Too little or too much is unacceptable
The exterior of the boat is made by layering resin-saturated FRP cloth and mat over the mold. The outside of the hull can be subjected to immense acceleration forces of up to 20 G when skipping across waves.
Running along the bottom of the boat from bow to stern is the keel, likened to the spine in a human, from which extend the ribs (frame) that give the boat a rounded lower cross-section and provide strength against buckling. Wooden reinforcement is bonded in place during the layering process.
The flat cloth and mat material must be saturated sufficiently in resin so that it adheres to the curved surfaces. Yet excessive resin not only adds weight but also leads to longer curing times and poor work efficiency, and skill is required to determine the optimum amount of resin saturation by checking how much seeps out.
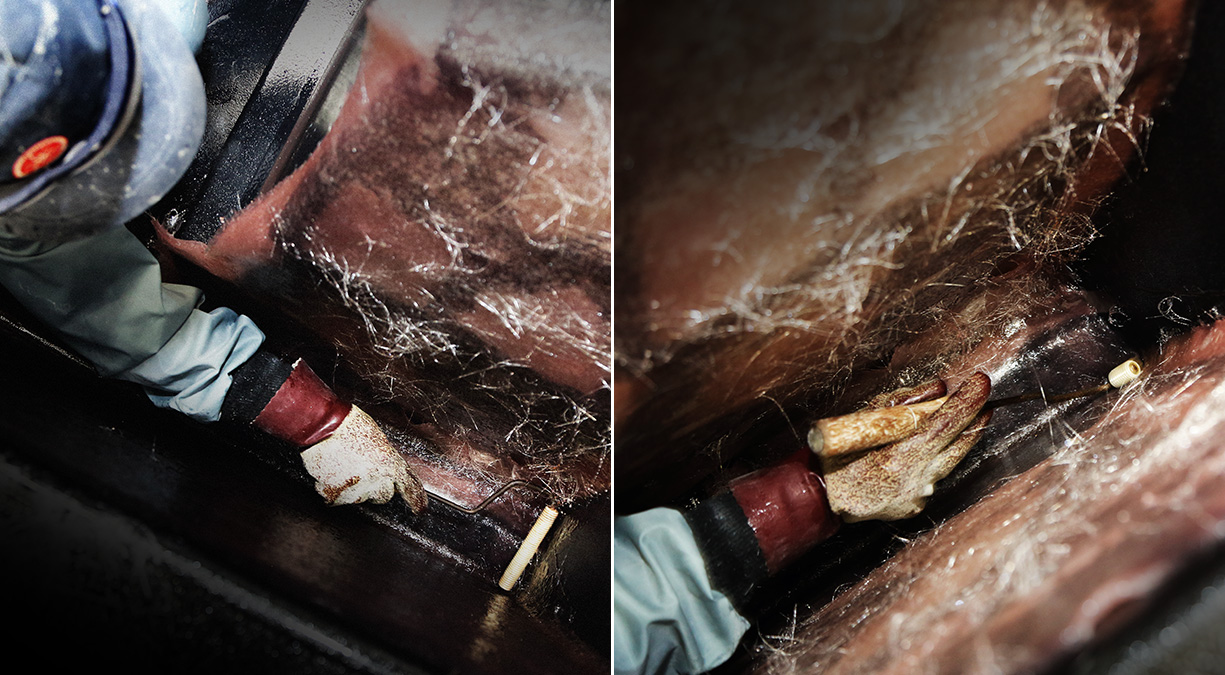
Rollers and spatulas are used to lay-up resin-saturated cloth and mat. It can be difficult to use rollers in molded areas with sharp angles, so specialists developed "spatulas" that help them reach every corner.
Bubbles in the resin can lead to cracking or peeling, so the cloth and mat needs to be pressed firmly to push out every last bubble—a process that is both meticulous and demanding.
The surfaces of joins between reinforcing materials such as the keel and frame have a specific cloth thickness and overlapping width. If these joins lack the required strength there is the risk of the boat breaking into pieces, so design drawings are checked thoroughly as there is simply no room for the slightest mistake.
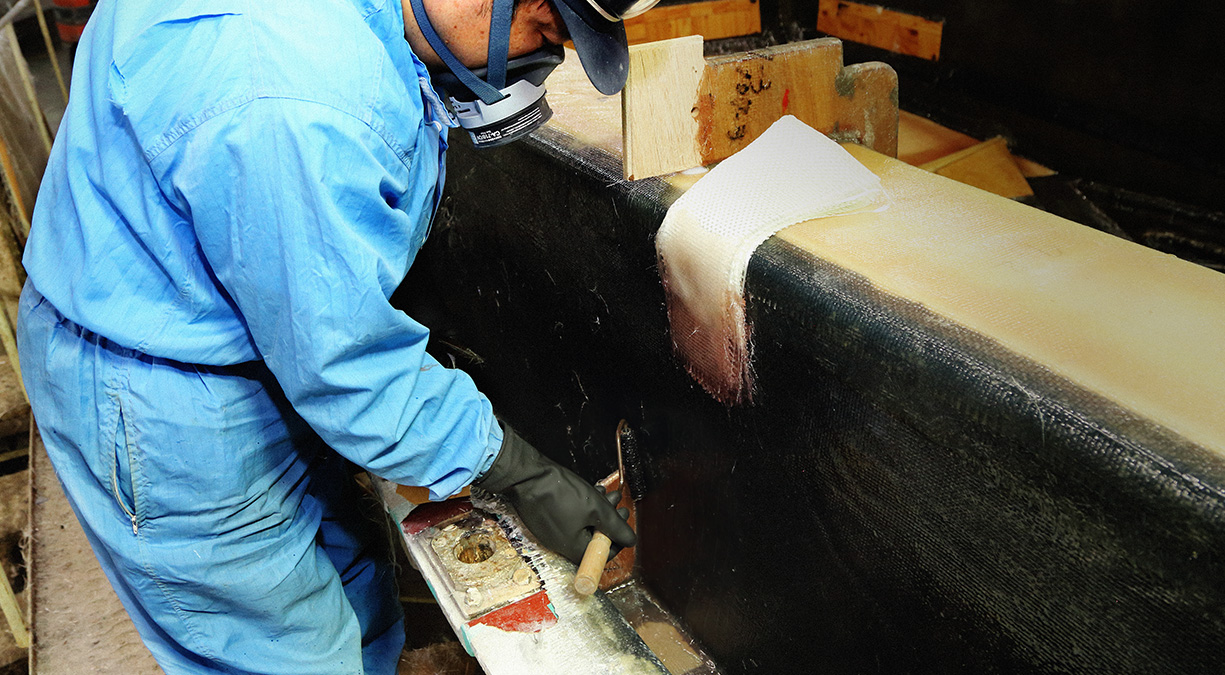
Methods such as "welding" and "riveting" are used to bond together steel reinforcing material, but boats have a wooden core as reinforcement for strength and lighter weight, in a method where surfaces are bonded together with FRP cloth.
The skills of the specialists and design expertise of Yamaha Motor come together to give customers the reassurance they need to use the boat with peace of mind, even through the tough rigors of the ocean.
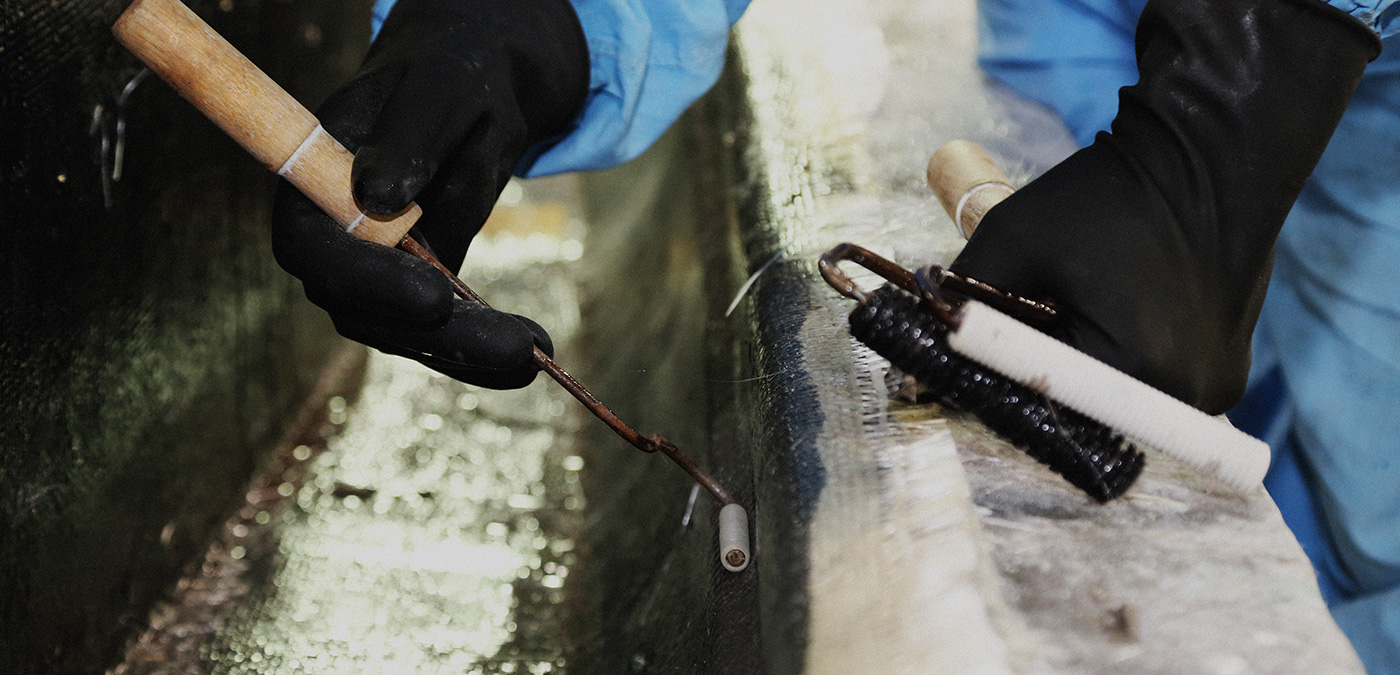