構造や形状に物理学の知見が織り込まれた、ブルーボトルコーヒーのドリッパー。適切なスピードで一定の流れを生み出す40本のリブや抽出口の1穴構造など、「美味しさ」を追求したこだわりのかたちには有田焼・銘窯の技が生きている。磁器という美しくデリケートなマテリアルで100分の1ミリの精度を担保する匠の技能を、試作工場発・ヤマハの手が支えている。
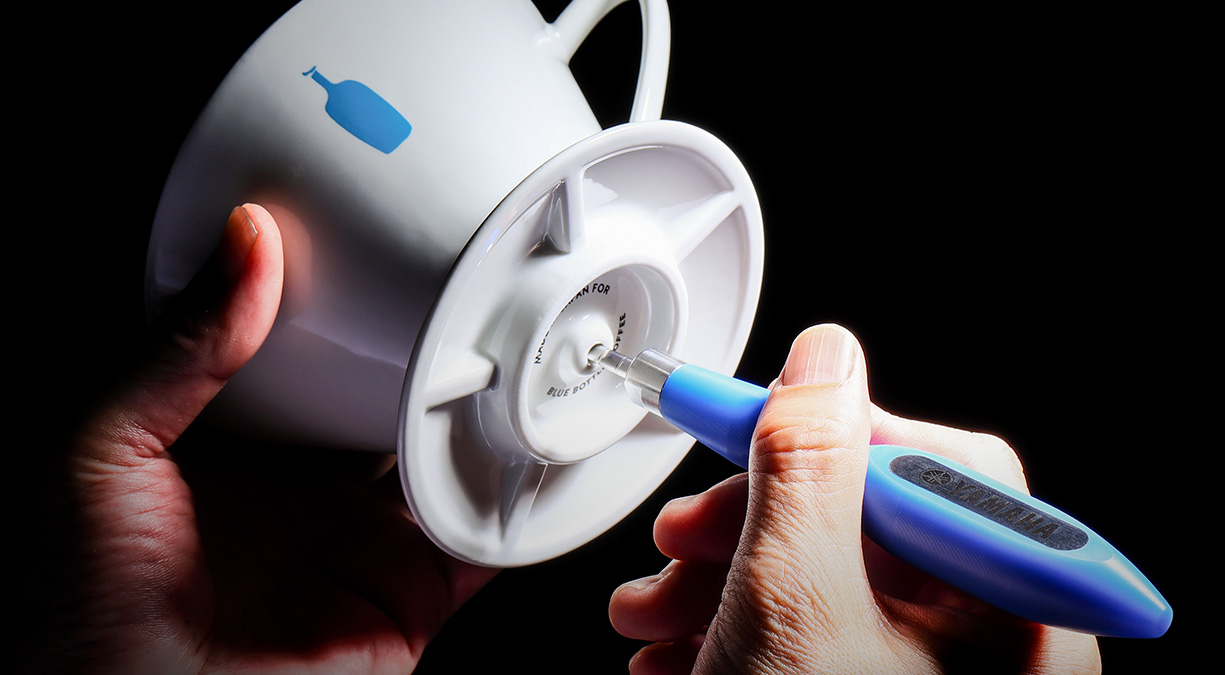
試作工場に、
領域や
難易度の
際限は、ない。
試作の現場では、伝統的に「アルファ価値」という独自の言葉が交わされてきた。
「それまで世になかったものをつくり出す。できなかったことをできるようにする。そして、できたものをより良くするために頭をひねり、さらなるひと手間を加えていく。そこに試作というこの仕事ならではの喜びがある。我われが使ってきた『アルファ価値』という言葉は、つまり、ヤマハの手と同義のもの」
試作工場は、製造業の中で二つの枢要な務めを担っている。一つは研究開発部品の試作であり、もう一つは量産開発のための試作である。いずれにしても製品開発者にとって0から1を生み出してくれるかけがえのない存在であり、そこでかたちを与えられた試作部品は、やがて図面を耕す基準となり製品価値の向上に重要な役割を果たしていく。
ここに持ち込まれてくる依頼や相談に、領域や難易度の際限はない。特殊なネジ1本からMotoGPマシンに組み込まれる大型の先行開発部品まで、さまざまなものづくりの依頼が飛び込んでくる。中には駆け込み寺同然の無茶な要求がないこともないが、それでも「できない」と門前払いすることはない。できる条件と状態を整えることに、試作職人としての意地もある。そうした依頼や相談をかたちにしていくために、あらゆる素材や加工技術、工作設備、そして組織としての豊富な知見と経験、さらにはものづくりへの喜びを身体いっぱいに湛えた熟練のクラフトマンたちがいる。
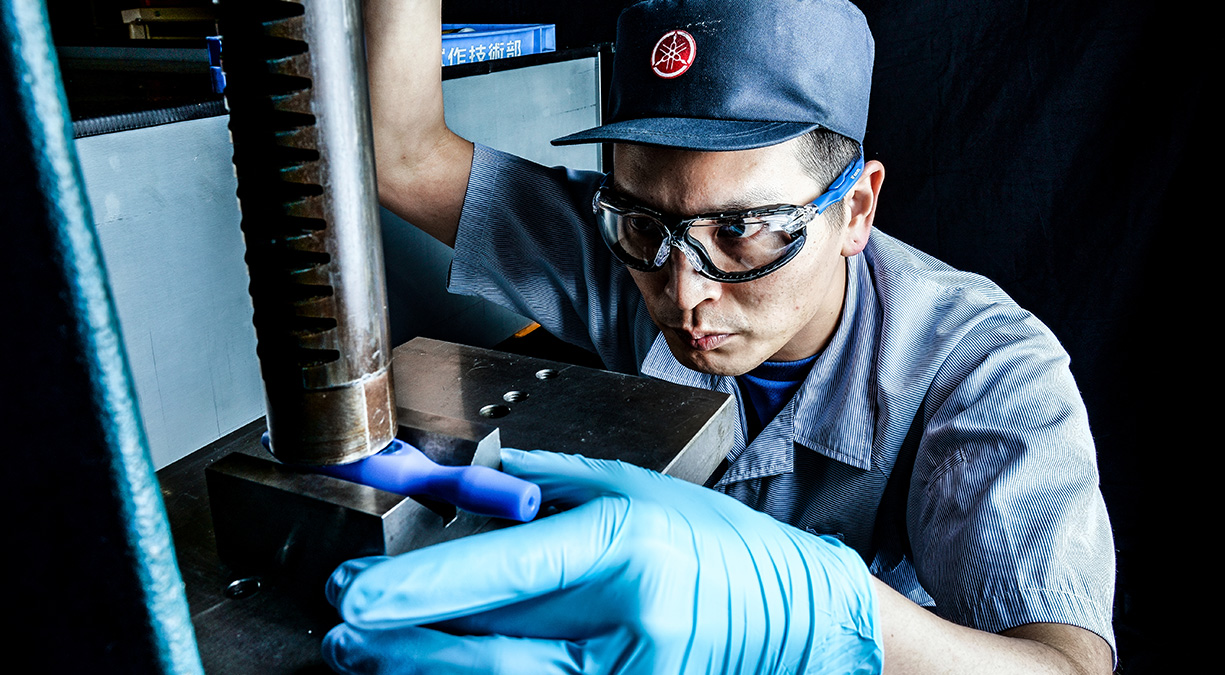
本質を
知る者同士の
敬意と共感。
「おもしろい」――。突如舞い込んできたドリッパー検査治具の相談に、試作技術のメンバーは無邪気に反応した。
「お客さまに提供する一杯」への、ブルーボトルコーヒーの一途さ。そこに感銘を受けたことは間違いない。同時に有田焼窯元の精緻なものづくりにも思いを馳せた。ドリッパーから糸のように落ちる美しい褐色の液体に、ものづくりの本質を知る者たちは敬意を抱いたのである。「焼成による縮み、釉薬による厚み。それらを計算した上で100分の1ミリの精度でつくるこだわりに、我われが積み上げてきた技術で貢献したい」。幅広い専門性を持った人材が、いつの間にか集まっていた。
アイデアを出し合い、検討を重ね、いくつもの試作品をつくった。それらを有田に送っては、オンラインで窯元の皆さんの率直な意見を伺う日々が始まった。400年続く工芸の匠が毎日使う道具である。ブランドのこだわりを守り抜く高精度を担保すると同時に、ストレスなく仕事に没頭できる使いやすさを備えていなくてはならない。許されるならば窯元を訪ねて匠の手の動きを目で追い、意見交換を重ねたいという思いはあったが、感染をひろげ続ける新型コロナがそれを許さなかった。
●
世界各地の店舗で提供されるブルーボトルコーヒーは、すべて有田焼の銘窯「久右エ門」の手によるドリッパーで抽出されたものだ。ドリッパーの磁器の厚みは、湯の熱を奪う。ブルーボトルコーヒーの品質を約束する最薄部約3mmの造形を実現するためには、強度に優れる陶石と、世界にも名を馳せる有田の伝統技が必要だった。求めるドリッパーをかたちにするため久右エ門の扉を叩いたアメリカ人技術者は、やがて有田の町に腰を据え、匠とともに20を超えるサンプルをつくったという。
「一杯のコーヒーのために、ここまでこだわるのかと感心した」。匠はそう振り返る。「それはヤマハの技術者に対しても同じこと。使う者のためにとことんまで考え抜くその姿勢、そして、それをかたちにしてみせる技術力。ものづくりに向き合う者として、強く感銘を受けた」
形状、素材、重量バランス、そして機能。手のひらに収まるその小さな検査治具には、至極の精度を保証する技術だけでなく、試作工場ならではのアイデアとこだわり、そして工芸の匠に対する敬意が詰まっている。
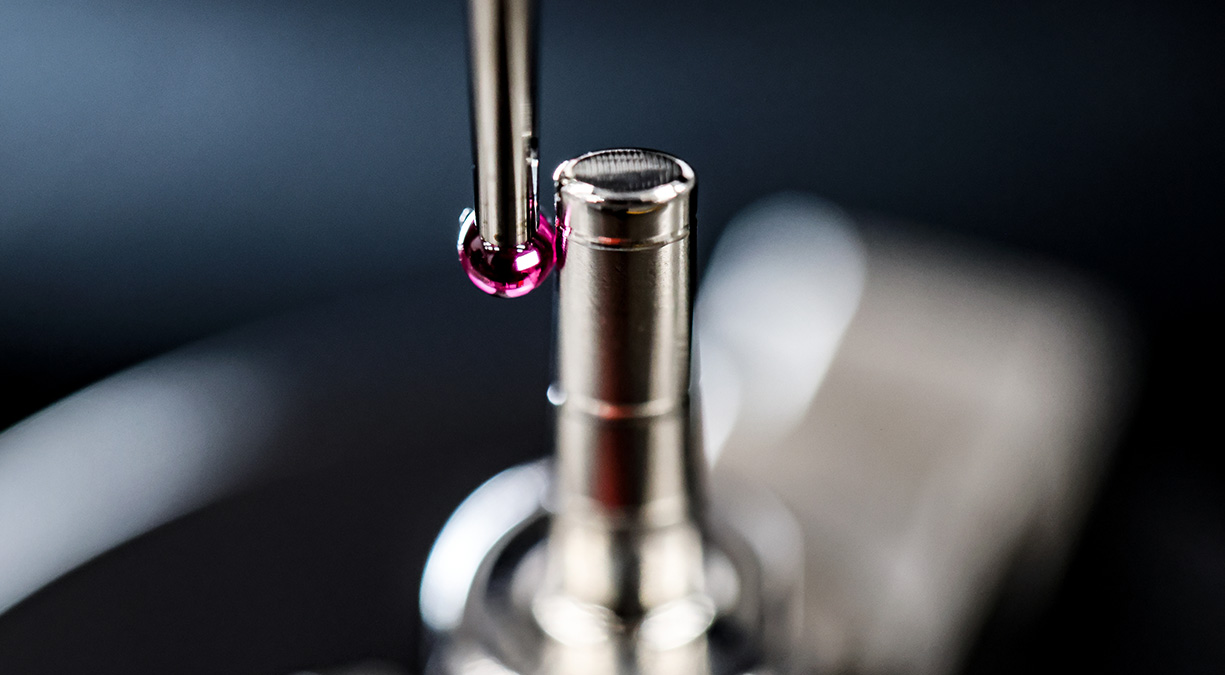
品質を
証明する、
匠の印鑑。
寸分の狂いもない穴のサイズを保証するのは、治具の先端部にあたるステンレス製のゲージだ。材料から吟味を重ね、高硬度かつ錆にも強い析出硬化系ステンレスを選択した。その形状には、手に取って見ただけでは気づくことのできない幾つもの知恵と加工技術が潜んでいる。
楕円テーパーの設計もその一つだ。ゲージはそもそも真円の抽出口に通すものだが、差し込みの作業は楕円のほうが遥かにスムーズでストレスは少ない。その楕円型のゲージには先端から軸に向かってテーパーがついている。あまりにも微細なそのテーパーラインを肉眼で捉えるのは至難の業だ。さらに、ゲージには公差を示す2本のラインが加えられた。一つ目のラインを通過しないもの、二つ目のラインを通過してしまうものが出荷されることはない。デリケートな性質を持つ磁器だからこそ、熟練の技をもってしてもごくわずかな不良が出てしまう。その厳格な検査と管理は、ブルーボトルコーヒーが提供するフレーバーを守る「最後の砦」となる。結果、極めて困難な加工技術を要する図面が描かれた。
3軸制御の高性能マシニングセンタが、その複雑微細なゲージを正確に削り出していく。1本に要する時間はおよそ60分。長い時間をかけてやっとかたちを得た小指サイズのゲージは、次に検査室に持ち込まれて三次元測定機にかけられる。スタイラスと呼ばれる接触部分の赤いルビーがそのラインをやさしくなぞると、モニターには3Dのデータが浮かび上がった。ミクロンの単位のギャップも決して見逃されることはない。
「ブルーボトルコーヒーのこだわりと、有田焼の伝統の技。そこに誇りを持った人々の質の高い連鎖によって、美味しい一杯のコーヒーが提供される。我われがつくった治具は、その価値を証明する匠の印鑑のようなもの。やりがいのある仕事に、積み上げてきた試作技術で貢献できたことが何よりうれしい」
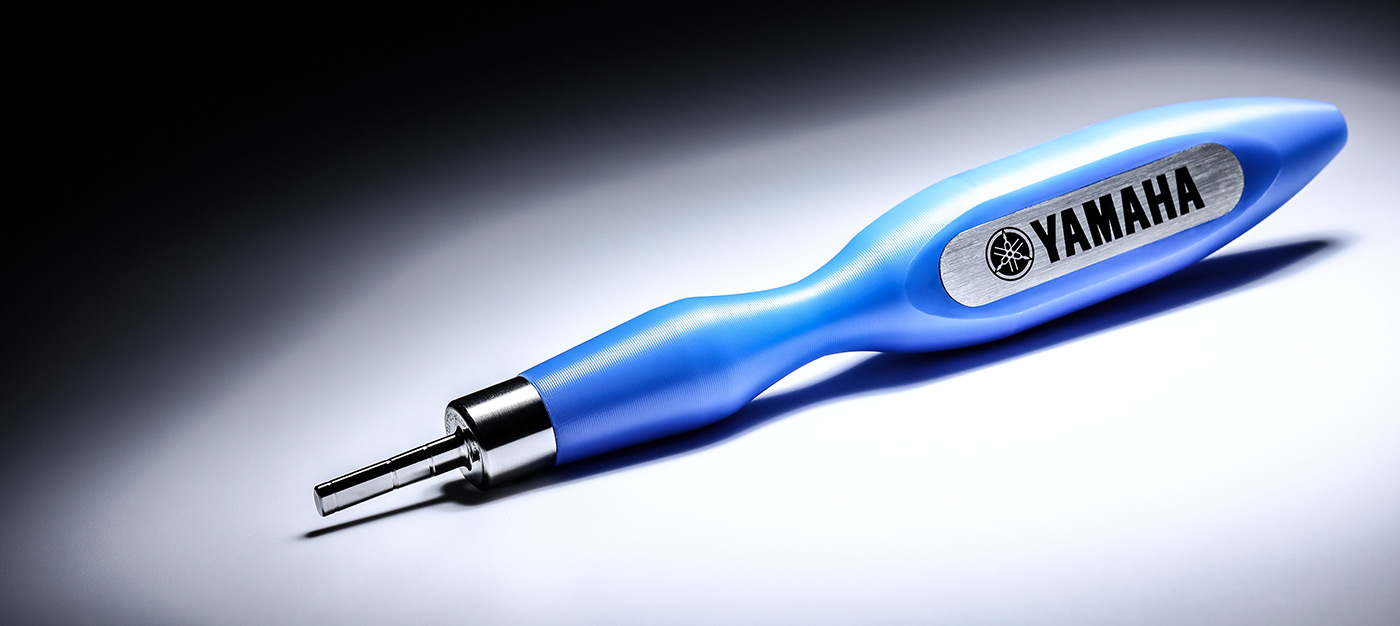
ブルーボトルコーヒー
【ドリッパー検査治具】
有田焼の銘窯、久保田稔製陶所 ―久右エ門― の手によるブルーボトルコーヒーのドリッパー。その生命線とも言える抽出口の検査に用いる専用治具を、Blue Bottle Coffee Japanの依頼によりヤマハ発動機 試作技術部門が企画・設計・製造を担った。
部位によって旋削幅を変える細やかな配慮
長く使うことで仮にゲージ部が摩耗しても、手になじんだグリップ部はそのまま使えるよう、セパレート構造の設計とした。グリップは軽量化と重量バランスの最適化を目指してMCナイロン樹脂を採用し、部位によって旋削の幅を変える細やかさで滑りにくさも追及している。握りの太さは、持ちやすく負荷の少ない直径12ミリに設定。握りのアングルや重量バランス等を複数の試作モデルで検討し、試用した匠のフィードバックを反映させながら最終仕様を決定した。
MotoGPマシンの部品づくりにも活躍する切削機
検査治具の命であるゲージ部は、3軸制御の高性能マシニングセンタで削り出す。素材となる析出硬化系ステンレスSUS630は小指にも満たない大きさだが、複雑かつ高精度な切削が完了するまでにはおよそ60分もの時間を要する。勢いよく吹きだす白濁色の切削油材の中でゆっくりとかたちを変えていくその姿は、まるで孵化を迎えた小さな生命のようにも感じる。このマシニングセンタは、先行開発部品の加工や、MotoGPマシン「YZR-M1」の専用部品の製造等でも活躍する。
三次元測定器と摩耗確認治具で高精度を保証
削り出されたゲージ部は、3D測定によって品質を保証される。その保証は出荷後、有田焼の匠の手に渡ってからも続く。ゲージの先端部分に溝加工を施し、目視による摩耗確認ができる工夫を加えたほか、セルフチェックを可能にする専用の摩耗確認治具を有田にお届けした。耐久テストでは25,000回もの模擬検査を実施し、その結果、摩耗確認治具によってわずかな摩耗が確認された。
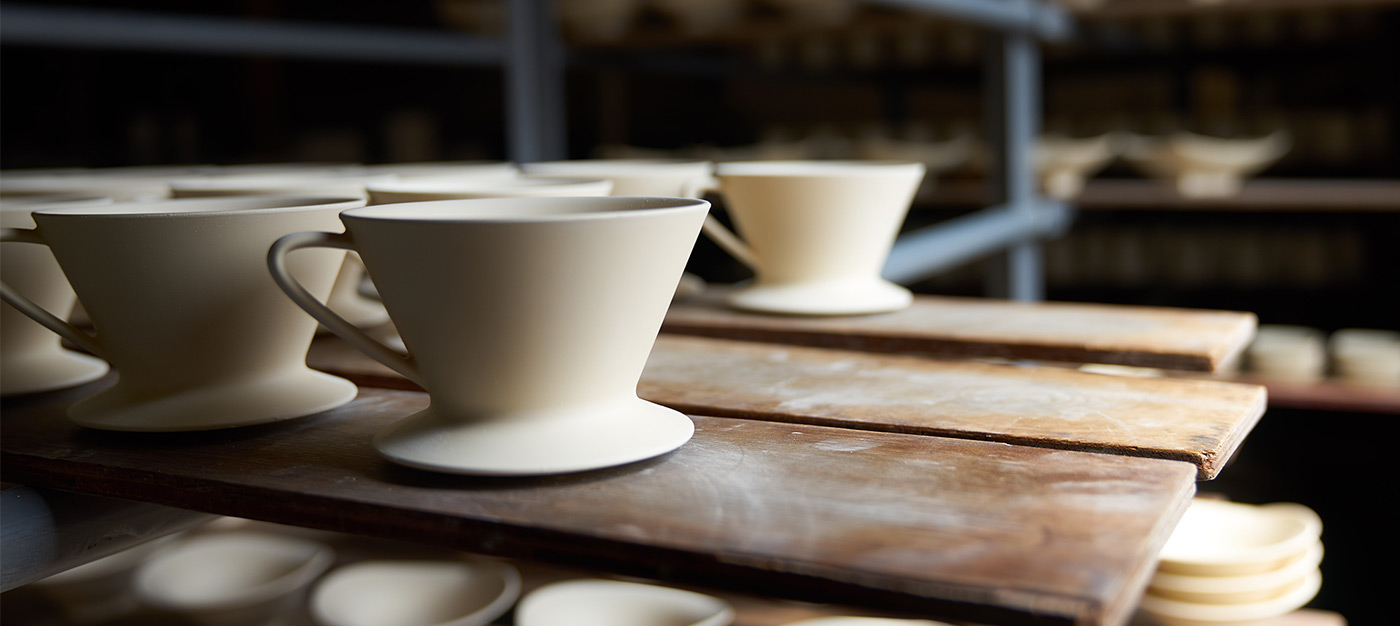