ヤマハ発動機株式会社は、従来比較※1で60%アップの冷却性能、製造コスト30%削減のオールアルミ製ダイキャストシリンダー、ヤマハ「DiASilシリンダー」※2を開発しました。ヤマハ「DiASilシリンダー」は、世界初のオールアルミ製ダイキャストシリンダーで、現在最高レベルの機能をもつニッケルメッキ処理シリンダーと同等の冷却性能を備え、低製造コストを達成します。
本技術は、当社が4月に公表の新中期経営計画「NEXT50」※3指針に示す経営課題のひとつ“成長戦略の推進”に繋がるコア技術となります。
ヤマハ「DiASilシリンダー」は、原材料・製造技術・環境対応、この3要素を融合させた技術です。材料は、(1) 20%シリコン含有アルミ材を使い、(2)
ヤマハCF アルミダイキャスト技術※4で加工し、(3) オールアルミ製ダイキャストシリンダーを成型します。ヤマハ独自のCFダイキャスト技術の応用で、従来では鋳造できなかった20%シリコン含有のアルミ材を使い、ダイキャスト量産が可能となります。従来の“鋳鉄ライナー”
採用が大半のアジア地域向け二輪車や四輪車にとって機能向上・商品性向上に貢献する次世代の技術となります。
当社は環境負荷の少ないアルミにかねてより着目しアルミ技術をコア技術と位置づけ、製品への織込みを推進しています。本年2月にも“薄肉かつ大物を両立させたアルミダイキャスト部品の量産が可能”なCFアルミダイキャスト技術を二輪車などの車体用技術として発表しましたが、今回はエンジン用技術となります。また本技術は、製造拠点の海外移転にも容易に対応できます。当社は今後この技術を四輪車用、船外機用エンジン生産技術としても普及・展開を図る計画です。
ヤマハ“DiASilシリンダー”のメリット(鋳鉄ライナー使用アルミシリンダー比較)
|
(1) 60%冷却性アップが可能
(2) 30%製造コスト削減が可能
(3) 優れたリサイクル性 |
|
(4) 30%軽量設計が可能
(5) 製造の海外移転が容易 |
|
|
|
※1従来比較=ピストンとの摺動による摩耗を防ぐシリンダ内側壁面に設けた筒状の鉄製パーツ(鋳鉄ライナーまたはスリーブと呼ばれる)を備えたシリンダーの意。多くの二輪車に採用されている。
※2「DiASil」(ダイアジル)=Die casting Aluminum-Silicon(ダイキャスト用アルミシリコン合金)を略した造語。
※3「NEXT50」(ネクスト50)=2005年のヤマハ発動機創立50周年に向け、次の半世紀での飛躍を図るための基盤構築を目指した3ヶ年(2002年4月~2005年3月)の新中期経営計画のこと。課題のひとつ「成長戦略の推進」とは、コア技術領域でエコ・パワーソース戦略として次世代エンジンと次世代コンポーネントの開発への取り組み、コア技術以外でバイオ領域とIT領域等での新ビジネスモデルの探索の推進のこと。
※4「ヤマハCFアルミダイキャスト技術」=(Yamaha Controlled Filling Die Casting)の略。鋳造条件(金型真空度、金型温度、溶湯射出速度)の最適化でアルミ鋳物内のガス量を従来の20%に削減し高品質アルミダイキャスト部品を量産する製造技術。2002年2月発表。
《開発の背景》
一般の二輪車用エンジンはエンジン回転数が高く(約1~2万回転/分)エンジン本体が高温になるため冷却性が重要となり、熱伝導率に優れ軽量なアルミ製が採用されています。このシリンダーは、軟らかいアルミシリンダー内壁面とピストンの間で生じる摩耗を防ぐため、ライナーと呼ぶ筒状の鋳鉄材が壁面に使われます。「鋳鉄ライナー使用アルミシリンダー」と呼ばれます。
アルミ製シリンダーに鋳鉄製の円筒を入れ込んだ構造で、耐摩耗性・耐焼き付き性が高く信頼性があり、ヤマハ二輪車の場合この方式採用車が全生産モデル中約7割で、特にアジア中南米向け製品では約9割を占めています。
しかし「鋳鉄ライナー使用アルミシリンダー」は、ライナー入れ込に伴う工程複雑化、リサイクル性、鋳鉄入りによる熱伝導効率の限界(鉄はアルミ比較で熱伝導率は3分の1)という課題もあり、さらなる環境対応性能や機能向上などがテーマとされていました。
一方、高性能二輪車エンジン用には、鋳鉄製ライナーの代わりにメッキ処理を壁面に行い、高い冷却性(「鋳鉄ライナー使用シリンダー」比較で約6割向上)が特徴の
"メッキシリンダー"が実用化されていますが、製造コスト的に課題が指摘されています。
このように「鋳鉄ライナー使用アルミシリンダー」「メッキシリンダー」は、各特色が生かされ実用化されていますが、生産コスト増を防ぎつつ、環境負荷が少なく、さらに高機能を実現するシリンダーの量産技術が、次世代エンジン技術として期待されていました。
ヤマハ「DiASilシリンダー」は、こうした背景下、耐摩耗性、優れた生産効率、良好なリサイクル性に加え、メッキシリンダーと同等の冷却性能をもつオールアルミ製ダイキャストシリンダーを低コストで量産できる技術として開発したものです。
《技術概要と展望》
耐摩耗性に優れたアルミシリンダー(内壁面)を作るには、硬いシリコン粒子を多量に含有させることが有効であり、20%シリコン粒子を含んだアルミ合金は高い耐摩耗性をもち、適した素材とされます。しかし、従来式のダイキャスト法では、シリコン含有量が増えるに伴い鋳造性は困難となり、鋳巣と呼ばれる穴が生じ、良好な摺動面が得られませんでした。
ヤマハ「DiASilシリンダー」では、高い耐摩耗性を持つ表面を作るために、シリコン粒子20%含有アルミ合金を使用します。ダイキャストが難しいこの材料でシリンダーを作るために、ヤマハ独自のCFダイキャスト技術を適用し、ダイキャスト条件をきめ細かく制御しました。
具体的には、(1)金型真空度最適化、(2)金型温度、(3)アルミ溶湯の射出速度などの項目を、細かく制御することで、硬いシリコン粒子が均一に分散した耐摩耗性の高い結晶組織を保ち、鋳巣と呼ばれる穴のない高品質のオールアルミ製ダイキャストシリンダーの成形量産を可能としました。
この技術は、製造コスト低減を図り性能アップに貢献できることから、「鋳鉄ライナー使用アルミシリンダー」採用の二輪車が約9割のアジア地域では、今後製造される製品の機能向上、コスト競争力向上に繋がる技術となります。また、自動車エンジン、船外機用エンジンへの応用と展開も可能な生産技術となります。
ヤマハ「DiASilシリンダー技術」のシステム概要 |
|
|
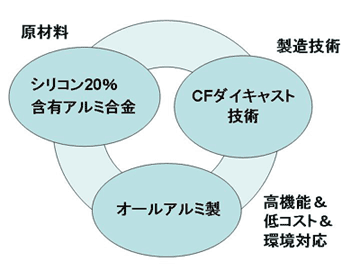 |
|
|
|
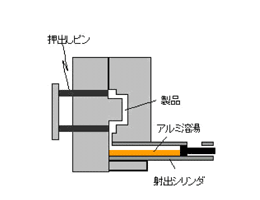 |
従来型のダイキャストの基本構造
従来のダイキャスト方式の場合、金型の真空度、アルミ溶湯の金型への吐出速度、金型温度の制御などの条件から、金型にて凝固するアルミ合金に気泡が混ざる傾向があり、良好な摺動面の形成が困難であった。 |
|
|
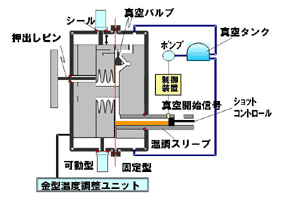 |
ヤマハ「DiASilシリンダー技術」に応用したCFダイキャスト技術の構造
(1) 金型をボックスで覆い、複雑な金型でも高真空を得る(従来比6倍)、(2) 金型温度の制御による溶湯温度の安定化、(3)
アルミ溶湯の射出速度向上(従来比5倍)などにより、複雑な形状でかつ良好な摺動面を持つアルミ製シリンダーの量産が可能。 |
|
|
|