완전 자동 설정 라인 구축을 위한 레시피
Non-Stop, Operation Free 프로세스를 달성하기 위해서는 완전히 자동화된 라인이 필요합니다. Yamaha가 우리만의 비법을 소개합니다.
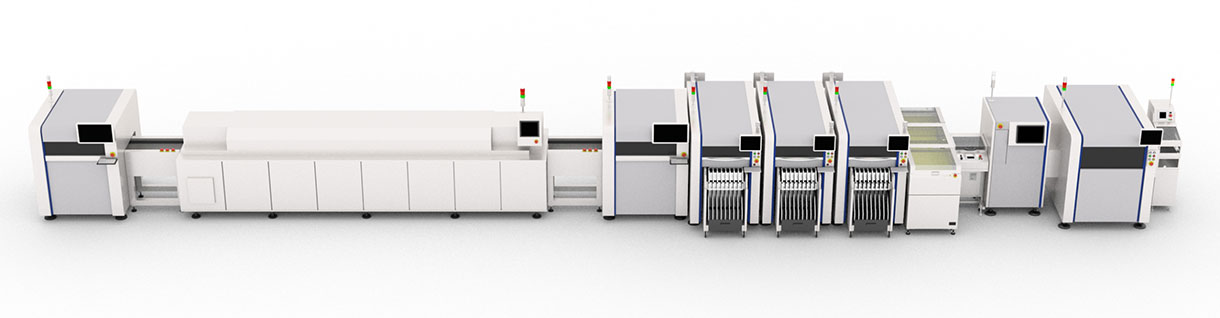
이런 문제가 없습니까?
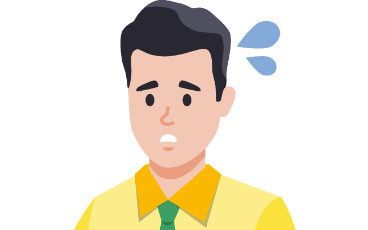
전환으로 인한 손실을 줄이고자 합니다. 그러나 시스템 사양으로 인해 효율성을 높이는 것이 그리 쉽지 않습니다.
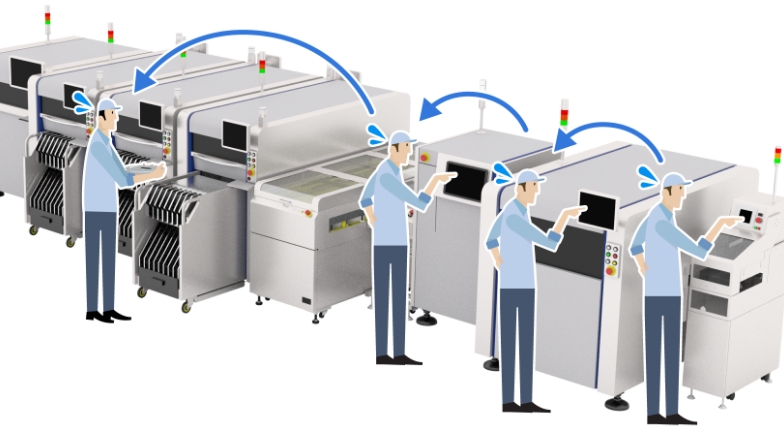
기계를 하나씩 교체하는 데 시간이 많이 걸립니다.
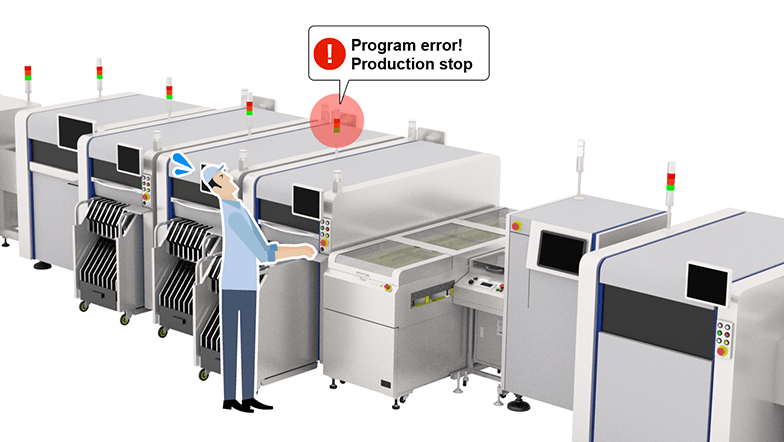
오류 메시지가 표시되고 잘못된 프로그램을 로드하여 시스템이 중지됩니다.
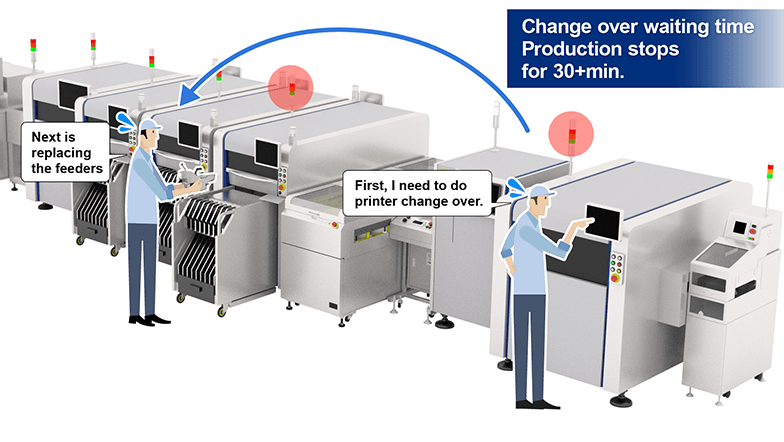
프린터의 체인지 오버를 마치더라도 마운터의 체인지 오버에 직면하여 시스템이 30분 이상 정지해야 합니다.
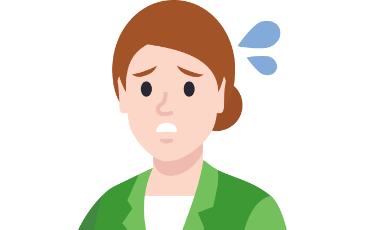
생산성을 0.1%라도 높이고 싶지만 방법을 모릅니다!
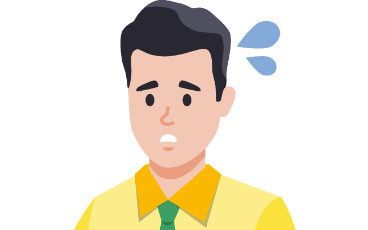
우리는 인시와 효율성을 개선하고 최소한의 작업자 수로 최대의 생산성을 달성하기를 원합니다. 하지만 어떻게!
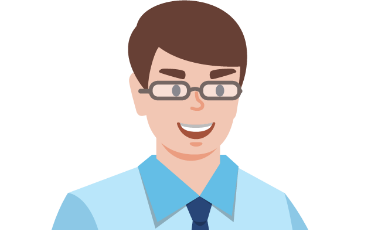
Yamaha는 이러한 문제에 직면한 고객에게 YAMAHA의 SMT 개념인 "1 STOP SMART SOLUTION "을 제안할 수 있습니다.
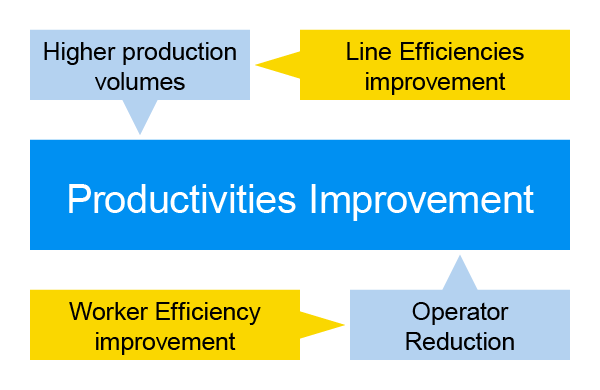
YAMAHA의 제안
당사의 1 STOP SMART SOLUTION", YAMAHA SMT 개념 "완전 자동화 라인을 위한 레시피"를 소개합니다.
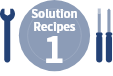
자동 설정
업스트림 머신에서 차기 모델의 레시피를 받아 생산성 향상
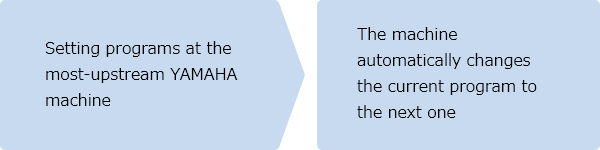
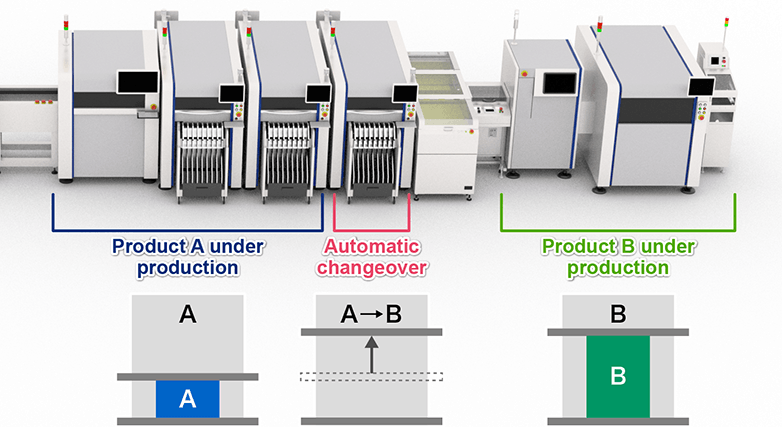
사례 1
최상위 머신에서 프로그램 지정
다운스트림 기계에서 자동 전환
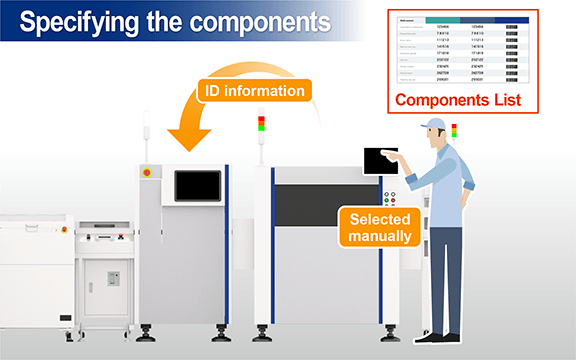
사례 2
최상류에 Kanban 설정
기계
다운스트림 기계에서 자동 전환
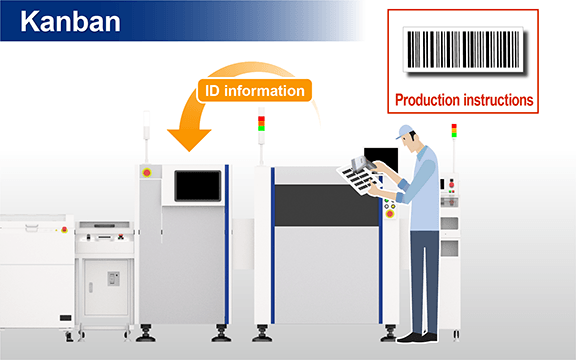
사례 3
가장 상위에 있는 Yamaha 기계 이전의 컨베이어에서 2D 바코드 판독
다운스트림 기계에서 자동 전환
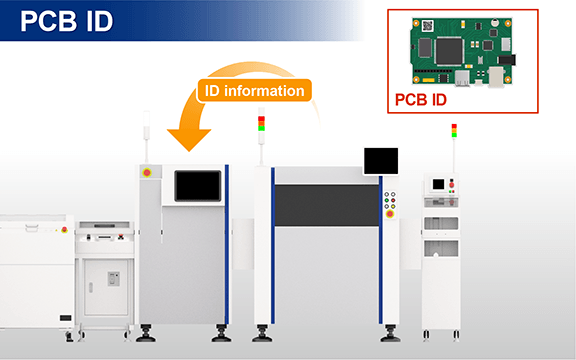
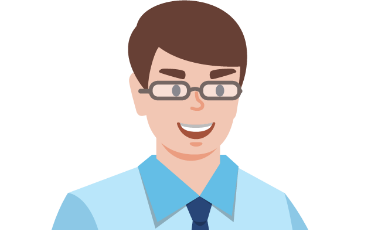
모든 기계를 Yamaha에 한 줄로 정렬하면 프린터에서 프리-리플로우 오븐까지 완전히 자동화된 라인을 얻을 수 있습니다.
장비를 다른 제조사의 장비로! 우리는 우리 기계에서 다른 제조업체의 기계로 통신하는 데 많은 경험을 가지고 있습니다.
컨베이어, 인라인 검사기, 리플로우 오븐 등 다른 제조사와 소통할 수 있습니다.
YAMAHA SMT Concept "1 STOP SMART SOLUTION에 솔루션이 있습니다!
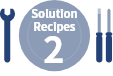
다른 회사의 장비를 연결하는 자동 설정
SMT 관련 주요 장비 제조사들이 함께 하는 모습을 경험해보세요! 다른 회사의 시스템 간에 전송된 설정으로 가용성이 향상됩니다!
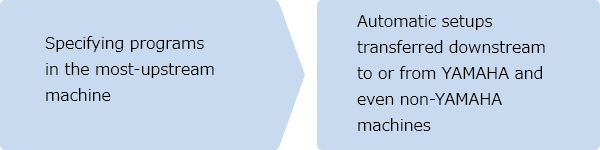
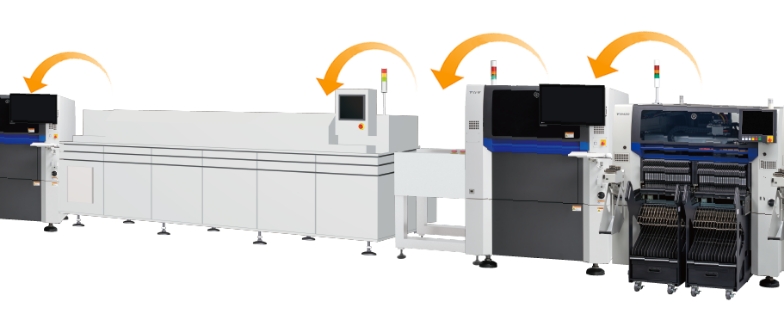
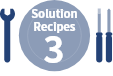
공통 설정 최적화
실장기의 전환 최소화
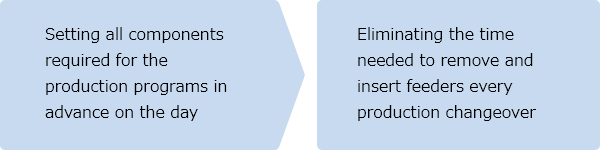
하나의 헤드로 다양한 부품을 장착할 수 있는 1 head solution과 최대 128개의 피더를 설정할 수 있는 YAMAHA 실장기 (YRM20)는 Common 설정에 매우 효과적입니다. 피더 교체 시간은 전환 시 30분 이상 소요될 수 있지만, 이 공통 설정 최적화를 사용하면 피더를 미리 설정하여 피더 교체로 기계 정지 시간을 없앨 수 있습니다.
헤드 교체가 필요 없는 광범위한 구성 요소
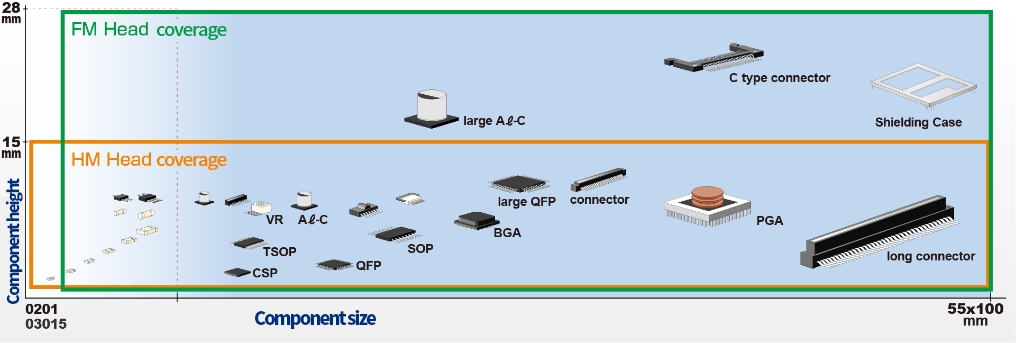
많은 부품를 한 번에 설정할 수 있습니다.
YRM20
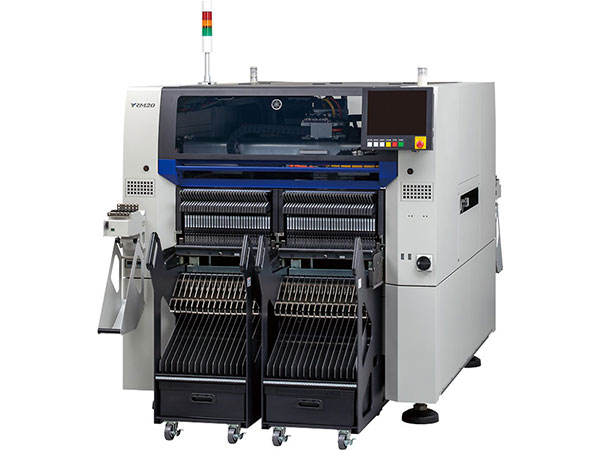
기계당 피더 용량은 최대 128 피더입니다(8mm 유형의 경우 변환).
작고 가벼운 피더 캐리지
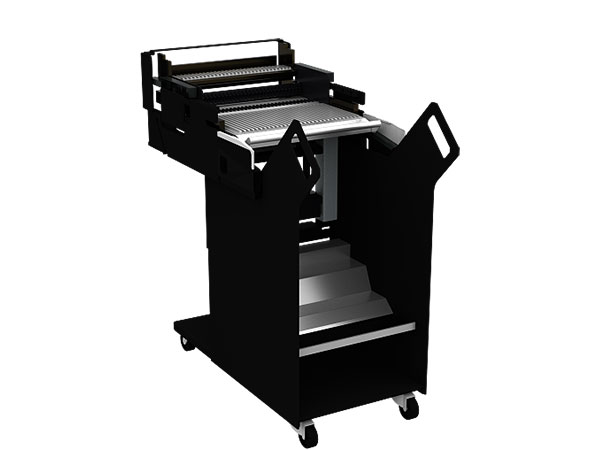
• 캐리지당 피더 용량은 최대 32피더(8mm용 환산)/figcaption>
30단 트레이 공급기(논스톱 교환형)
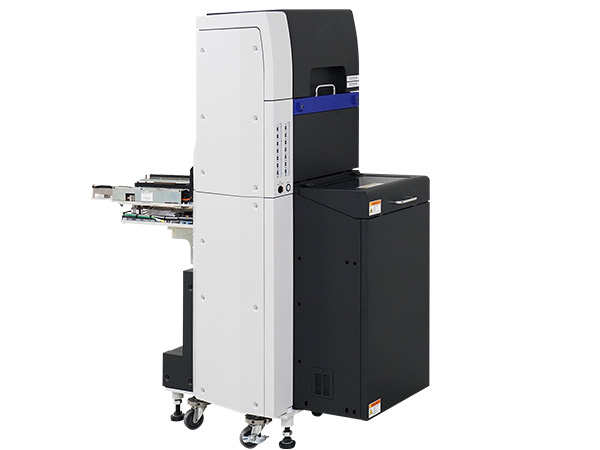
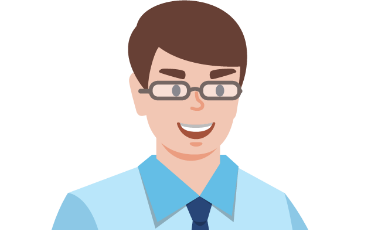
야마하만이 1 head solution으로 제공할 수 있는 공통 설정 최적화!
당사의 1 head solution은 헤드 교환(HM 헤드용) 없이 최소 0201mm에서 최대 55×100mm까지 부품을 지원합니다. 공통 설정을 기반으로 사전에 부품를 설정하면 운영자의 추가 설정 없이 다양한 제작 프로그램을 실행할 수 있습니다!
공통 설정 최적화는…
1라인에 설정할 수 있는 부품 종류의 수에 따라 PCB에 대한 최적의 Feeder 배열을 시뮬레이션하는 기능
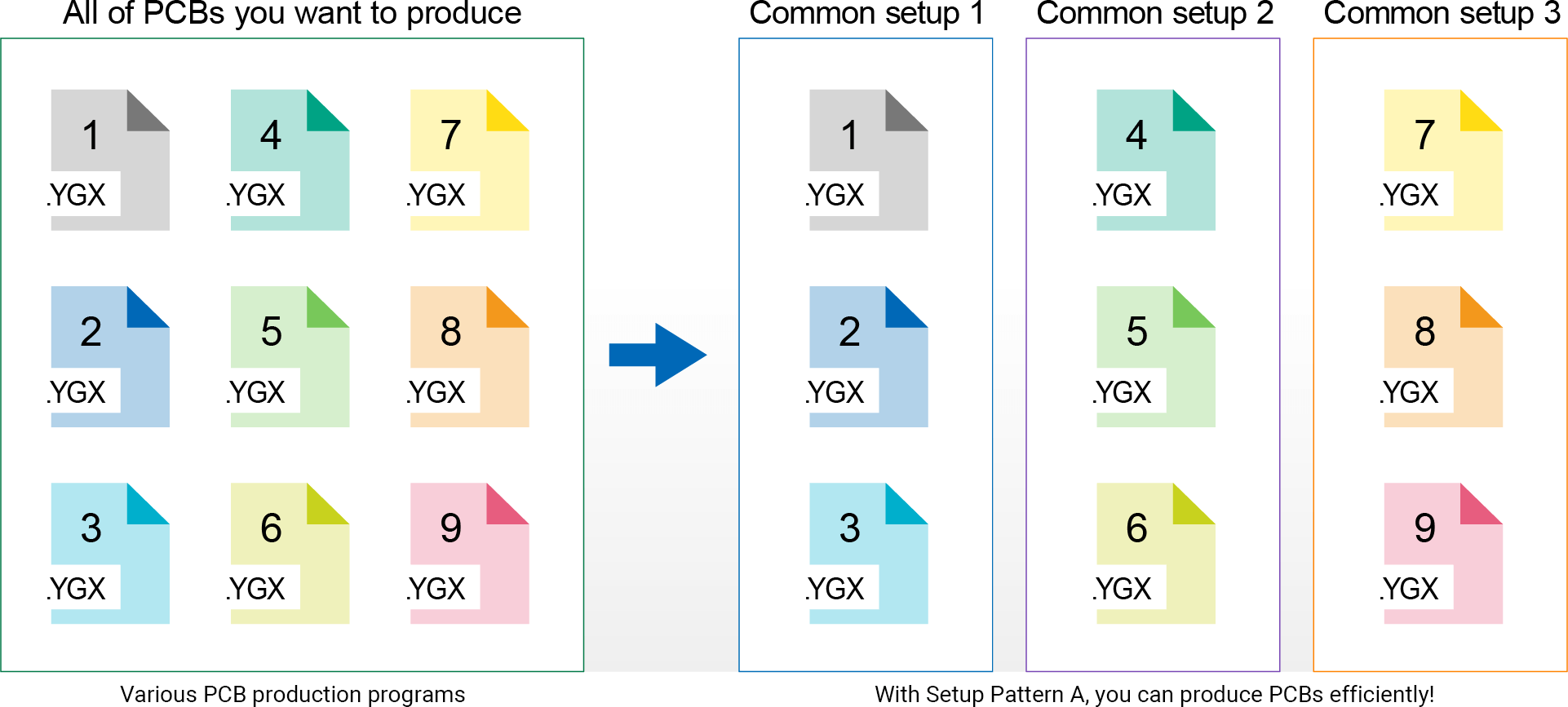
피더 캐리지 그룹 설정을 통한 공통 설정 최적화
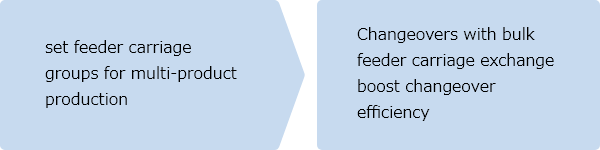
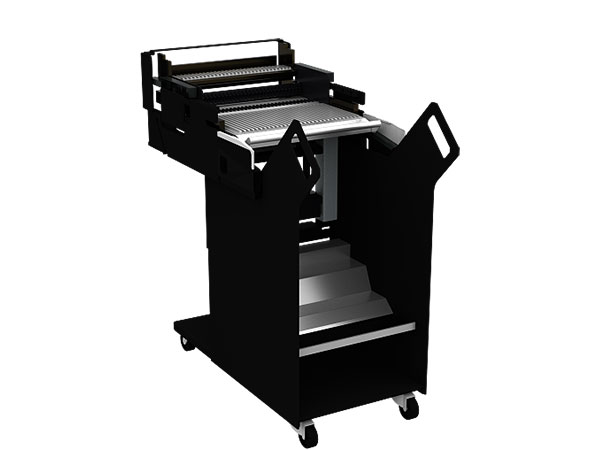
그룹화 기능은…
어떤 PCB가 어떤 PCB와 유사한지 자동으로 결정하고 그룹화하여 설정 수를 최소화합니다.
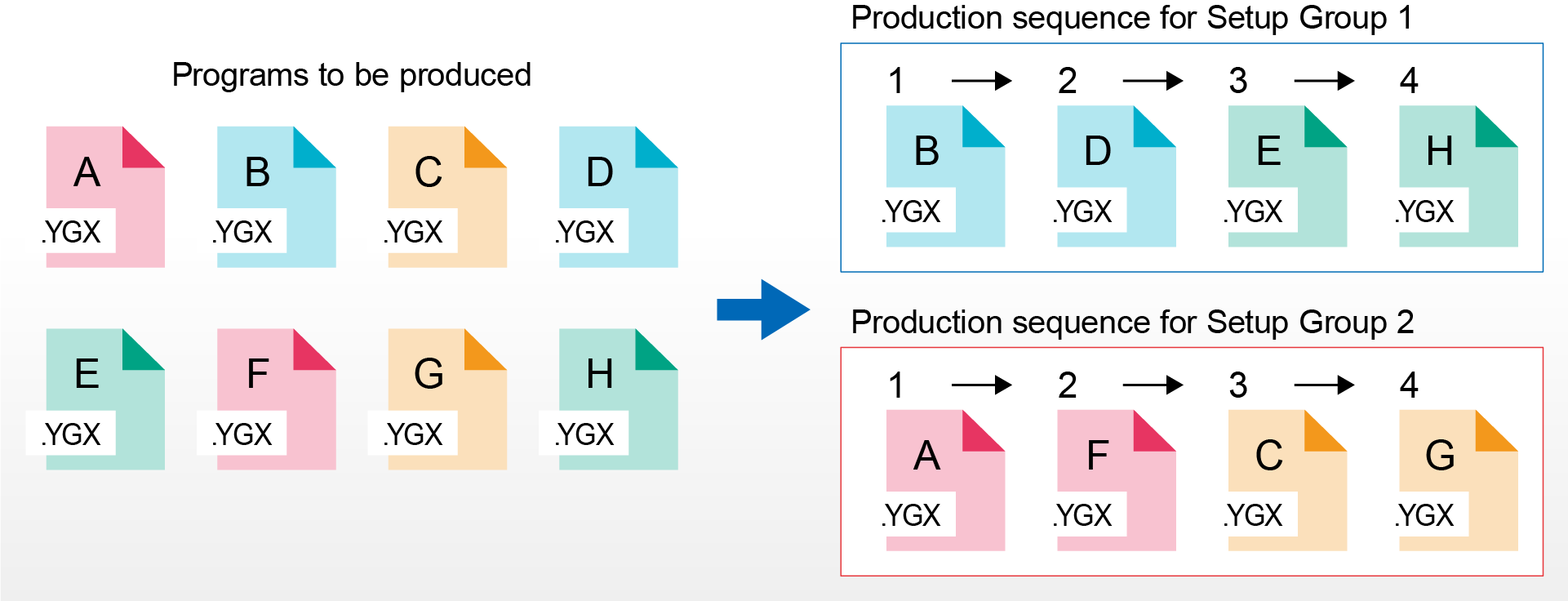
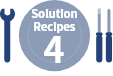
프린터의 완전 자동화된 설정 및 전환
프린터를 위한 완전 자동화된 설정 및 전환 제공
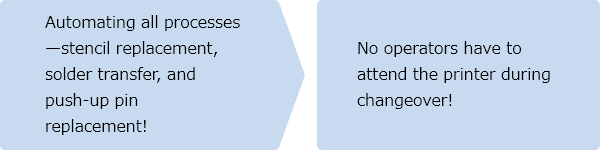
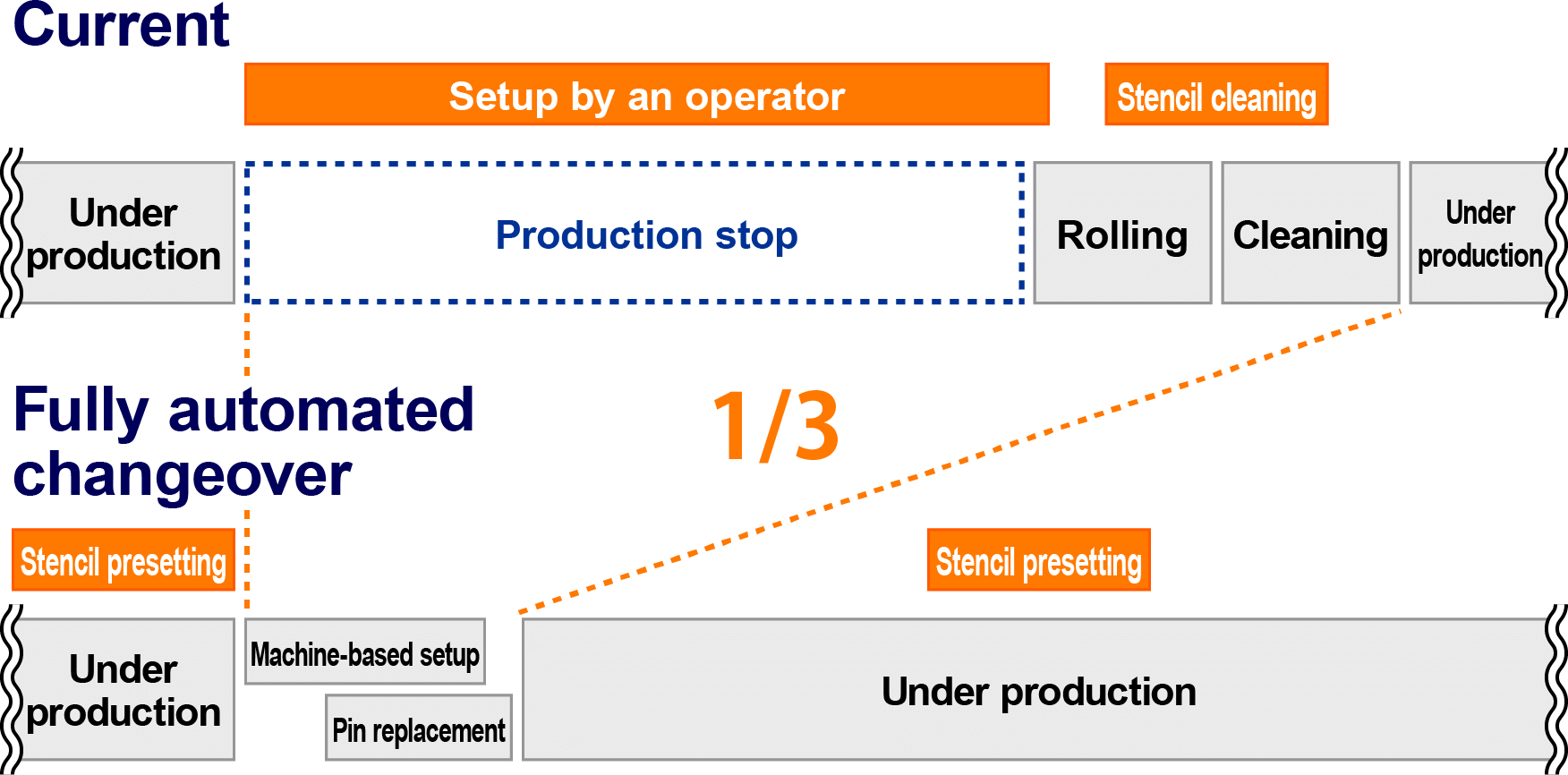
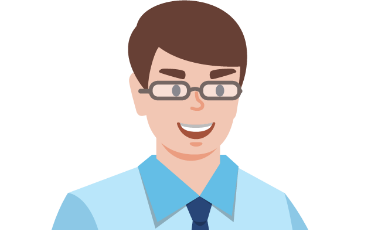
푸시업 핀의 자동 교체는 4개의 0을 제공합니다!
작업자를 귀찮게 하던 지그 보관 공간의 필요성을 없애고 지그 비용을 0으로 줄이고 지그 조달 및 배치를 없애고 핀이 잘못 배열되는 것을 0으로 줄입니다!
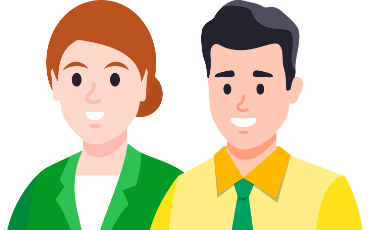
기계가 전환 프로세스를 수행할 수 있도록 하면 작업자의 작업량이 크게 줄어 1단계 = 1초 = 1엔으로 표시되어 생산성이 향상됩니다.
YAMAHA의 SMT 개념인 1 STOP SMART SOLUTION의 예를 소개합니다.
완전 자동 설정 라인 구축을 위한 레시피 공개!
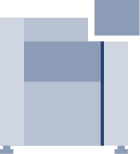
소개 예 1
산업용 장비용 PCB 생산 라인
전에

·짐을 싣는 사람
・YSP
・컨베이어
・YS24
・YS24X
・컨베이어
・YSi-12
・컨베이어
・리플로우 오븐
・냉각 컨베이어
・버퍼 컨베이어
・YSi-12(레이저 검사 기능 탑재)
・OK/NG 선별 컨베이어 ・언로더
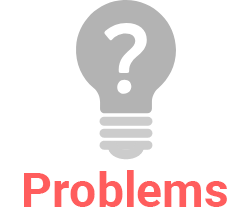
- 1.
- 장비 교체 및 프린터 교체와 관련된 프로그램 변경으로 인해 20분 정도 생산을 일시 중지해야 합니다.
- 2.
- 예를 들어 비숙련 작업자에 의한 플로팅 리드가 있는 불량 제품은 리플로우 공정을 거쳐 검사기로 유출된다. 그것들을 수리하는 것은 번거롭습니다.
- 3.
- 구성 요소는 제 시간에 다시 채울 수 없습니다. 이로 인해 장비가 중지되어 생산성이 저하됩니다.
후에

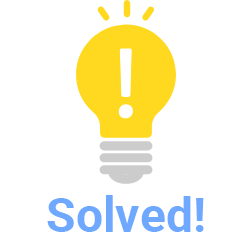
- 1.
- 해결!프린터까지 포함한 자동 설정으로 기존 20분 걸리던 전환 다운타임이 5분으로 단축되었습니다.
- 2.
- 리플로우 프로세스 전에 3D 검사를 도입함으로써 사용자는 플로팅 리드 및 기타 결함을 감지할 수 있어 평균 1ppm의 프로세스 중 결함률을 달성할 수 있습니다.
- 3.
- 웹 잔량 모니터링과 자동 로딩 피더의 조합은 구성품 재충전의 효율성을 개선하고 단기 기계 중단을 크게 줄였습니다.
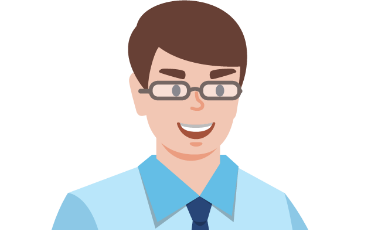
이 라인에 사용된 YAMAHA의 기술 포인트는…
기계: YSP10, YSi-SP, YRM20, 자동 로딩 피더, YSi-V
소프트웨어 프로그램: 자동 설정、대시보드、웹 잔량 모니터링
프린터: 완전 자동 전환 지원, 12온스 주사기 PSC, 인쇄 위치 이동 피드백
검사기 : QA옵션, 모바일판단기능, 공정상관
자동 설정, 자동 로딩 피더 등의 도입으로 생산 중단 시간이 상당히 단축되었습니다. 또한 Reflow 공정 전 3D 검사를 도입하여 Reflow 공정 후 불량률을 최소화하였습니다.
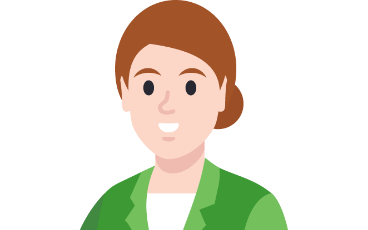
YAMAHA의 주요 이점은 높은 생산성을 제공하면서 손쉬운 전환을 제공한다는 것입니다.
칸반 설정 + 전송 모드에서 자동 설정을 도입했습니다. 주요 프린터에서 생산 품목의 바코드를 읽기만 하면 SPI 및 실장기까지 자동 설정이 가능하여 대기 시간 동안 생산할 PCB를 처리하고 다른 작업을 수행할 수 있습니다. 이로써 설정 시간이 상당히 단축되었습니다. 또한 피더나 트롤리를 교체하지 않고도 전환을 수행할 수 있게 해주는 1 head solution의 특성을 활용하는 최적화된 공유 설정을 사용합니다.
또한 리플로우 공정 전에 3D AOI(YSi-V)를 도입함으로써 대부분의 결함을 리플로우 공정 전에 감지할 수 있었습니다. 그 결과 비숙련 작업자가 개입하더라도 공정 중 불량률이 1ppm 미만으로 줄어들어 납땜 인두를 사용하는 거의 모든 수리 작업이 필요하지 않습니다.
대시보드 및 i-ProDB에서 사용할 수 있는 프로세스별 프로세스 상관 관계를 통해 원인을 식별할 수 있는 결함의 수가 증가했습니다. 이는 품질 향상에도 기여했다고 생각합니다.
부품 리필과 관련하여 웹 잔량 모니터링은 라인의 대형 화면 또는 전체 라인의 모바일 장치에 부품 잔량 정보를 표시합니다. 또한, 자동 로딩 피더의 조합 사용으로 효율적인 부품 리필이 가능해졌으며, 그 결과 리필 지연으로 인한 라인 중단이 거의 발생하지 않았습니다.
생산량이 증가함에도 불구하고 라인당 작업자 1명으로 생산을 계속할 수 있었던 것은 YAMAHA의 풍부한 기능 세트가 기계 생산성을 크게 높인 덕분이라고 생각합니다. 우리는 보다 효율적이고 고품질의 생산 라인을 구축하기 위해 효과적인 기능을 계속 도입할 것입니다.
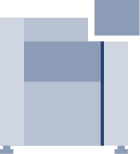
사례 연구 #2
연중무휴 24시간 하이 믹스 대량 생산을 하는 자동차 고객
전에

·짐을 싣는 사람
・PCB 클리너
・YGP(확장 컨베이어 포함)
・SPI
・YG100
・YG100
・YG100
・리플로우 오븐
・쿨링 버퍼 컨베이어
・언로더
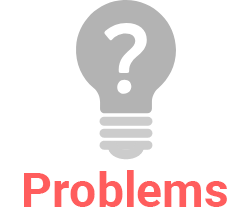
- 1.
- 공정의 평균 불량률은 15ppm이며, 라인당 작업자가 1명뿐이어서 불량 원인 파악 및 개선이 어렵다…
- 2.
- 설정을 변경하는 데 시간이 걸리고 가용성이 손실됩니다.
- 3.
- 제 시간에 부품를 보충할 수 없기 때문에 가용성 손실.
- 4.
- 한 작업자가 로더/언로더의 매거진 설정, 땜납 보충 및 프로그램 전환을 담당하는 경우 각 작업자가 취하는 단계 수는 하루(교대당) 거의 20,000단계입니다.
후에

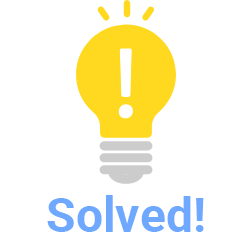
- 1.
- 공정 중 불량률은 평균 1.00ppm 미만입니다. 가장 좋은 달에는 비율이 0.1ppm 미만이었습니다(한 달에 하나의 공정 불량만).
- 2.
- 전환은 완전히 자동화됩니다. 로더가 2D 코드를 읽으면 자동으로 전환이 수행됩니다. 프린터 전환은 이제 YSP10에 의해 완전히 자동화되었으며 2.5~4.5분 내에 완료됩니다.
- 3.
- Auto Loading Feeder를 도입하여 구성품 보충 시 가용성 손실을 크게 줄였습니다.
- 4.
- 자동화된 땜납 보충 및 완전 자동화된 전환으로 프린터 방문 횟수를 80% 줄였습니다. 그 결과 작업자 단계 수가 20% 감소했습니다.
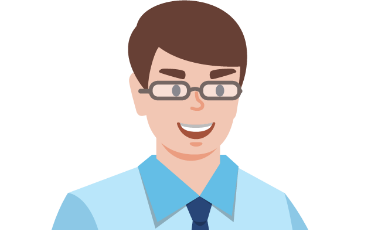
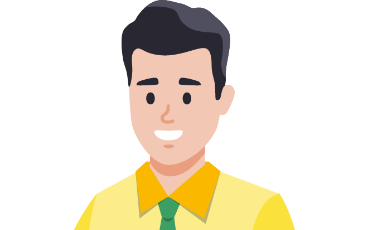
YAMAHA의 주요 이점은 혼합 생산에서도 빠른 속도입니다!
우리는 4개의 라인을 가지고 있으며 그 중 하나는 YAMAHA 라인이지만 어떤 경우에도 다른 라인보다 빠릅니다.
업데이트 전 YAMAHA 라인은 다른 라인과 거의 동일한 생산 능력을 가지고 있었습니다. 그러나 YSM20R을 도입한 이후로 공간이 변하지 않았음에도 불구하고 용량은 거의 2배가 되었습니다. 또한 운영자 수는 변경되지 않습니다. 부품 보충 빈도가 거의 2배 가까이 증가했지만 Auto Loading Feeder를 사용하여 부품이 떨어지는 경우를 최소화했습니다. 그 결과 전체 장비 효율이 90% 이상인 YAMAHA 라인을 운영할 수 있습니다.
또한, 공정 불량도 1/10 이하로 감소시켜 유지하고 있습니다.
중요한 점은 pre-reflow 프로세스에서 3D AOI인 YSi-V를 도입했다는 것입니다.
YSi-V가 결함을 감지하면 즉시 실장기를 사이클 스톱하여 결함의 원인과 문제를 일으킨 원인을 확인합니다(QA 옵션). 이 배치 작업은 불량품의 대량을 제거하고 작업자가 노즐 유지 보수와 같은 개선 조치를 취할 수 있게 하여 품질을 크게 향상시켰습니다.
결함이 줄어들어 더 이상 공급자를 귀찮게 할 필요가 없으며 현장, 생산 엔지니어링 부서 및 관리 부서의 모든 사람들이 만족합니다. 물론 사장, 부장, 다른 임원들도 기뻐한다.
우리는 현장에서 Yamaha 장비를 계속 사용하여 라인을 더욱 개선할 것입니다!
그리고 더! "멈출 수 없는" 및 "작업이 필요 없는" 솔루션을 위한 재료의 자동 보충!
1.12온스 주사기 PSC가 있는 프린터
이것은 인쇄 품질에 영향을 미치는 솔더 롤링 직경을 안정화합니다. 새로 개발된 12온스 주사기는 장기간 논스톱 생산이 가능합니다.
2. 자동 로딩 피더가 장착된 마운터
자동 로딩 기능으로 누구나 쉽게 테이프 부품 부품을 언제든지 쉽게 다시 채울 수 있습니다. 테이프 로딩 시간은 약 5초 정도로 짧습니다. *
*테이프 공급 시작부터 픽업 준비가 될 때까지.
3. 논스톱 트레이 보충 기능이 있는 마운터
실장기는 팔레트 또는 매거진에서 트레이 부품을 논스톱으로 공급할 수 있도록 지원하므로 기계를 멈추지 않고도 효율적인 트레이 부품 공급 및 생산이 가능합니다.
4.스택 공급액 장착 마운터(스틱 피더, 스태킹 트레이 피더 등)
우리는 고객 요구 사항 및 대상 부품에 따라 스택 스틱 피더, 스택 트레이 피더 등을 지원하는 데 많은 경험을 보유하고 있습니다. 보다 자세한 사항은 당사 대리점 또는 아래의 문의 페이지로 문의해 주시기 바랍니다.
당사의 라인 구축 지원 엔지니어가 귀하와 상담할 준비가 되어 있습니다.
YAMAHA의 라인 구축 지원 엔지니어는 YAMAHA 장비 사용 여부에 관계없이 고객에게 무료 상담 서비스(전화, 이메일, 방문, 쇼룸 견학 등)를 제공합니다.