An Unmanned Industrial-use Helicopter Bringing Together Three Types of Technology
介绍雅马哈发动机技术背后的故事。
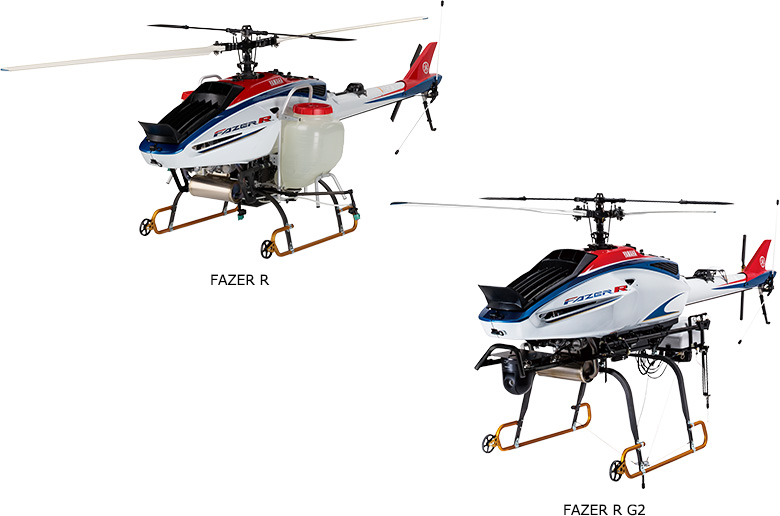
雅马哈的工业用无人直升机是一种无人机,主要用于农业领域的作物喷洒,但也被研究机构用于科学调查,辅助防灾和测量观测任务。
2016 年 10 月发布的新 FAZER R 是雅马哈的最新型号。它是根据农业产业的最新变化和基于日本政府“积极农业政策”的飞机制造业法*修订版开发的下一代机型。它以上一代FAZER为基础,但获得了更高的发动机功率输出、减少旋转损失的新尾旋翼形状等,使其能够承载一个32升的农化罐,大约是其1.5至2倍。之前型号的尺寸。这使得 FAZER R 每次飞行都能在更大的四公顷(40,000 平方米)土地上撒播农用化学品。
* 2014 年修订的飞机制造业法:最大起飞重量从 100 公斤增加到 150 公斤
Also, Yamaha announced the introduction of the FAZER R G2, a special model based on the FAZER R that is equipped for automatic flight to areas beyond the range of human sight. It is meant for handling tasks like taking measurements, conducting observations and gathering video footage in dangerous areas. Compared to the previous RMAX G1 automatic-flight model, carrying capacity has been increased from 10 kg to 35 kg and maximum operating altitude has gone from 1,000 m to 2,800 m, allowing observation of high-elevation volcanoes like Asama, Tokachi, Kusatsu-Shirane and Aso.
Woven into and supporting these two models’ reliability are Yamaha’s three core competencies: small-engine technology, FRP technology and electronic control technology. With its power unit for example, an unmanned helicopter requires the ability to carry heavy loads like agrichemical tanks, so it should have plenty of drive force and durability to provide consistently stable flight.
Generally, when a helicopter’s rotor tips spin faster than the speed of sound, the helicopter generates less lift and is prone to stall. So, typically, a fixed rotation speed is maintained while the rotor’s pitch is adjusted to increase or decrease lift. The rotor rotation speed for the FAZER and FAZER R at normal operation is set at 840 rpm. Its specially developed fuel-injected 390cc, liquid-cooled, 4-stroke 2-cylinder engine (#1) ensures stable performance, especially when operating over rice paddies during the hot and humid summer days in Japan when it is often used.
The engine’s horizontally opposed cylinder layout brings advantages like excellent weight balance, design compactness and mass-centralization. There is a growing number of agricultural areas in Japan located near residential neighborhoods and urban areas, so the crafts’ operating environment was also considered during development. The engine contains many years of Yamaha engine development know-how and a wealth of parts sure to spark interest in lovers of machines, like forged aluminum pistons, chrome-plated cylinders integrated into the crankcases, a crankshaft without a center journal, a plastic resin intake manifold and a titanium exhaust pipe.
The FRP rotors (#2) and body cowling are also among the crafts’ standout traits. These are not only lightweight and strong, but they also don’t break apart into numerous small pieces should they impact something, so the use of this material also helps to prevent secondary accidents. Also, helicopter rotors are normally made of metal, wood, carbon fiber and the like, but Yamaha uses two high-precision twin-blade rotors in which each blade weighs approximately 1,700 grams, but the difference in weight between the two blades is under just 5 grams. The shape and size of the rotor naturally affects the machine’s center of gravity but also its overall balance, torsional characteristics and more, so this high level of manufacturing precision to create a uniform profile is due to making full use of the FRP expertise we gained through our years of building boat hulls.
However, what is most important though is to make the remote-controlled unmanned helicopter easy to operate for as many people as possible. To that end, Yamaha has spent an enormous amount of time and effort developing and refining its electronic control technology.
In 1990, the high-precision Yamaha Operator Support System (YOSS) employing a laser sensor to control altitude was added to the R-50 model. Following that, the revolutionary Yamaha Attitude Control System (YACS) was developed using feedback from three gyro sensors and an accelerometer. YACS was added to the R-50 in 1995, making the helicopter easier to operate, and its precision was further refined for the RMAX released in 1997. Furthermore, the RMAX Type II G released in 2003 added a GPS to the system and greatly improved the helicopter’s usability. The FAZER and FAZER R combine the GPS antenna and directional sensor into one unit, employ a phase lock loop (PLL) device to control radio wavelengths for improved reception stability, feature numerous improvements to their electronic control systems, have an airspeed control mode and more. These functions enabled easy, smooth takeoffs and landings and the capability for maintaining airspeed automatically.
Also, a model capable of automatic flight was released in 2000 aimed at capturing images and conducting observation of volcanos beyond the range of human sight, the RMAX G0. Its high-precision Real-Time Kinematic Differential GPS (RTK-DGPS) system enabled automatic flight along pre-programmed flight paths. Additionally, with the RMAX G1 released in 2006, further improvements to the flight control system made it possible for more precise flight even in difficult conditions such as high winds, expanding the advantages automatic flight could bring. In these ways, Yamaha’s unmanned helicopters are spreading into uses outside the agriculture sector, such as use in observation and surveys of volcanic eruptions and other disaster areas.