생산 라인의 만족 수량 x 품질 x 노동력 절감: SMT 솔루션
Yamaha의 SMT 장비로 구성된 생산 라인을 채택하여 구현할 수 있는 다양한 SMT 솔루션을 소개합니다.
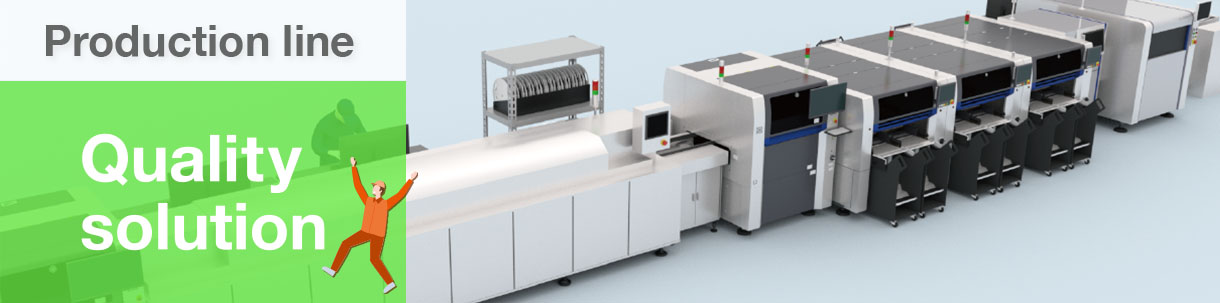

뛰어난 픽업 및 마운팅 성능을 유지하고 픽업률이 떨어지는 것을 방지하는 솔루션
생산 라인에서 가장 흔히 볼 수 있는 오류는 마운터 픽업 오류입니다.
1 STOP SMART SOLUTION 픽업 및 장착 오류를 최소화하는 솔루션을 제공합니다.
다층보정을 통한 안정적인 픽업 및 마운팅
Yamaha 마운터에는 안정적인 부품 픽업과 안정적인 마운팅을 달성하기 위한 다양한 보정 기능이 있습니다.
생산 중에 시스템의 수정 표시를 자동으로 스캔하여 실장기 항상 높은 픽업 및 마운팅 성능을 제공합니다.
다중 정확도 보상 시스템 MACS
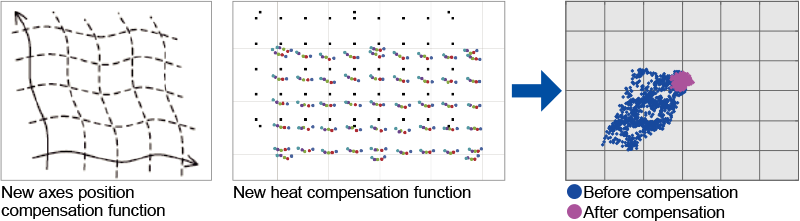
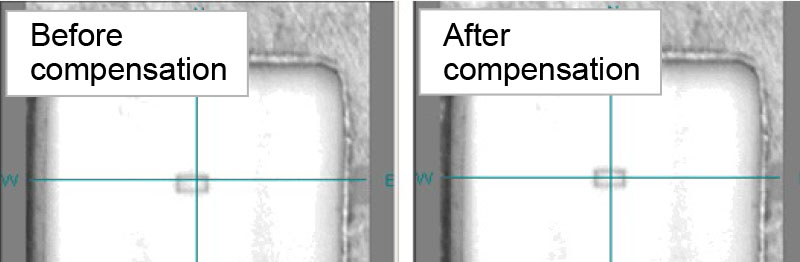
대시보드의 고급 픽업 오류 분석
오류가 많고 오류율이 높은 부품부터 시작하면 Pickup 오류를 보다 효과적으로 개선할 수 있습니다.
1 STOP SMART SOLUTION 개선이 필요한 부품 무엇인지 빠르게 파악하고, 부품 인지, 헤드인지, 피더인지 픽업 오류의 원인을 파악할 수 있는 기능을 포함하고 있습니다.
대시보드 분석 중
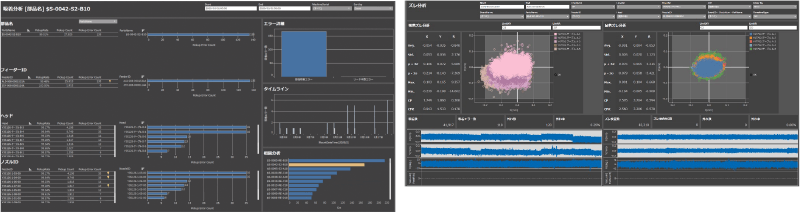
All Image Tracer
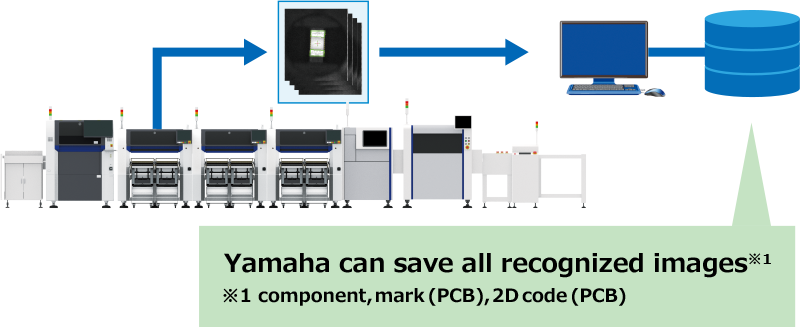
1. 자동으로 노즐 상태 체크로 노즐 상태를 적절하게 유지
높은 픽업 속도를 유지하려면 노즐을 올바른 상태로 유지하는 것이 중요합니다.
Yamaha 마운터에는 에어 채널을 청소하고 픽업의 열화를 방지하기 위해 정기적으로 노즐을 불어주는 블로우 스테이션이 있습니다. 노즐 상단의 스프링의 미끄럼을 노즐의 이미지와 함께 확인하여 지속적인 생산을 위해 항상 올바른 상태를 유지합니다.
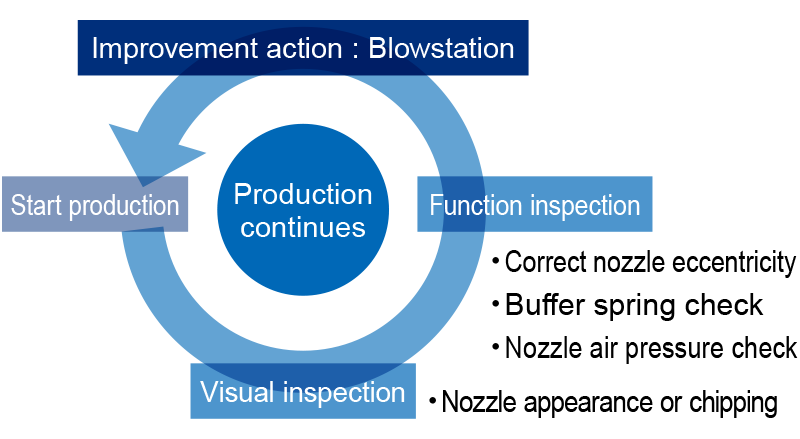
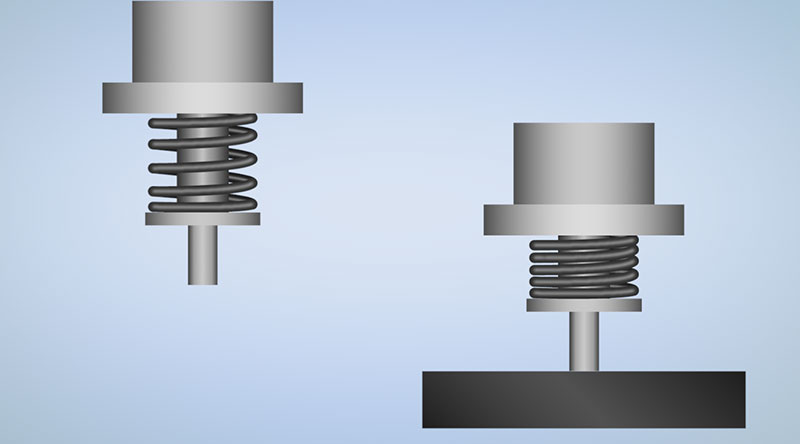

높은 솔더 인쇄 정확도 및 유연성
인쇄 공정은 생산 라인에서 대부분의 불량을 유발한다고 합니다.
Yamaha의 납땜 인쇄 솔루션은 이 문제를 해결합니다.
받음각이 가변적인 스퀴지 3S 헤드
Yamaha 프린터의 독창적인 가변 각도 스퀴지 3S 헤드는 광범위한 인쇄 조건을 충족할 수 있어 모든 유형의 PCB에서 뛰어난 납땜 인쇄 품질을 실현합니다.
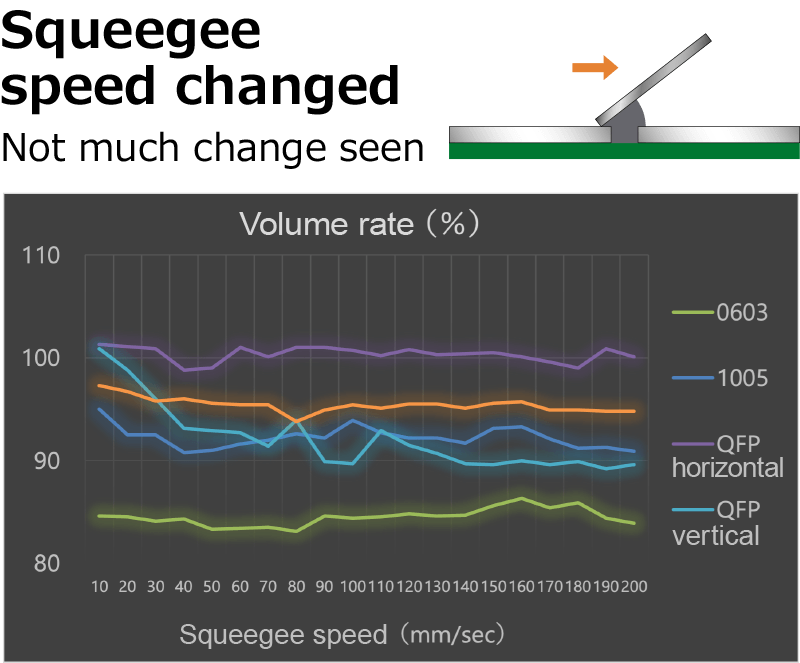

SPI와 연동된 자율 제어로 고정밀 인쇄
SPI와 연동하여 인쇄 정보를 실시간으로 프린터에 피드백합니다.
즉, 생산 Lot별 생산 PCB의 마무리 정확도 변화에 따라 뛰어난 인쇄 정밀도를 자체적으로 유지할 수 있습니다.
인쇄 위치 피드백: 인쇄 위치 안정화
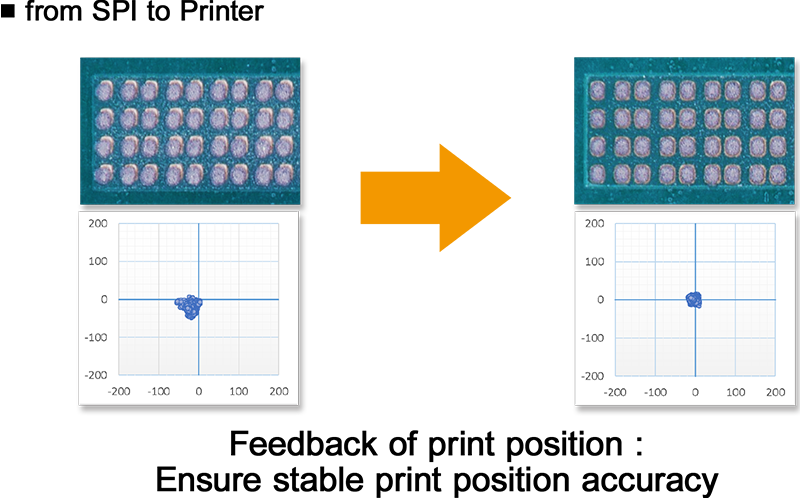
청소 피드백: 브리징 방지

엔지니어링 방법 및 주변 재료에 대한 광범위한 전문 지식
고품질 솔더 인쇄의 경우 솔더 및 금속 스텐실과 같은 올바른 주변 재료를 선택하고 설계하는 것이 중요합니다.
Yamaha는 이 분야에 대한 광범위한 지식과 경험을 보유하고 있으며 제조업체와 함께 땜납 및 금속 스텐실을 공동으로 평가할 수 있습니다. 또한 문제를 해결하는 데 도움이 될 수 있는 정보를 공유하기 위해 개별 인쇄 세미나를 제공합니다.
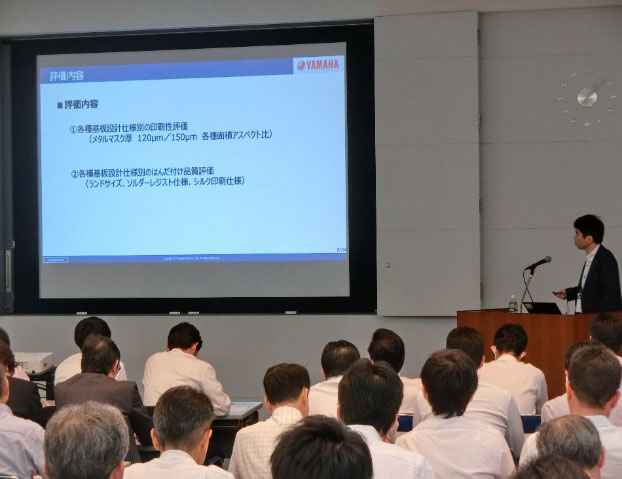

결함이 발생하는 즉시 정확하고 쉽게 결함 원인을 식별합니다.
결함이 발견되면 라인을 멈추고 원인을 파악하는 데 오랜 시간이 걸리고 상당한 생산 손실이 발생합니다. 반대로 생산을 계속하면 결함이 있는 제품이 많이 발생합니다.
Yamaha의 다양한 검사 시스템은 이러한 문제를 해결할 수 있습니다.
Reflow 전 검사를 통한 대량 불량 방지
더 나은 품질을 달성하기 위해 점점 더 많은 고객이 사전 리플로우 검사를 채택하고 있습니다.
리플로우 전 검사는 솔더가 응고되기 전에 순차적인 결함을 감지할 수 있어 리플로우 후 대량의 결함이 발생하는 것을 방지할 수 있습니다.
플럭스가 문자를 흐리게 하여 리플로우 후 검사 중에 문자를 감지할 수 없게 만드는 경우의 예
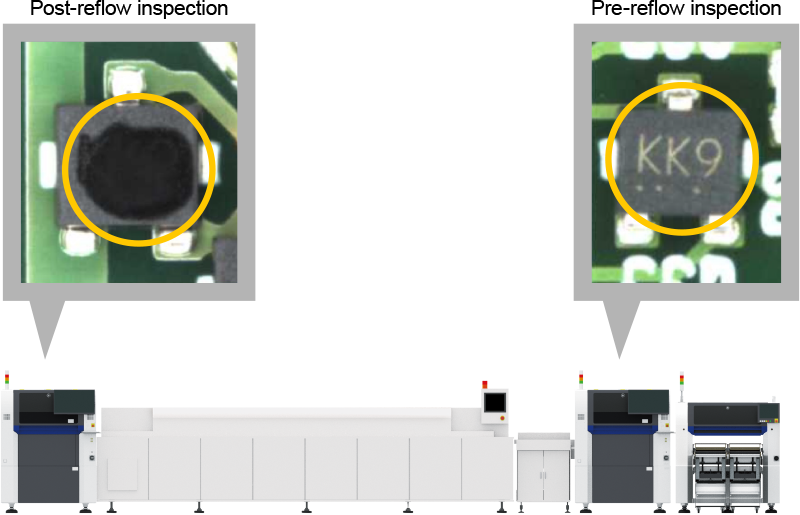
리플로우 전 자동 결함 감지를 통해 초도품 확인을 자동화하고 수리 작업 프로세스를 방지하며 폐기 손실 비용을 줄일 수 있습니다.
리플로우 전 극성 검사 및 특성 검사는 검사 시스템에 의한 오호를 줄여 미조정 비율을 개선합니다.
불량원인 규명으로 공정불량 예방 및 전 공정 품질향상
검사 시스템과 실장기 연결하여 불량 방지
결함을 발견했을 때 프로세스와 그 원인을 조사하는 것은 번거로운 작업입니다.
Yamaha는 실장기와 AOI를 연결하기 때문에 결함이 감지되면 결함을 생성한 실장기 즉시 중지되어 더 많은 결함이 발생하는 것을 방지하고 결함이 발생한 이유를 식별하는 데 도움이 됩니다.
QA 옵션
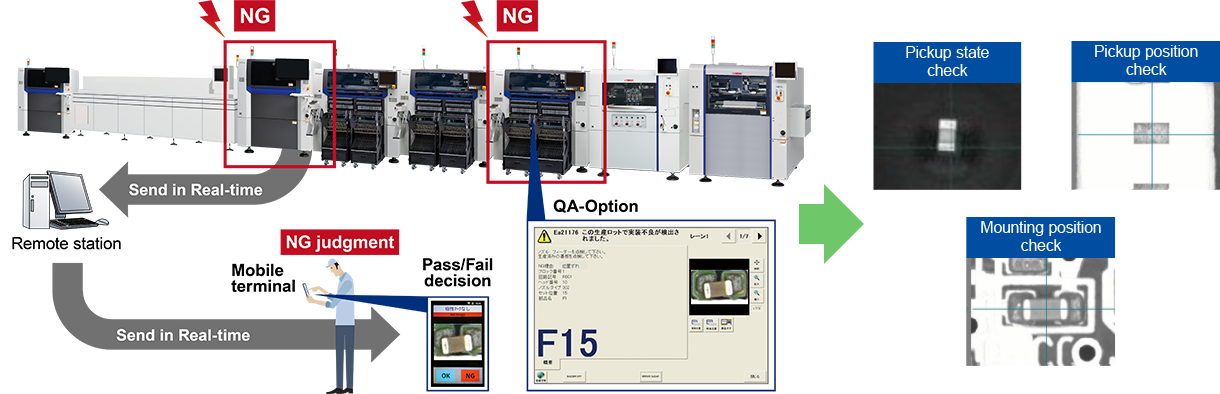
공정별 이미지 비교를 통한 불량원인 규명
리플로우 후 불량 PCB가 발견되면 어느 공정에 책임이 있는지 파악하기 어려웠기 때문에 생산 개선이 어려웠다.
개선 속도를 높이기 위해 1 STOP SMART SOLUTION 모든 프로세스의 이미지를 비교하고 결함이 나타나기 시작한 프로세스를 식별할 수 있습니다.
프로세스 상관관계
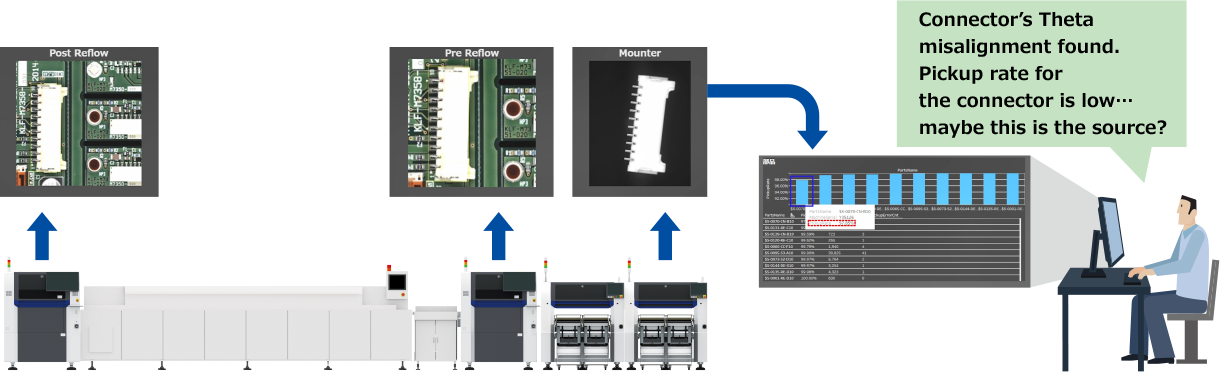
[결함 원인 규명 예시]
부품에서 발견된 이물질
[원인]
원인은 애초부터 부품에 달라붙은 이물질이었다.
[측정하다]
결과를 구성 요소 제조업체에 피드백
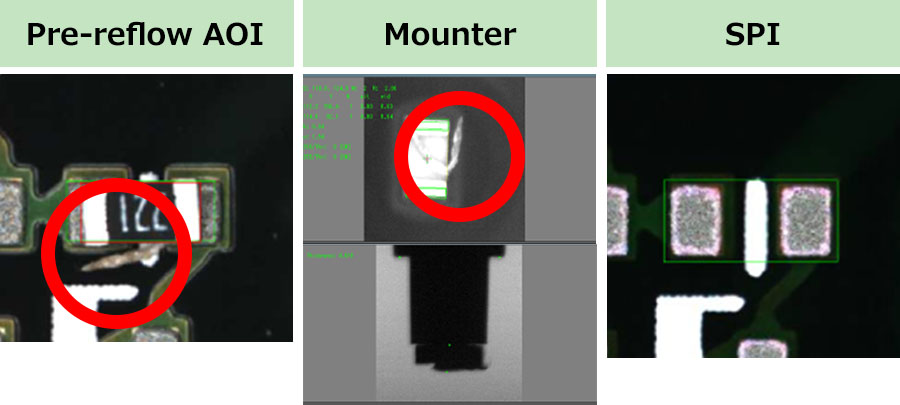
[결함 원인 규명 예시]
부품 거꾸로되었습니다.
[원인]
결함은 릴을 교체할 때 발생한 것으로 파악됐다. 접합 실패가 원인이었다.
[측정하다]
접합에 대한 교육을 다시 실시했습니다.
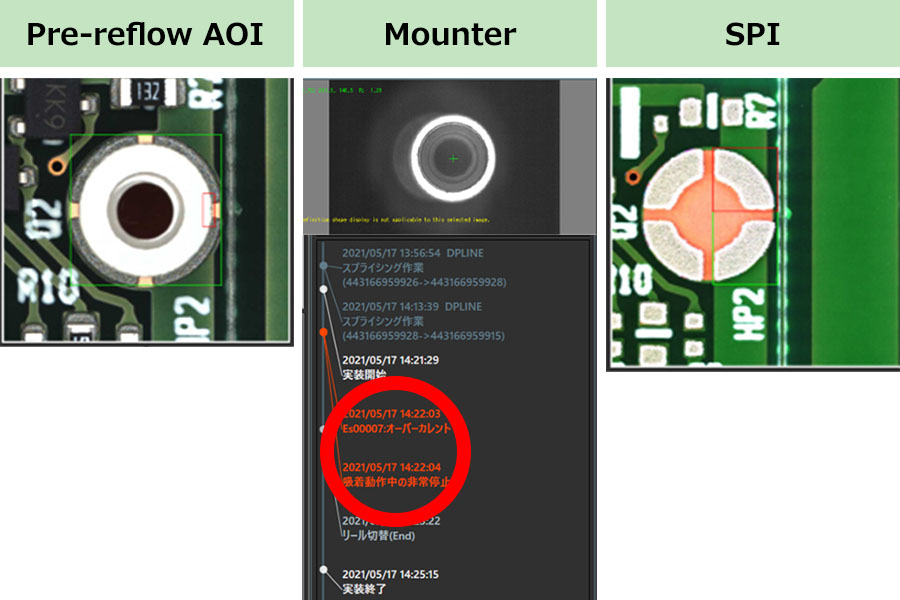