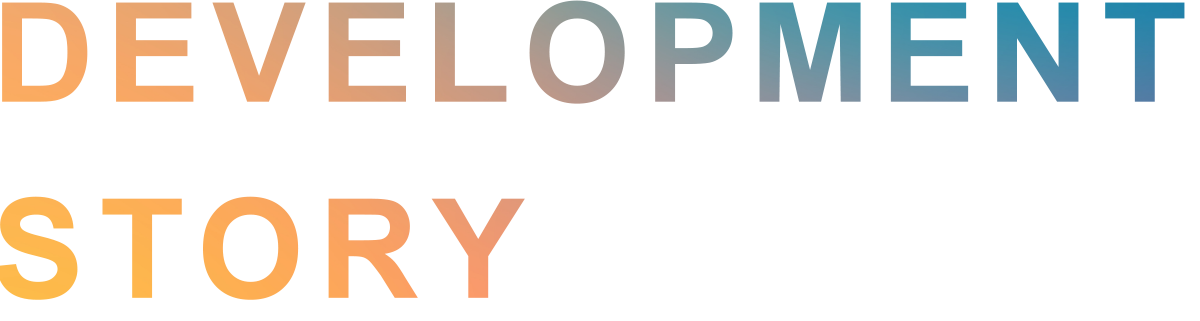
We Hope to Provide Music of Equal Quality Even on the Sea.
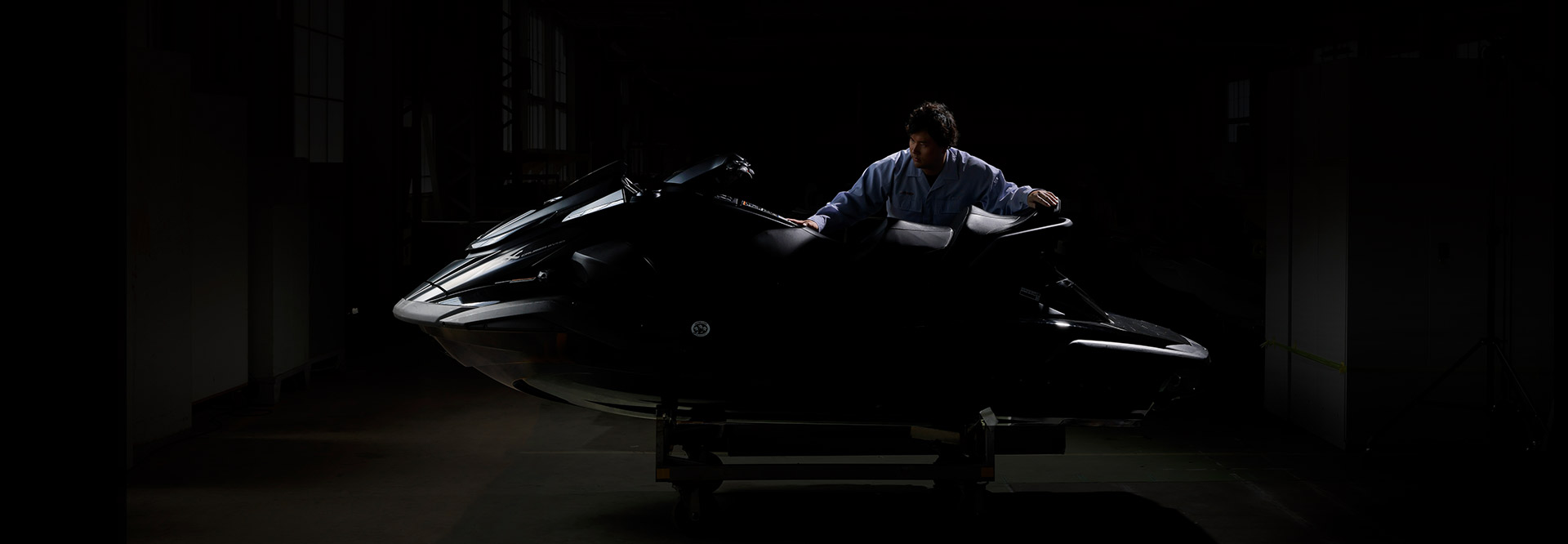
We aim to deliver sound that impresses our customers.
After much hardship, and with that belief in mind,
we completed the speaker equipped with the WaveRunner.
We interviewed five key members to hear their stories about development of the speaker.
Profile
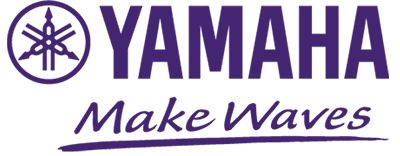
-
Kiyoshi Yamaki
Technology Development Group,
CX Strategy Promotion Department,
Electronic Devices Division,
Yamaha Corporation After joining the company, he handled semiconductor LSI design and evaluation. Then, he gradually shifted to work on the sound production side, starting with the promotion of ringtones for mobile phones, which became popular around 1999. Currently, he leads the sound design of audio products, such as automotive sound system. -
Toshiyuki Ono
Speaker Development Group,
Engineering Department,
Electronic Devices Division,
Yamaha Corporation He joined Yamaha in 2020. He has been involved in the development of automotive speakers and other audio products for about 25 years, including his former career. He is currently in charge of the development of Yamaha Motor's projects, including the WaveRunner, and oversees the development of other speaker units for amusement as the team leader. -
Koji Ogata
Strategic Purchasing Group (Supplier Quality Engineer),
Sales Department,
Electronic Devices Division,
Yamaha Corporation His first mission after joining the company was to develop the EOS Ti-22, the titanium head golf club that had the world's largest volume at the time. Through this project, he was involved in collaborative technical studies with Yamaha Motor. He then works as the team leader in the current Strategic Purchasing Group, responsible for the production technology and process design of automotive speakers.
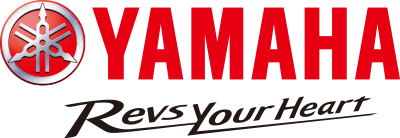
-
Masakichi Suzuki
Yamaha Motor Manufacturing
Corporation of America Since joining Yamaha Motor, he has been involved in the design of electrical components for the WaveRunner. Since 2021, he has been involved in the development of this audio product. As of July 1st, he was assigned as a development officer at Yamaha Motor Manufacturing Corporation of America (YMMC). -
Chihiro Matsumoto
Product Strategy Group,
Strategy Planning Division,
Yamaha Motor Co., Ltd. After working in the Development Department, he was transferred to Engine Design Department of the WaveRunner. Then he was assigned to the U.S. as a WaveRunner product planner, and is still in charge of product planning at the headquarters.
Their affiliation and titles are current as of the time of the interview.
Why don't Yamaha Motor boats have Yamaha Corporation audio?

Matsumoto:
Starting about ten years ago, we sold aftermarket audio as accessories in line with trends in the American market. After that, we moved to installing them as original parts, but as product planners, we also wanted to develop better audio that can meet the needs of our customers.
Suzuki:
Our company has been selling factory installed audio models since 2021. In fact, we had approached Yamaha Corporation about the development of the 2021 model. I heard that at the time, the high reliability requirements for the WaveRunner could not be reconciled with the cost, and unfortunately, we weren’t able to do development. After that, I also got involved in the development, and the biggest cause to get started was a very simple question: "Why don't Yamaha Motor’s boats have Yamaha Corporation audio?" As Matsumoto said before, when we were talking about what to do to aim for a better level of both volume and sound quality, we contacted Yamaha Corporation again and decided to consider it together, and development of this model started in June 2021.
Yamaki:
I was not involved yet in June 2021, and I found out about it when I saw an internal report. Before that, I had worked together a little on collaborations such as motor shows, and I had always wanted to work seriously with Yamaha Motor. When I heard about it, my first thought was that it sounded interesting. I think it was around August 2021, when the member who was originally in charge said, "There is a discussion about installing speakers in Yamaha Motor's WaveRunner, so can you make a demo right away?" I remember thinking, "I’ve been waiting for this, let's get started immediately!" and started connecting it to our DSP chip and amplifier environment to play audio through the speakers.
Ogata:
We were so positive about the project at the time because we already had experience with large-volume subwoofer boxes for automotive use. I heard that, because we had already been able to make boxes of a similar volume, they concluded that it was possible, including production feasibility. However, I only found out later how difficult it was (laughs).
Suzuki:
So, you had gained experience with automotive sound system over those few years, and decided that you could do it, and that's why you accepted our offer.
Yamaki:
I think the experience of automotive sound system development gave us a confidence. Before that, we had developed and sold small semiconductor LSIs and related products. In 2020, we finally reached the stage of starting acoustic tuning for the actual product for the automobile manufacturer that first adopted our automotive sound system, which we had been developing for a long time. However, due to COVID-19, we could not go on site, so we struggled to develop it while creating a system called remote tuning. The next year in 2021, a Chinese manufacturer released a car equipped with Yamaha's first automotive sound system, and we were at our most confident when we heard from Yamaha Motor.
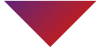
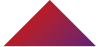
Vibrations from waves were stronger than we expected.I couldn’t believe my eyes when I saw the durability test results.

Ono:
I have a decent amount of experience with automotive speakers, so to be honest I wasn’t really worried. However, when I actually opened the lid, it was a total mess, but I’ll talk about that in the later part. One of the issues we faced at the beginning of development was that, unlike automotive and home speakers, which are used in limited spaces, the WaveRunner is used in open outdoor spaces. It is exposed to fresh water and seawater. To produce low-pitched sounds, the speaker must be placed in a box. In that case, the sealing is very important, and each part must be durable. I also thought that the challenge would be to achieve a sound pressure and sound quality that would be great even outdoors.
Ogata:
In terms of manufacturing, the most difficult part was also sealing. This time, we outsourced the manufacturing to a Chinese company. They had experience in producing regular IPX (the international standard for dustproof and waterproof treatment) and outdoor speakers, but they had no experience in producing speakers for use in marine sports. As we proceeded with product development, we realized that strict sealing that is not possible with regular IPX was necessary. We obviously had no experience in this area, so we received a lot of advice from Yamaha Motor. We also did a lot of research ourselves, including with the manufacturing contractor, and after repeated trial and error, we finally arrived at this point.
Suzuki:
We faced three challenges at the start of development. The first was reliability. The WaveRunner is a Personal Water Craft (PWC), so it is expected to run at high speeds, be used in saltwater, and even tip over. So the speakers must be usable in hot or cold environments, even if they were dropped into saltwater, and they also needed to be shock-resistant. Because they have no suspension, they are directly impacted when hit by a wave. We thought Yamaha Corporation didn’t have a track record of doing that with their products in the past, so the issue would be whether they could meet our reliability requirements. The second was cost. This may be a common image, but I had the impression that Yamaha speakers were sort of little expensive, premium, high-line. However, this time they would not only be installed in premium models, but also in standard-grade models, so we were concerned about whether they could be mass-produced at a cost that would allow many customers to use them. We heard people saying things like this within the company, and the costs rise rapidly during development with electrical components in particular. It may not be viable before mass production begins, so it was a challenge to manage it so that this does not happen. The third challenge was the concern about Yamaha Corporation becoming a completely new supplier. Generally, in the transportation equipment industry like ours, we contracted with suppliers that have a track record and technology in electrical parts. Even so, I thought we could achieve this by leveraging the connection of the tuning fork, and that something would happen as a result. Therefore, we wanted to do a collaboration between two Yamahas, even though it was an unlikely choice from the perspective of choosing an existing supplier.
Matsumoto:
The WaveRunner does not require a helmet like a motorcycle, and you can ride it as soon as you get your license. For example, on lakes in the U.S., if the environment is right, you can ride it continuously at speeds of over 100 kilometers per hour. Audio must be set according to the customer's usage environment. Especially at speeds of over 80 kilometers per hour, wind noise becomes very loud, so I think this was a major challenge not only for Yamaha Corporation but also for our body design.
Ono:
There were so many obstacles that I don't have enough time to discuss them all, but the two biggest obstacles were shock resistance and water resistance. There were two types of shock resistance tests: one for intermittent vibrations with small accelerations, like being constantly hit by waves, and one for a large, heavy impact. Honestly, in my experience, I thought that shocks were more difficult than vibrations, but for this product, the vibration test was much tougher. When I saw the first test results, I couldn't believe my eyes. It was broken in such a way that I thought the test conditions must have been wrong, or there was a mistake, or someone had hit it on purpose, so I thought it couldn’t be right. When I actually went on site, I saw that this had really happened, and that's when the real development started. Finally, we were able to suppress resonance and ensure vibration resistance quality by reducing the weight of the magnetic circuit of the speaker unit, which accounts for a very large part of the product's mass. It was a really brave decision to make major design changes in the middle of development, but when I think about it now, we weren’t mistaken. Another challenge was water resistance, which we struggled to overcome until the very end of development. We must have caused Yamaha Motor a lot of worry and inconvenience. A speaker is a product that creates sound by moving the air with the flexible movement of its diaphragm. In contrast, this box is a product that must not allow even a single drop of water to get in, requiring very high sealing performance. With the speaker in such a box, the speaker's diaphragm, which needs to be able to move flexibly, must be able to withstand all of the changes in pressure caused by the temperature of the air inside, and the water pressure from the outside. I believe this is where the difficulty of the issue lies. In order to solve this problem, we tried every possible measure to make the joints as strong as possible, while still not interfering with the movement of the diaphragm. I think we took measures to strengthen the speaker like never before in my career, and somehow managed to create a speaker.
Yamaki:
In sound production, the sound we have made so far has basically been sounds heard in the closed world of indoors, and we’ve been creating sound by using sound pressure that utilizes echoes from walls, but outdoors, all of that gets lost. From the beginning, our goal was to increase the sound pressure, but we were thinking about how to achieve that sound pressure outdoors, where it is so hard to hear sounds. Just to increase the volume with parameters, we need to have a lot of current flowing, but the first wall we hit was that the hardware specifications required a limited amount of current to flow. In the beginning, if we got good sound in a test, we would start by measuring the current. We often turned up the volume thinking that the sound pressure would increase by so much, but it was no good when we measured it. At our Toyooka office, although it is not completely anechoic, we have an anechoic chamber with very little echoing. Therefore, we brought speakers and equipment there and created a listening environment similar to that of a boat. While imagining what sound would be like outdoors, we made repeated visits and ran simulations, and repeatedly worked on the target sound and the current, which made the first half of the project difficult.
Ogata:
Yamaha Design Laboratory got involved from the design stage, so we focused closely on the design as well. To get the design right, we needed a resin molding die, but it was also very difficult to design. In the end, we decided it would be impossible to do this with a simple die, and we had to adopt a three-way sliding structure, and it was the largest we had ever made for an automotive speaker. This turned out to be worth it, and when we showed the finished product to Director Kawada of the Design Research Laboratory, he smiled with satisfaction and said, "Good job making it happen." That really stuck in my mind. Naturally, I think we created a design that will satisfy our customers.
Suzuki:
When we tried to ensure reliability, we were able to simulate things like vibration resistance and waterproofing to some extent, but we were unable to fully simulate many aspects of waterproofing. We repeatedly made things, breaking them and taking measures, or taking measures when they broke on their own, and we repeatedly tested them under different conditions until we found the cause. We found about ten points in the speaker structure where there was concern about waterproofing. We disassembled each one of them every time to investigate where the water was leaking from, and while some broke in the same pattern, others broke in different patterns. I think we probably broke hundreds of speakers. To put it in better terms, we were able to hone them. On the other hand, we obviously don’t have infinite time for development, and we had to explain each milestone within the company, with a schedule for when to release this model to the world. As a result, some of us thought that the project itself was impossible, and we would be better off canceling it, and that we could not complete it on schedule. Even so, we and Yamaha Corporation had no intention of giving up, and we kept conducting tests even while we were discussing the issue, so we were finally able to solve the problem. Another point we struggled with was that we were not modifying an existing product from Yamaha Corporation, so we had to create a new process. We visited the local factory many times, and with help from many people, we were able to identify the concerns and the causes. This goes back to what Ogata-san said earlier, but Yamaha Corporation came up with a very aggressive design. I think we could have made a design that was easier to manufacture, but they were particular about what kind of design to use, and we both knew that it had to be this one, so we just did it knowing that it would be difficult.
Matsumoto:
For grill designs, it’s preferable to have a relatively symmetrical design within a circle, but this time, they proposed a unique asymmetrical design. I expect it must have been difficult to manufacture. As a result, I think that we made a shape with a feeling of speed and agility that is integrated into the moving vehicle.
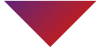
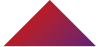
Having decided the concept, our goal for sound creation gradually came into sight.

Yamaki:
In parallel with these difficulties, or first of all, we started working on the sound production by deciding the sound concept. As we played test sounds, we thought about the outdoor situation, where the sound spreads out in all directions, and the fantastic entertainment of PWC. After exchanging opinions with experts from each department within the company, we came up with the following sound concept.
Fulfilled with sound under broad sky
Urging you to open the throttle
Feel the sound of outdoor music festivals
Once we had decided on the sound concept, I had the image of the sound I wanted to create fully formed in my head. How could I make this real? Drawing from Yamaha's track record and experience in sound and music, I thought that we could apply approaches from live sound and PA sound systems. Bass is the most prone to scattering, so it should have a solid core. The mid to high frequency range should be made using Yamaha's unique signal processing technology to create an effect where the PWC rider is surrounded by sound, and the vocals should be firmly positioned in front of her/him. Of course, the more I listened to it on the water, the more frustrated I became because I couldn't get the sound I wanted. As I mentioned before, we also struggled with the electric current. Still, I was able to gradually get closer step by step to the sound of the concept I was aiming for.
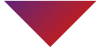
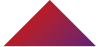
The combined strength of One Yamaha made it possible to complete the speaker.

Ono:
Many challenges arose during development, so even if we were able to overcome something along the way, I made a promise to myself that I would not get too excited or let my guard down. So, even when we cleared a test and got the approval for mass production, I couldn’t really believe it. However, when mass production started, the head of development and manager of Yamaha Motor came to our Chinese production contractor and gave us warm words of appreciation, which made me feel deep joy in my heart. I want our customers to feel the combined power of Yamaha Motor and Yamaha Corporation, the so-called One Yamaha. I'm embarrassed to say that I only rode the WaveRunner for the first time last month, thanks to Yamaha Motor's kind consideration. This was such an enjoyable experience that I wondered how such a world could exist. I would be happy if our products can contribute to improving the value of truly enjoyable and excellent products. My hope is that this will be an opportunity for us to work together on various projects.
Yamaki:
As I mentioned before, when I started sound production, I first created a sound concept. I was inspired by outdoor festivals, where people enjoy music outdoors. My approach was to create the same sense of realism and feeling of being at a live show surrounded by sound on the WaveRunner. When I visited the U.S., the person in charge at YMUS (Yamaha Motor Corporation, USA) praised it for its excellent sound. We worked with Yamaha Motor to create the sound, and once it was finished, we were able to test drive it with everyone involved. I felt confident that we could give our customers an experience of music playing on the water and everyone smiling. I think we were able to give shape to the concept that Yamaha Motor shared with us at the beginning of the development, "Beyond expectation superior music on the water," with a focus on the sound concept. It’s my very enthusiastic pleasure to be able to deliver this to our customers.
Ogata:
I later heard that it was unusual for Yamaha Motor to launch three models in parallel, the FX, VX, and GP series models. This was of course very difficult, but the fact that we were able to develop multiple models in parallel gave us great confidence, as a business unit and as individuals. I think the knowledge and skills we gained through this product development will be a great asset for us in our future Monozukuri (manufacturing). I also hope that we can apply this knowledge to future product development, including the next WaveRunner. This was a very valuable experience. Thank you very much.
Suzuki:
As for how I felt when the project was completed, like Mr. Ono said earlier, I felt that there was no clear timing for the completion of this project, and we were incorporating various measures the whole time, so I was left wondering when it will be completed. Once we moved to mass production, I felt a great sense of relief that development was finally over and we could deliver the product to our customers. On the other hand, I have been working intensively on this development for about three years since 2021, so I felt kind of sad that the development was finally over, which kind of contradicted my feeling of relief. My focus working on this audio was, of course, sound and design. There is probably no other thing that allows you to enjoy music while driving at 100 kilometers per hour. The biggest selling point is the loud sound that allows you to enjoy music even while driving, and the sound quality that matches the traits of Yamaha Corporation and that of the WaveRunner. It has an aggressive shape with no shame for its decoration, as well as a highly designed grill. And especially this time, we are proud of the Yamaha plated emblem in the center, so these traits will also give the rider a greater sense of ownership. Finally, while we started this initiative with the WaveRunner, I hope it will spread to other Yamaha products as well. I think a lot of regular customers do not know the difference between Yamaha Motor and Yamaha Corporation. However, the fact is that Yamaha Corporation's speakers offer great sound to customers. I hope that customers who purchase the WaveRunner will get a great impression of Yamaha.
Matsumoto:
In the future, I would like to keep promoting Yamaha Motor's Monozukuri and Yamaha Corporation's sound production with the Yamaha brand and identity. I don't think this is the end, so I want to continue to develop it and make it evolve into the next model and the one after that.
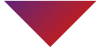
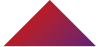
- ※
- Photographs may differ from the product at the time of shipment from the factory. They also include props used when shooting.
- ※
- Some photographs showing common features and technologies may use other models.