アルミ鋳造技術とアプリケーション
ヤマハ発動機の技術ストーリーをご紹介します。
アルミニウムは軽くて磁気を帯びず、熱を伝えやすく、融点が低いので鋳造しやすく、万一成分が流出しても土壌を傷めないことなど、工業製品にとって多くのメリットがあります。ヤマハはアルミ鋳造方法として1960年代より、アルミ溶湯を高圧で金型に注入する「高圧アルミダイキャスト」を取り入れ、製品特性にあわせて各部品に採用してきました。
1985年頃からは、アルミ溶湯の流れをよくするために金型を約300ミリバールに減圧する「減圧・高圧ダイキャスト」を実用化し、軽量化、燃費向上、騒音低減などに貢献させました。ただ高圧でアルミを流し込むと鋳物内へ気泡が入り込むことがあり、強度をあまり高くできず、溶接も出来ないという課題がありました。
そこで、デザインに優れ、アルミの質感も醸し出せるアルミ製パーツを開発の照準に、研究を繰り返し実用化したのが「CFアルミダイキャスト」※と呼ぶ生産技術でした(#1)。滑らかな曲線をもち、厚さを1~2mmに薄く仕上げることも。2003年のスノーモビル「RX-1」の車体の一部に先行採用、バイク向けでは「YZF-R6」(2003年)のリアアームに織り込み(#2)、2004年は「FZ6-S」「FZ6-N」のメインフレームに採用(#3)。以来さまざまな製品の車体パーツに織り込んでいます。最近の「MT-09」シリーズのフレームもこの「CFアルミダイキャスト」によるものです(#4)。
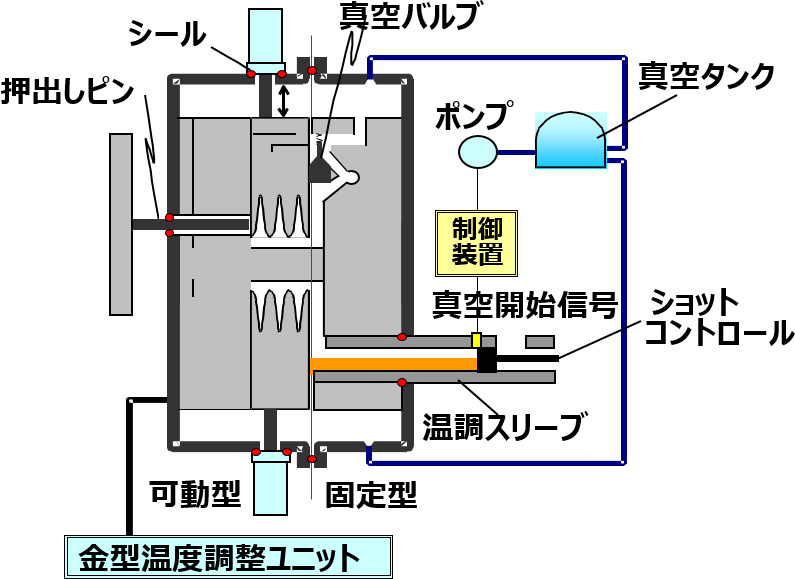

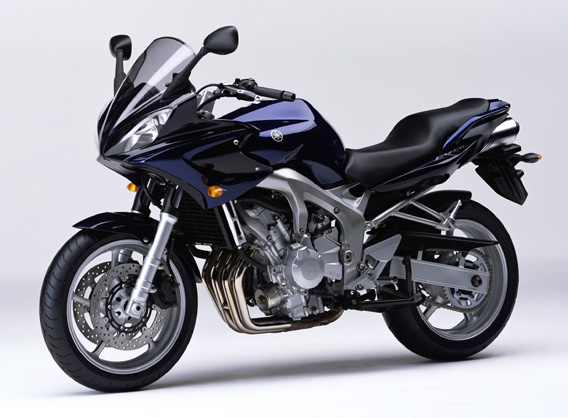
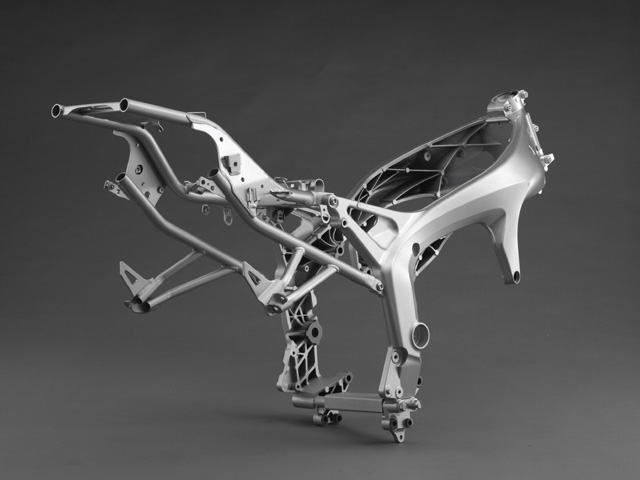
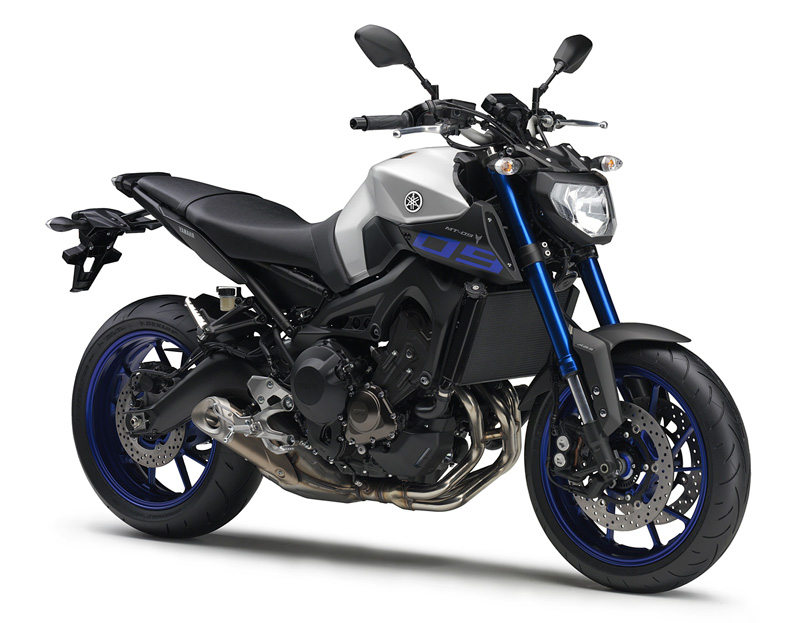
着眼点は、真空度、アルミの流し込む速度、金型温度。これらの相互バランスでした。まず金型の真空度は、従来の300ミリバールの減圧から真空に近い20ミリバールとしました。さらにアルミ溶湯を流し込む速度もアップ。アルミ溶湯が金型内で均一に凝固するように、金型の温度をちょうどよく保持するプログラムと仕組みを完成させました。
この総合的な制御で、アルミ凝固粒子の均一化を促進、含有気泡も少なくなり、アルミの厚さも部分ごとにミリ単位で作ることもでき、滑らかな曲面のアルミパーツが完成しました。ちなみに、これに似た製造技術は、当時すでに欧州製自動車のボディの一部や、薄型テレビのフレームなどに実例がありましたが、バイクやスノーモビル製品への実用化はヤマハが初めてでした。
そしてこの「CFアルミダイキャスト」技術は、次世代のエンジン開発へと展開。「CFアルミダイキャスト」技術でシリンダーを成形することで、従来式鋳造では難しいとされていたシリコン20%含有での鋳造が可能となり、めっきや鉄スリーブなしでシリンダーの耐摩耗性を確保したのです。めっき不要の高性能オールアルミ製シリンダー「DiASil Cylinder」(ダイアジルシリンダー)が誕生。今日の「YZF-R3」「YZF-R25」「NMAX」その他、多くのモデルに織り込まれています(#5)。
※CF=コントロールフィリングとは、アルミの金型への流し込みを制御するという意味です。