Sheer craftsmanship in every finish
Creating the complex freeform surfaces that make up the structure of a boat begins with "male molds" that are machined with large 3D NC lathes, which are then covered with layers of FRP to form "female molds."
Large boats that exceed 20 m in length comprise of multiple molds, but this requires an extremely advanced molding technique to achieve the high level of precision where the molds are joined.
The boat is completed by applying layers of FRP mat and cloth onto the female mold. Yet even with the use of reinforced molds, its sheer size means that the mold itself can buckle under its own weight, or the boat can end up slightly damaged or faulty during the layering process.
Making sure that the mold is as perfect as possible requires daily inspections that only a highly skilled “specialist” can achieve.
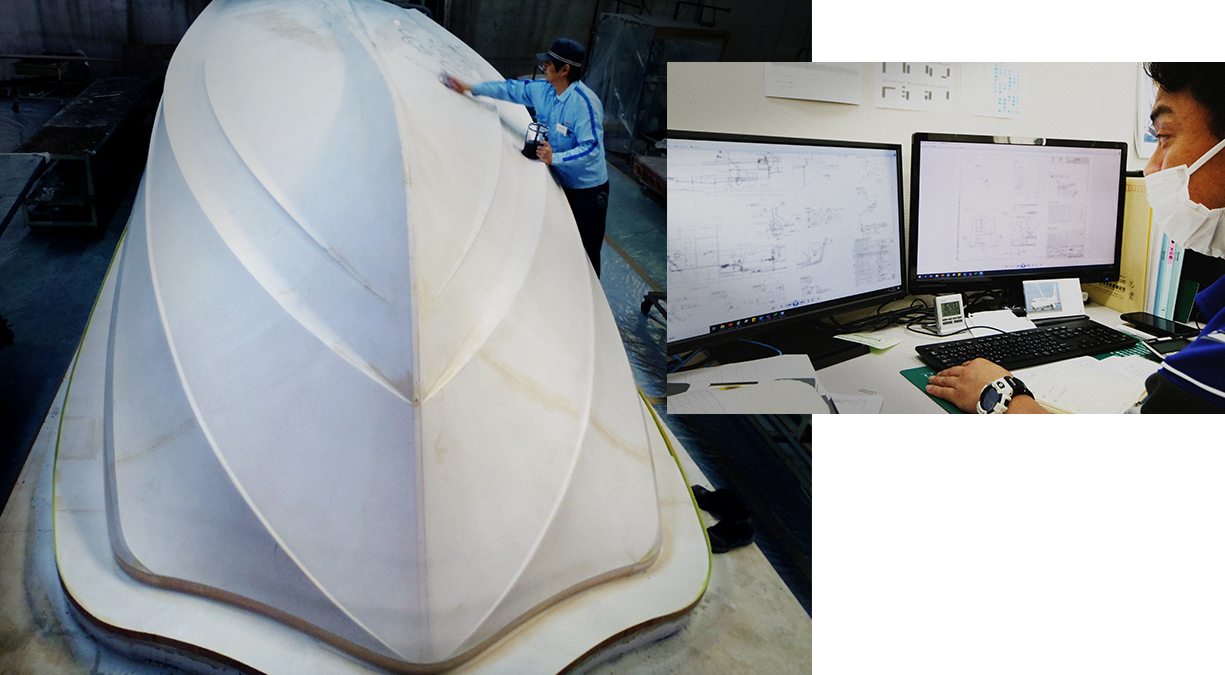
Machining the male molds through to producing the female molds is performed entirely with machines at dedicated plants. The shipbuilding plant machines the female molds that it receives to a level of finish that is on par with glass lenses.
Even the slightest imperfection can cause the gelcoat to start peeling off. To avoid this, the mold surface is polished to a mirror-like finish by shining light over the surface.
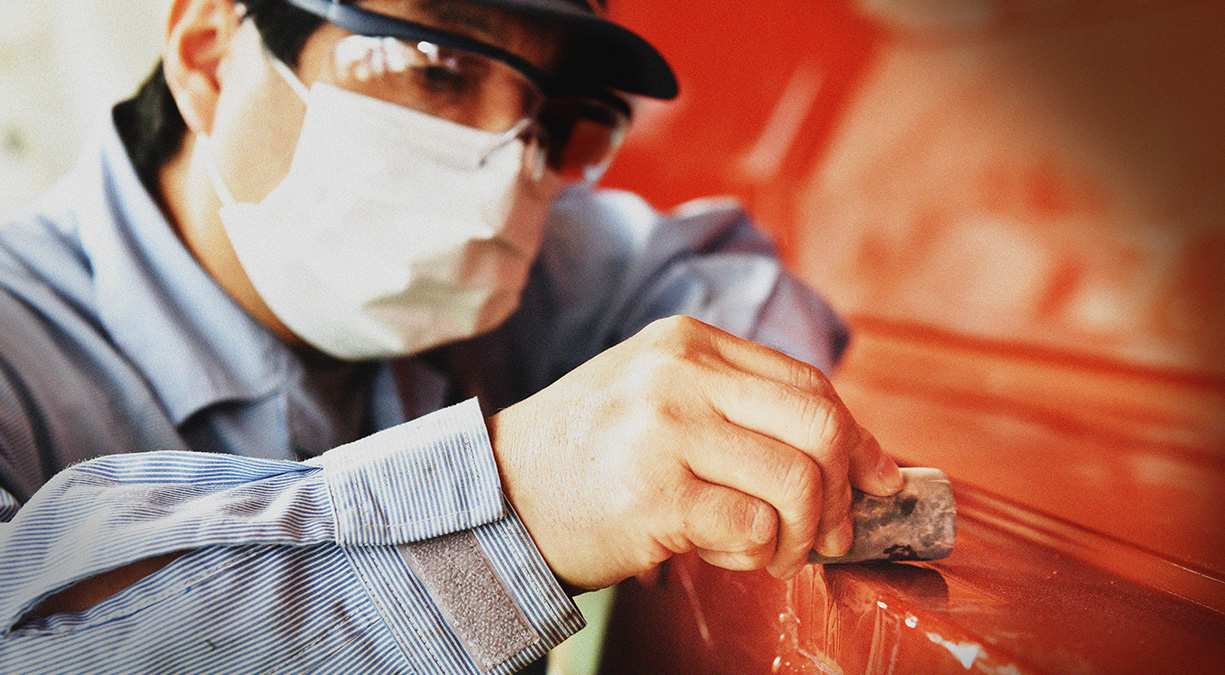
Unlike flat surfaces, identifying distortions along curved surfaces depends on factors like what angle the surface is viewed from and the way light is reflected, a feat achievable by only the most highly skilled specialists.
Each curved surface is viewed from a number of different angles, with the surface continuously buffed depending on how light shone on the polished mold reflects off.
Six layers of glass coating are applied to the highly polished mold to completely fill up any micropores—only then is the gelcoat applied.
There are no figures that can be used to represent such imperfections, and the work is only complete when the specialist is completely happy with the finish.
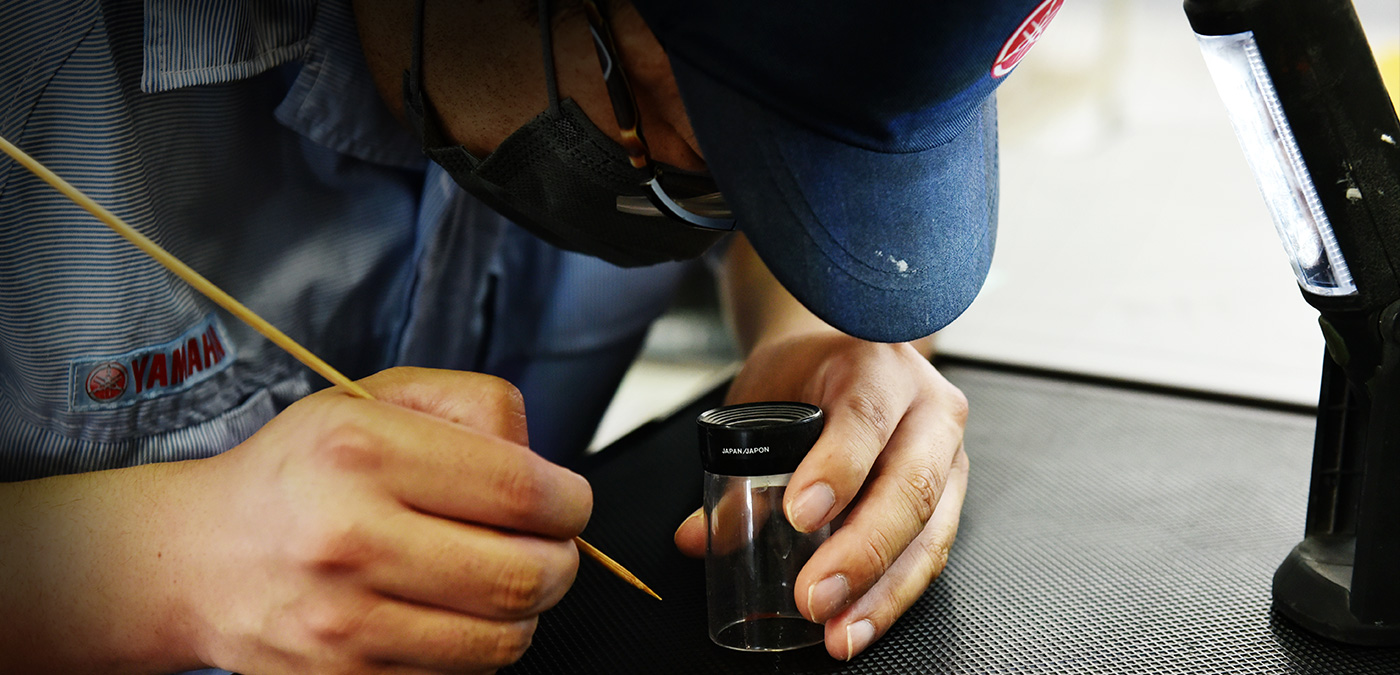