工場でプールを手づくりする、デリケートなダイナミズム
FRP(Fiber Reinforced Plastics)とは、繊維強化プラスチックのこと。ヤマハ発動機はボート製造で培ったFRP製造技術を活かしてプールの製造をスタートし、間もなく半世紀を迎えようとしている。大きな部品を高精度で美しく仕上げるその工程は、いまもクラフトマンたちの匠の技能によって支えられている。
タッチの差、
その精度を
担保する。
「指先、タッチの差」――。競泳実況の常套句であるこのフレーズは、決して誇張した表現ではない。その瞬間、スイマーの指が伸びていたか、それとも曲がっていたかというわずかな差で記録も勝敗も違ったものとなる。そのシビアな真剣勝負のステージとなるプールは、もちろんどこまでもフェアで、どこまでも精緻でなくてはならない。公認プールの規格は極めて厳格だ。
50メートル・8レーンの競技用プールを満たすためには、およそ200万リットルもの水が必要だ。25メートルの標準的なスクールプールでも、36万リットル前後の強烈な圧力を受け止めている。水圧による負荷だけではない。四六時中、直射日光を受け続けるスイミングプールは、気温の変化による素材の膨張・収縮まで設計に織り込まれていなければならない。こうした厳しい要件、過酷な条件を満たしながら、ヤマハFRPプールは「指先、タッチの差」となるミリ単位の精度を担保している。
安全性や耐久性は、さらに重要な要件である。
2011年に発生した東日本大震災の直後、ヤマハは大規模な調査団を組んでプールの納入先を巡回し、岩手、宮城、福島の3県に納めたヤマハFRPプールのうち、立ち入り禁止区域を除く全329件で被害の調査・点検を実施した。この調査で、地盤沈下等による配管の損傷などが見つかったものの、すべてのプールで本体機能には大きな被害がないことを確認した。粘り強い素材特性を持つFRPプールの高い耐震性能があらためて証明され、そのうち避難所となっていた64の施設では、断水中の水道水の代わりにプールの水が生活水として活用されていた。
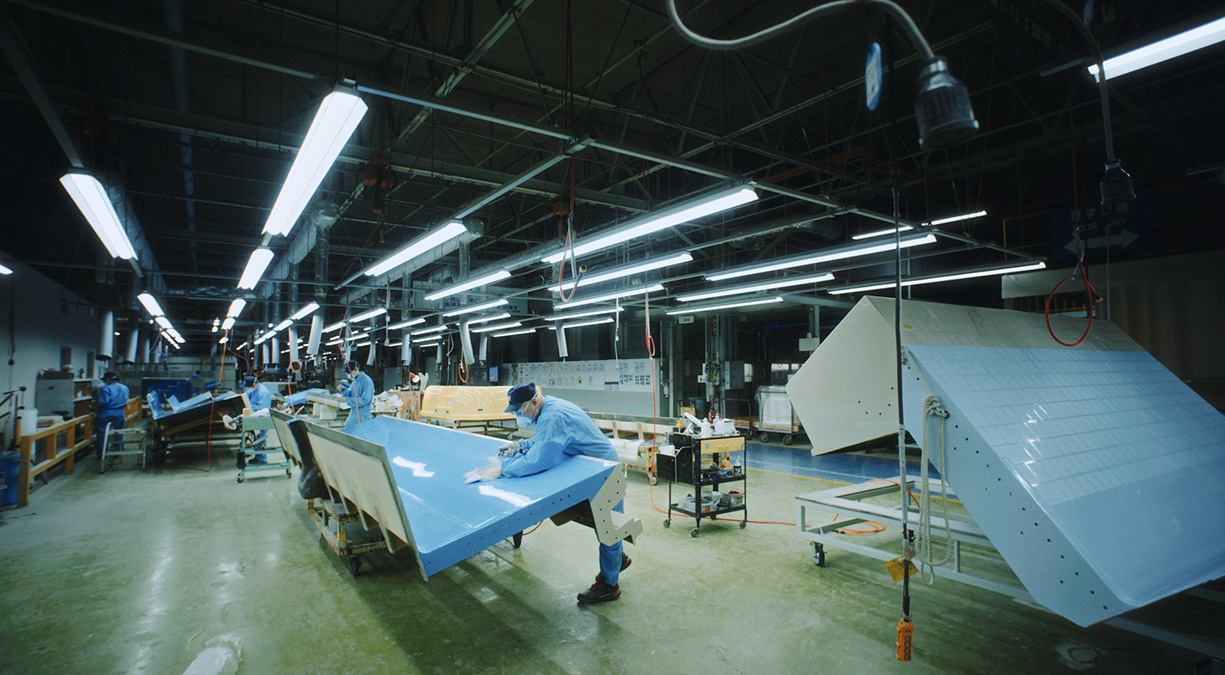
仕上げから
始まる
ものづくり。
ヤマハFRPプールは、管理の行き届いた自社工場でユニット部品を成形し、それらを施工現場に移送して組み立てることで完成する。「工場でプールを手づくりする」という不思議な光景を正確に思い浮かべるのは難しいが、その違和感のとおり、浜名湖畔に建つFRPプールの成型工場の内側はオートバイや船外機の製造・生産現場とはずいぶん違う。
工場に足を踏み入れて、まず目を奪われるのは整然と並ぶ製品の大きさだ。ワークと呼ばれる構成部品の一点一点の存在感が、工場の景色を独特なものにしている。大きなものでは長さ8m。たとえば組み立て前のプラモデルの部品を思い浮かべてみてほしい。そのうち、手に取ったたった一点の部品がこのサイズなのである。オートバイの製造工場とは景色が違ってくるのも当然である。
さらにもう一点。この工場の中で行われているほぼすべての工程が、クラフトマンの手作業によるものだ。よって、工場につきものの大きな機械音が響き渡ることがない。広く、大きなものが並ぶ、静かな空間。ここでプールが産声を上げる。
ヤマハFRPプールは、雌型にセットしたガラス繊維に樹脂を浸透させ、これを幾重にも重ねることで成形される。型に触れていた面がプールの表面となるため、クラフトマンは美しさを求めて極限まで型の平滑化と向き合うこととなる。たとえ目視できなくとも、この工程でわずかでも凹凸を残してしまえば、もう後戻りはできない。だからこそ、その目は厳しい。一般的な製品なら塗装と言えば仕上げの工程だが、FRPの場合は、その繊細な仕上げの作業からものづくりがスタートする。美しさを作り込み、その後に強さが積み重ねられてゆく。
滑らかで、美しい型。それはゲルコート塗料を吹く職人にとってはキャンバスだ。工場の一角に据えられた塗装ブースには、ゲルコート塗料を吹きだすエアスプレーガンがぶら下がっている。
「一発勝負」
右手にエアガン、左手にエアホースを持ったクラフトマンは、その緊張感をこう表現する。
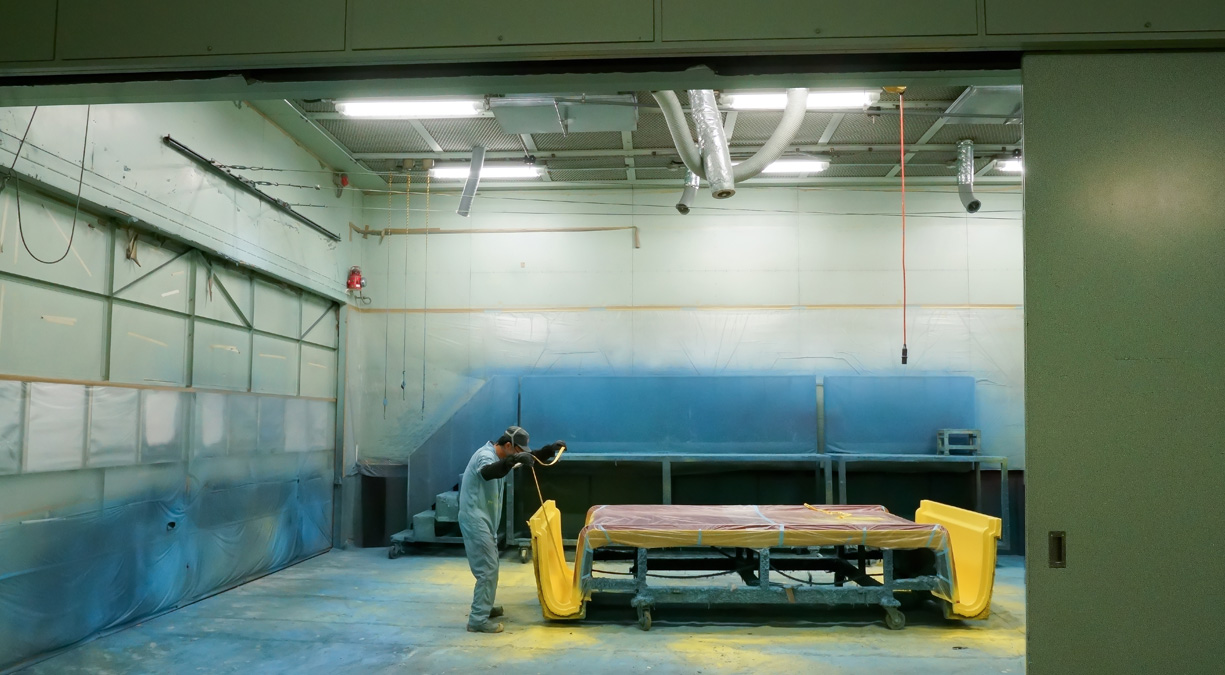
淀みなく、
そして
しなやかに。
ゲルコートの吹付を行うクラフトマンのしなやかな動き。その美しさを端的に伝える言葉が見つからない。ガンを持つ右手、ホースをさばく左手、首の角度や身体の向き、そして細やかな移動。それらすべてが連動し合い、淀みなく、しなやかに、そして静かに続く。両手に握ったツールが見えなければ、まるで舞っているようにも映ることだろう。それでいて機敏で、変幻自在にアングルや強弱の変化までつく。
吹付1回あたり塗膜の厚さは0.2mm。これを2回と少しの繰り返しで規定の0.55mmにもっていく。ガンから吐出するゲルコートの量は厳格に管理されており、余分な厚塗りはまったくできない。
圧巻は手首の返しだ。吹付はスプレーガンを往復させながら行うが、その折り返し点は物理的にどうしても二重になる。横移動と同じリズムで折り返せば液だれやムラになるため、クラフトマンは繊細かつ高難度の技をここで繰り出す。スナップを利かせて滑らかに手首を返し、同時にスプレーガンを対象物からスーッと離していく。その速度は速くても遅くてもいけない。しかも、均一でなくてはならない。
返ってくるときはその逆の動きとなる。往復によって塗料が厚くなることを見越して、吹付量が少なくなるよう距離でそれを微調整する。製品の角ばった部分も塗料がたまりやすいが、これも同じ技を用いてケアされる。「カラダがそれを覚えている」。吹付の匠はそう話す。
厳しく室温管理された塗装ブースとは言え、冬の朝など塗料の出方が鈍いと感じることがある。職人の感性でそうした些細な変化を見つけると、エア圧を変え、動きのスピードを変え、ベストな状態にアジャストする。
ヤマハFRPプールの成形技術。そのルーツはボートの艇体づくりに端を発する。軽く、強く、そして設計自由度の高いFRPの特長を活かして、いまから半世紀ほど前にプールの製造を開始した。ミリ単位の精度や強度・耐久性だけではない。美しく肌触りの良い、笑顔溢れるプール。ボートを起源とするその歴史を遡れば、FRPプール製造現場のこだわりが見えてくる。
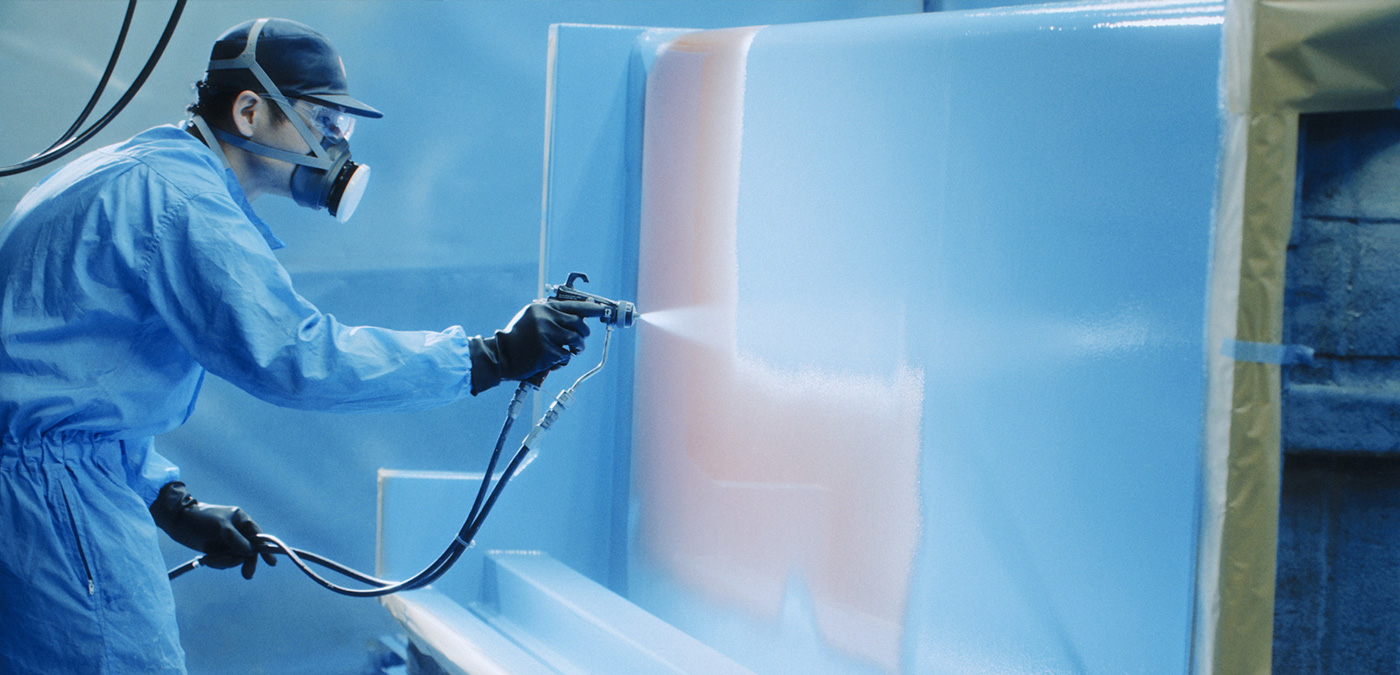