ヤマハ発動機の第1号製品、125㏄のモーターサイクル「YA-1」(1955年)。そのフロントフェンダーには、音叉をモチーフとした真鍮製のオーナメントが輝いていた。この復刻モデルを限定生産するにあたり、その大役を担ったのは鋳造試作職場のクラフトマンたちだった。
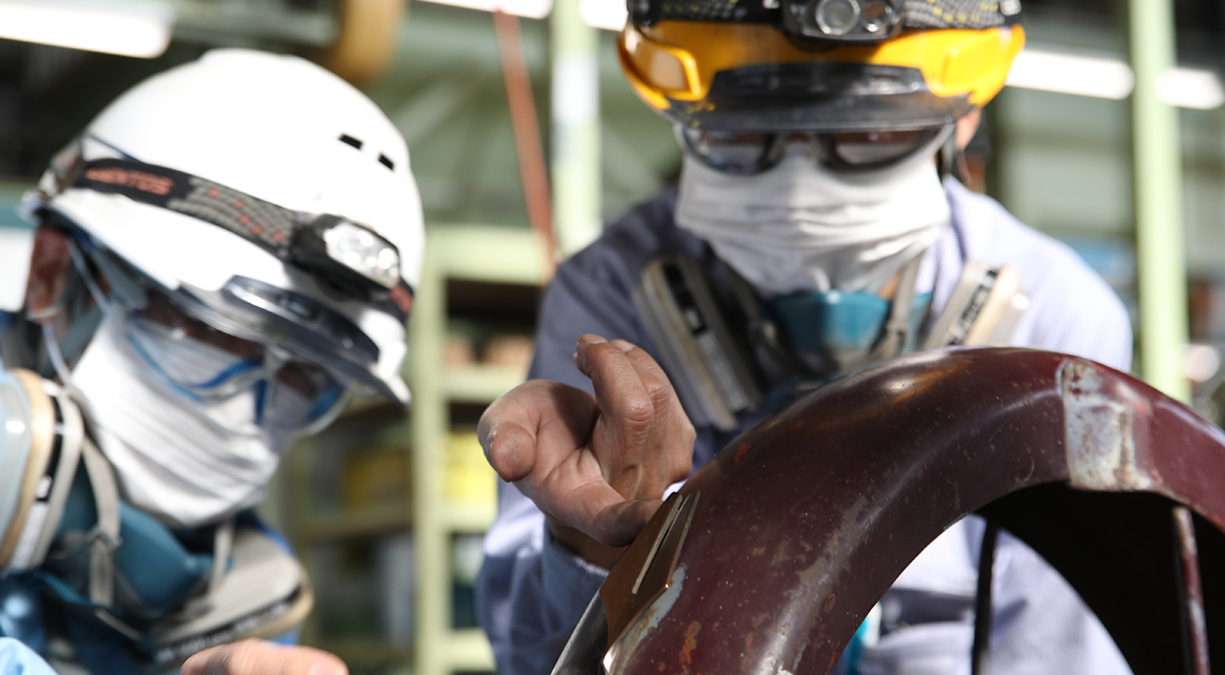
そもそも
溶かすことが
難しい。
ずっしりとした重み。そして、黄銅色の光沢。銅と亜鉛の合金である真鍮(brass)には、他の金属にはない独特の風合いがある。経年による表情の変化と、それを磨く愉しみ、また磨くことで輝く鏡面の美しさも魅力の一つだろう。
その反面、真鍮の鋳物づくりは他の金属とは比較にならないほど手間がかかる。人類はこの素材と350年以上も向き合ってきたが、その間、製造技術のイノベーションはほとんど起こらず、場数を踏んだクラフトマンたちの知見と手業によって製法がつながれてきた。
扱いにくい理由の一つに、融点の高さという特性が挙げられる。アルミが600度超で溶けるのに対して、真鍮の融点は1000度を超える。「かたちをつくる以前に、そもそも溶かすことが難しい」。真鍮の用途は限定的であり、技術や設備の発展も見込みにくい。ヤマハ発動機が真鍮鋳物を内製した実績は1950年代まで遡らなければならない。
1955年に製造されたYA-1のオーナメントを復刻するにあたり、試作部門に白羽の矢が立った。試作職場は、ものづくりにおいて二つの枢要な機能を担っている。一つは研究開発部品の試作であり、もう一つは量産開発のための試作である。その機能を果たすために、あらゆる素材や加工技術、工作設備、そして組織としての豊富な知見と経験、さらにはものづくりへの喜びを身体いっぱいに湛えたクラフトマンたちが在籍する。
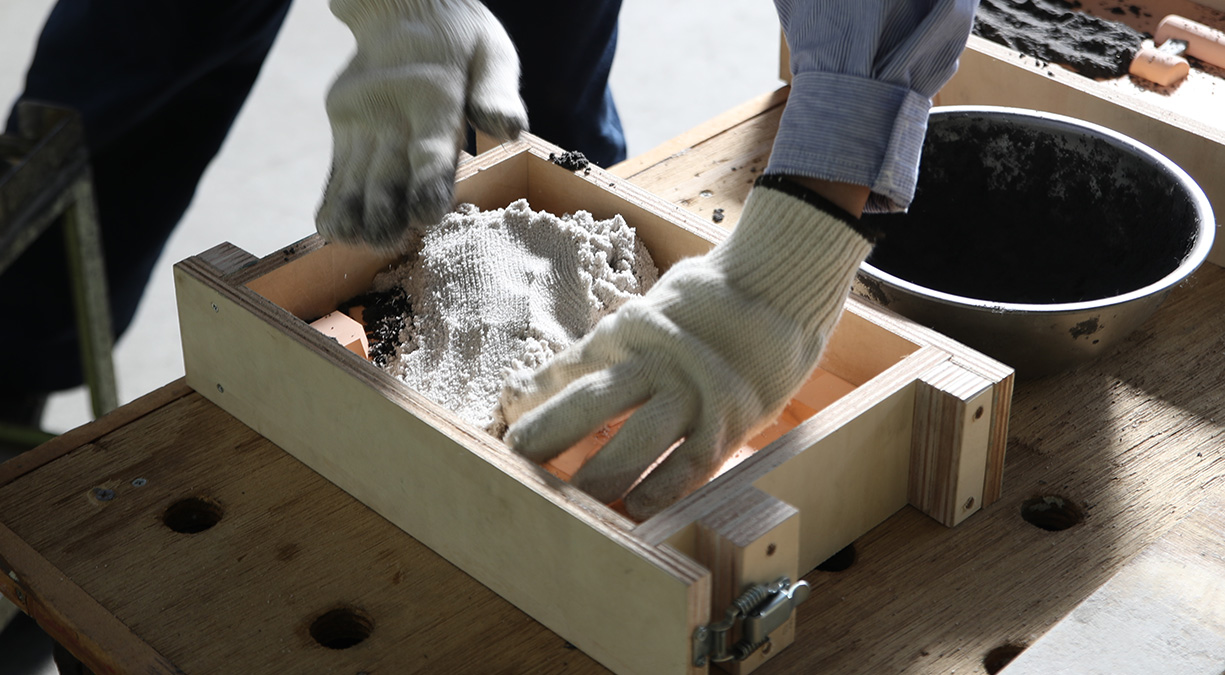
先人たちと
同じ製法で
つくりたい。
色がくすんだオリジナルのオーナメントを手に取って、じっくりと観察をする。これをかたちにするだけなら、知恵を働かせればなんとかなるかもしれない。ただ、試作職人たちは、もう一段上を狙った。「68年前と同じ方法でつくりたい。そして、試行錯誤の過程から先人たちの苦労や思いを感じとりたい」と。
まずは素材を特定しなければならない。ひと口に真鍮と言っても、銅と亜鉛の含有率で色合いも違えば、伸びや強さなどの性格も異なる。オリジナルを観察し、さらには製造工程を想定した上で、高力黄銅鋳物1種HBsC1ではないかというあたりをつけた。後に設計図に残されメモが発見され、その目利きが正解だったことが明らかになる。手書きのHBsC1という文字を見た担当者は、「よっし!」と声をあげて喜んだ。
次に製法である。3年間で約11,000台という出荷実績から平均的な日産数を勘定し、砂型手込め鋳造が用いられたはずだと推察した。砂は比熱が小さく保温性もあるため、流し込まれた溶湯がゆるやかに冷却される特性を持つ。最も古典的な鋳造方法ではあるが、現在も小ロッド鋳造の主力となっている製法だ。知見はある。
最後に残った課題は方案だった。方案とは、溶湯の通り道や鋳込温度など、鋳造工程のすべてを規定する設計図のことを指す。どこから溶湯を注ぎ、どのように湯を流して型の隅々まで行き渡らせるのか。いくつもの失敗を重ね、「おそらくこれが正解だろう」という答えにたどり着いた。もちろん製法の記録が発見されない限り確信には至らないが、これなら先人たちからも咎めは受けないだろうというところまで考え抜き、また試鋳を何度も繰り返すことで再現方法を確立した。
その作業工程は、確かに68年の時計を巻き戻したかのように見える。
まず、上下に分かれた木枠に鋳型を置く。この鋳型は、金属が凝固する際に起こる縮みを推量して、わずかに製品より大きくつくられている。そこに3種類の砂を順に込める。砂にかける圧を手のひらで繊細にコントロールし、部位によってふわりと、部位によってはぎゅうぎゅうと。砂を使い分けるのは、製品の面粗度をよりオリジナルに近づけるためだ。
「見切り」と呼ばれる手業で表面を均し、硬化・乾燥させた後に上下の型を接合する。かちかちに固まっているとは言え、相手は砂である。粗末に扱えば砂が崩れて湯道にこぼれ、鋳物の表面を荒らす原因となる。がっちりと接合されたその型の一部をカットすると、方案検討で苦労を重ねた小さな注湯口が現れた。
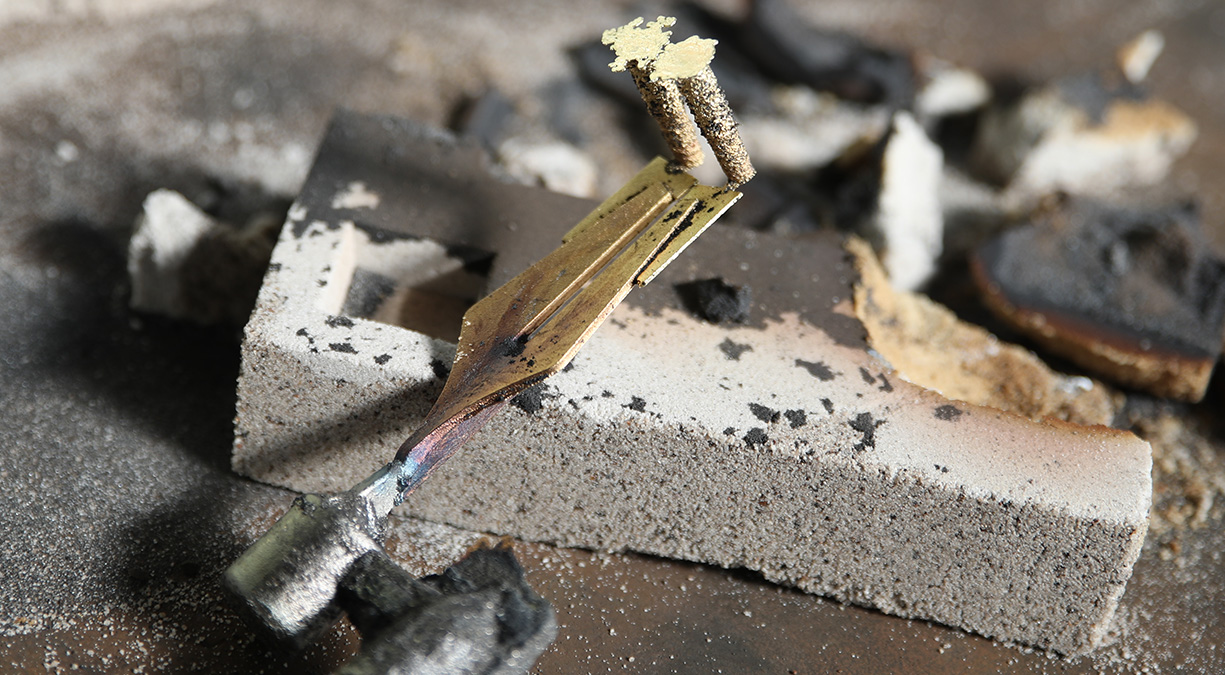
頭で描く
温度、速度、
そして量。
その頃、トリベ(耐火材容器)の中では真鍮の溶湯が真っ赤に煮えたぎり、まさに1000度の壁を超えようとしている。火鉢ほどのトリベの中には、柄杓の役割も担う小さなトリベが入っている。料理で言えば、オーブン・イン・オーブンといったところだろう。作業者は前工程の進捗に注意を払いながら、絶妙のタイミングで狙った温度に到達させた。
ここからは瞬きもできない。トリベの中の小さなトリベをヤットコのような治具を使って挟み、一気に注湯口に注ぎ込む。そのわずか1秒、2秒の間にも、湯道を正しいスピードで駆け巡る溶湯の姿がクラフトマンの頭の中には浮かんでいる。温度、速度、量。そのいずれか一つが欠けても湯回りに不良を起こす。繰り返してきた試鋳で、その技を磨いてきた。
冷却後、砂型を割って、かたちを得たばかりのワークを取り出す。そのワークから方案部を切断すると、誇り高い音叉のオーナメントが姿を現した。仕上げの工程はさらに繊細だ。#180から#2000まで7種のサンドペーパーを順に当て、バフを使ってフィニッシュする。1個のオーナメントを磨き上げるのに約1時間。かつてオリジナルを研磨した先人たちもきっと同じだけの時間を費やしたことだろう。
「素材や製法、仕上げまでオリジナルを忠実に再現しようと、知恵を出し合って、トライ&エラーを繰り返してきた。先人たちも同じ過程を経験しながら、この真鍮製オーナメントをかたちにしたのだと思う」
「68年前と同じ方法でつくりたい」――。それを探求する過程で手に入れたのは、先人たちへの敬意、そしてものづくりに没入することへの純粋な悦びだった。
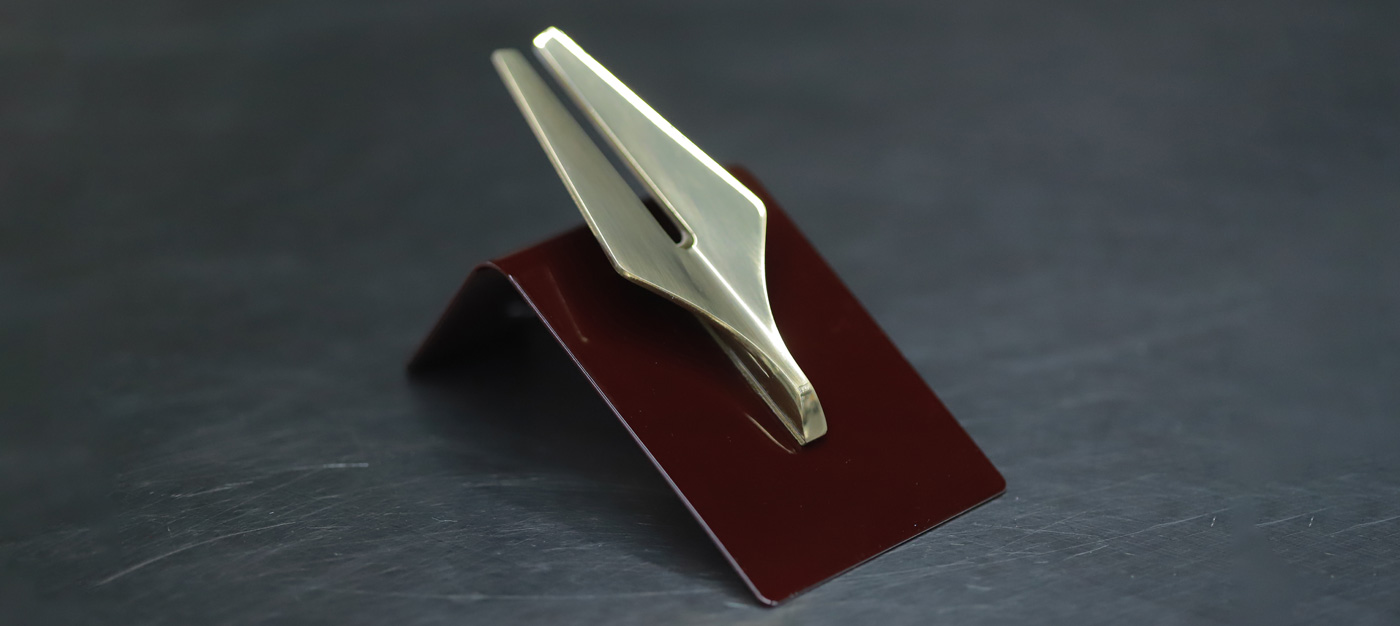