Single axis robots (Application examples)
Introduces the applications of the single-axis robots.
- Using combination of multiple single-axis robots for painting applications
- Attaching tape to round workpieces
- Stopper and cutting system
- Stopper and pitch feed
- Positioning mechanism for jigs and tools, etc.
- Clean, dustproof / dripproof, high-speed conveying unit
- Contact stopper height change unit
- Screw tightening device
- Device to shift workpiece in width direction
- Press-fitting device
- O-ring fitting device
- Carrying and transferring equipment
Using combination of multiple single-axis robots for painting applications
Several single-axis robots are interpolated in this application for painting, etc.
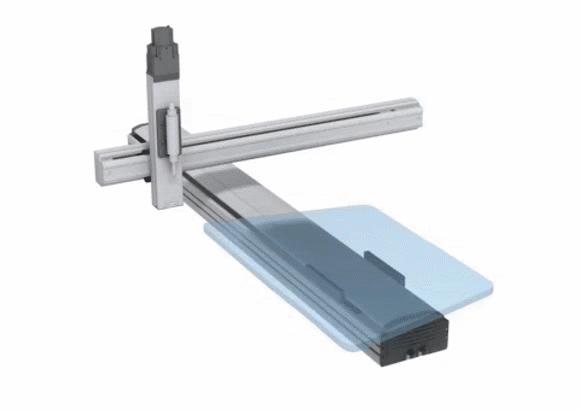
- The single-axis robot can be controlled with a multi-axis controller such as RCX340, and the combined coordinates used for linear or circular movements.
- A layout such as a desktop system, different from the normal Cartesian robot, can be configured.
- Select and combine the optimum specifications from the diverse single-axis robot lineup.
Attaching tape to round workpieces
Attach tape to round workpieces by interpolating and controlling multiple single-axis robots.
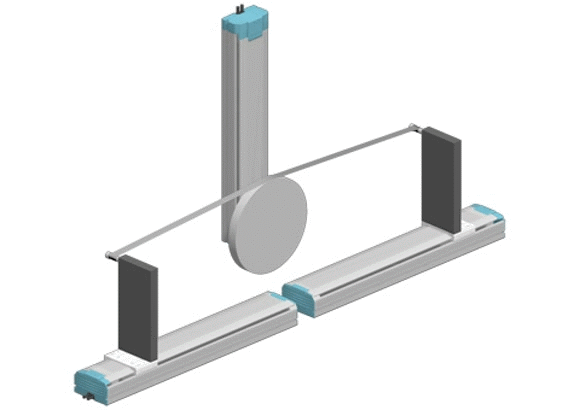
- Control multiple single-axis robots with a single multi-axis controller (multi-robot).
- Each axis can be synchronized with the multi-axis controller's interpolation function.
- By synchronizing the axes, the tension applied on the tape is maintained at a steady level, and the tape can be attached without stretching or slackening.
Stopper and pitch feed
Positioning for bread slices
Application of pressing function and pitch feed operation
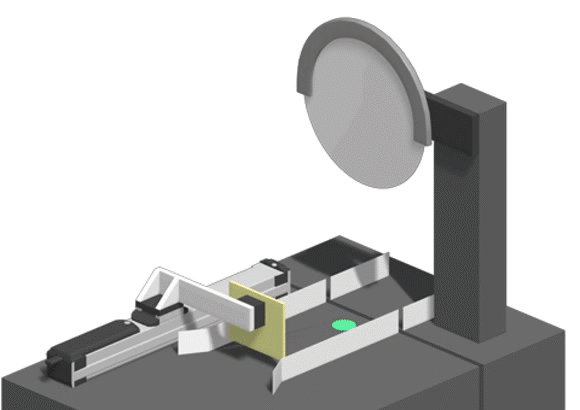
- The robot measures the bread thickness and determines the type. (Current position can be fed back from TS positioner.)
- The pitch feed rate is changed according to the bread type.
- The pressing torque can be adjusted according to the type of workpiece.
Stopper and cutting system
Cutting resin lens materials
Application of pressing function.
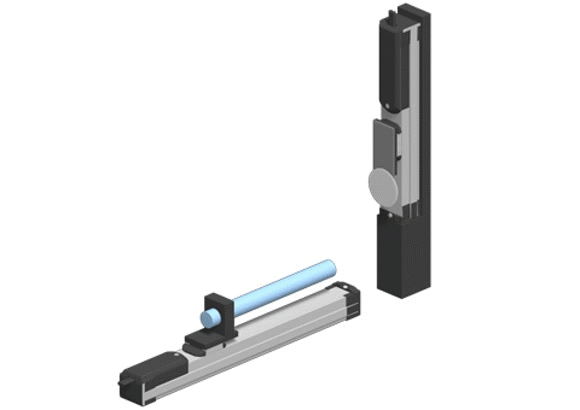
- This cutting operation uses the TRANSERVO (TS-S, TS-X, TS-P) pressing function.
- The pressing torque can be adjusted, and the timeout time and operation after reaching the specified torque can be randomly selected (continue pressing, hold position).
- The upward control can be simplified by setting continuous operation for multiple points.
Positioning mechanism for jigs and tools, etc.
Machining center cutting fluid nozzle position adjustment
Positioning in adverse environments
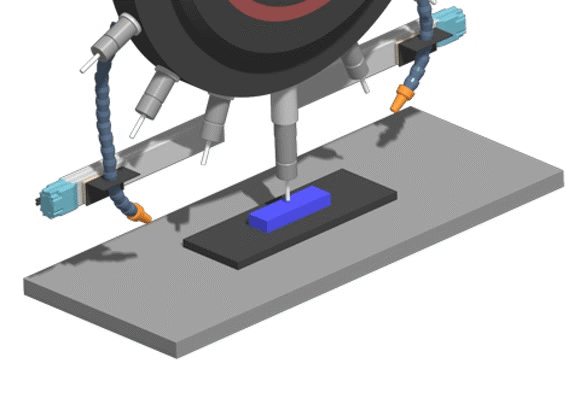
- The magnetic accuracy detector resolver enables use even in adverse environment subject to cutting fluid.
Clean, dustproof / dripproof, high-speed conveying unit
Transfer and conveyance in the clean environment.
Transfer and conveyance in the harsh environment.
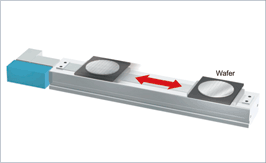
- Belt drive type robot complying with cleanliness requirement.
- With a large payload, it is optimum for conveying panels.
- Provided with specifications for cleanliness and applicable to long stroke.
- With the payload and moment permissible value at high level, it is applicable to the Cartesian combination.
- Equivalent to B10 (YAMAHA model) .
Contact stopper height change unit
Change of stopper height in multiple number of steps.
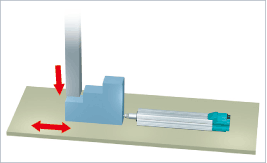
- The stop position for the stopper block is positioned by the cylinder type robot.
- It is possible to make set up done by single touch operation or automatically.
Screw tightening device
Tightening screws arranged on a straight line.
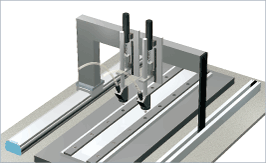
- High rigidity with a support axis added.
- Pitch selectable freely in the moving axis direction.
Device to shift workpiece in width direction
Positioning of workpieces flowing on the conveyor.
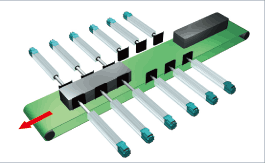
- Arrangement of multiple number of compact robots.
- Pulse string control from the upper controller.
Press-fitting device
Workpieces are press fitted in holes arranged on a straight line.
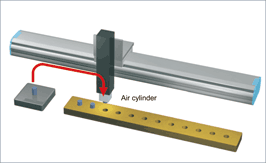
- Highly rigid frame.
- Applicable to work positions arranged linearly.
O-ring fitting device
Handling workpieces to assembly units arranged on a straight line.
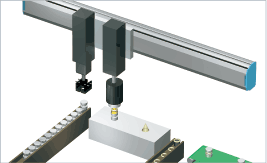
- Assembly jigs arranged on a straight line under the single axis robot.
Carrying and transferring equipment
Handling parts
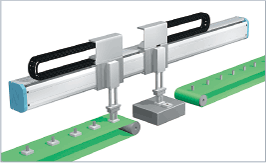
- Space saving layout using double carrier. (N15 / N18)
Application examples
Related contents
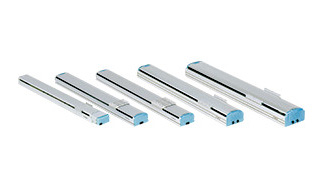
- Single axis robots FLIP-X Series (Electric slider)
- FLIP-X series include many models of 6types and 29variations for a wide range of applications.
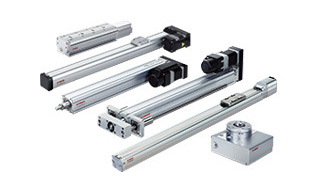
- Stepping motor single axis robot (Electric cylinder)
- Closed loop stepping motor single-axis robots, TRANSERVO series. Excellent characteristics of both stepping motor and servo motor were combined.
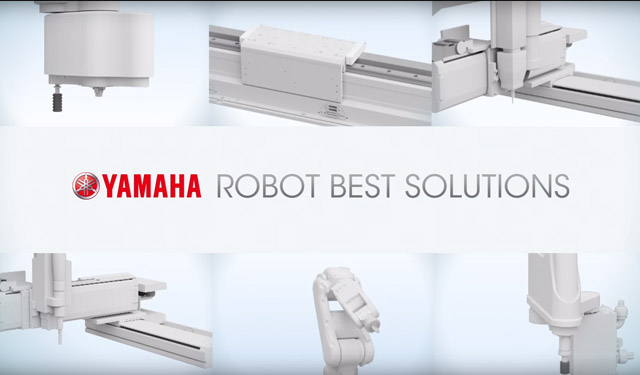
- Robot Movie Channel
- Yamaha Motor Robot Official Channel
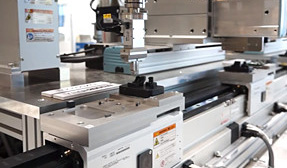
- Case Examples Handbook
- Here, we are introducing some case examples that have actually solved customer's problems.
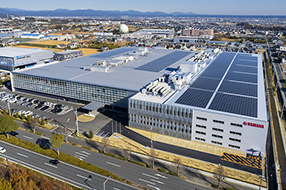
Robotics Business Unit
Sales & Marketing Section
FA Sales & Marketing Division
127 Toyooka, Chūō-ku, Hamamatsu, Shizuoka 433-8103, Japan
Telephone +81-53-525-8350 /
Facsimile +81-53-525-8378