DAYSIN THE STUDIO
Advancements in manufacturing technology and manufacturing materials have brought forth a number of revolutions to design studios. Forms that were previously thought impossible became possible. In other words, designers could create and offer new value to the end users of a product, and the ones to make this a reality are the product and production engineers. The result was also the reflection of Yamaha engineers’ sense of beauty.
Giving Form to Aluminum’s
Unique Material Qualities
For a motorcycle, which is essentially numerous parts assembled together, the look and feel of quality in both the exterior paint and the metals used have an influence on the entire machine. This is particularly true back in the 1980s when the SRX600 was being developed. When the designers were moving from design sketches to clay modeling, the lead designer took great interest in the feel of a certain metal part—the muffler cover. Normally, when working with clay models, shaped wood parts are painted silver and are seen as “metal” for the design process. But in this case, one designer perceived that just this one aluminum part would affect the entire design, so he took an actual sheet of aluminum and hammered it to accurately represent the shape and feel of the real part before adding it to the clay model.
Thanks to advancements in computer technology, it is now possible to see beforehand what a finished product will look like using 3D virtual reality technology. The virtual model can be viewed from any angle while altering the light source to view and consider ahead of time how highlights and shadows will look on the machine. The YZF-R1’s fuel tank, which emphasizes the feel and quality of aluminum as much as possible, was created through this design process.
West Coast Sunshine
and Okinawan Waters
Every company has its own style of advertising, and for Yamaha, the use of non-Japanese actors or models for Japanese domestic market advertisements is rare. Even so, the ad campaign for the introduction of the first-generation JOG scooter was shot on the sunny west coast of the United States, with cheerful young people frolicking in the sun’s glittering rays.
The relationship between design and mass-production painting technology has long been closely connected. At the time, it was common practice to hold retreats in which designers and engineers lodged together during a project.
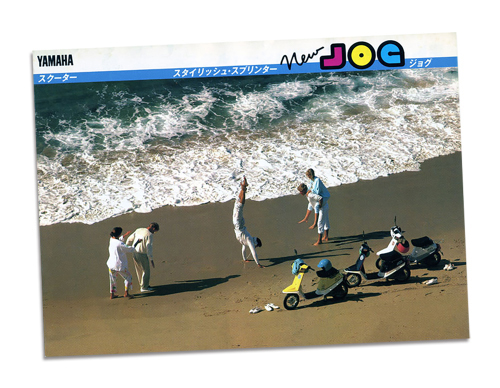
“I want the JOG to be colorful like candy, like a candy that glitters under the California sunshine.” The designers carried a camera in one hand as they walked the coastline of the Shonan Beach in Japan, and put together a color collage to recreate such a scene.
Using the color collage as their guide, Yamaha engineers collaborated with a painting company to research and produce a set of original “cocktail colors” to make their design a reality. Matching colors or ones with very similar hues were arranged into an upper and lower coat. The lower coat was combined with a colorant and the top coat was given a brightener (two coats, one bake). The end result was a depth and three-dimensional glittering quality not produced with previous candy colors or similar colors from other manufacturers. The “cocktail colors” devised in this way were also employed on Yamaha’s Venture Royale luxury tourer. The paint technician who had a central role in the project is said to have hit upon the idea while looking at coral reefs in Okinawa from an airplane.
Expressing the Value of
a Product’s
Functions
with Design
Yamaha’s EXULT Series of premium yachts boast the latest technologies and the aesthetics unique to Yamaha boatbuilding. One example is the Inboard Performance System (IPS) for 360-degree boat control, which makes docking and maneuvering through tight marina spaces a breeze. It was a Yamaha designer who realized the value presented by this system. He thought: “Since the system reduces the risk of collisions when leaving or returning to the dock, do we still need the gunwale that doubles as a bumper?”
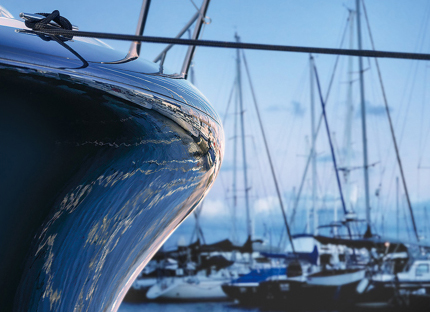
The gunwale is the flat reinforced strip along the top edge of the side of the boat hull. Imagining a boat without a gunwale was surely something that few could even conceive of.
A design doing away with the long-standing idea of a boat having a “top” and “bottom,” and instead considering the boat as a single unified form made it possible to create stunning, never-before-seen streamlined styling beyond what even the designer had imagined. Like the richly nuanced appearance of the bow and an elegant hull design with rounded surfaces and a glamorous look, for example. However, actually creating such a form would also require high-precision boatbuilding technology. To realize this new design, the manufacturing division set to work and succeeded in developing our multi-piece mold processing technology for putting together separately molded sections to shape the hull.
A Structural Proposal Based
on Proprietary Technology
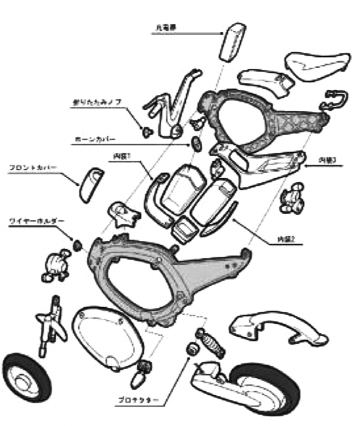
“How can we connect the functions of the handlebar, seat, front wheel and the motor-integrated rear wheel in a beautiful way?”
The answer to this came about precisely because the machine was electric-powered. “After mulling it over day after day as if trying to solve a puzzle, we realized that the most logical way would be to simply bring together all the components with a pentagonal shape.” The designers drew up sketches for the machine and even the parts layout—remarkably at almost the same time. Of course, this method was a big departure from the normal production process, but what made it possible was the styling that necessitated the functional components be laid out logically, and the fact that Yamaha already possessed exceptional aluminum machining capabilities. The designers envisioned manufacturing the EC-02’s symbolic pentagon shape via controlled-filling (CF) aluminum die-casting right from the beginning. This was because they were aiming for the weight savings and beautiful finish that could be achieved with the thin frame walls and bracing ribs this would enable, but also that if this cutting-edge technology were adopted for an EV machine, it would be a great way to draw the world’s attention to Yamaha’s proprietary manufacturing techniques.
The designers envisioned manufacturing the EC-02’s symbolic pentagon shape via controlled-filling (CF) aluminum die-casting right from the beginning. This was because they were aiming for the weight savings and beautiful finish that could be achieved with the thin frame walls and bracing ribs this would enable, but also that if this cutting-edge technology were adopted for an EV machine, it would be a great way to draw the world’s attention to Yamaha’s proprietary manufacturing techniques.
Either way, using the company’s outstanding machining techniques was in the minds of the design team, and although the “Pocke” exhibition model put on display at the Tokyo Motor Show involved no actual engineering (it was that simple of a design), it became the base for the EC-02 production model that was brought to market later. Because design had been the main driving force from the initial idea through to the frame structure itself, the EC-02 can be considered an extremely rare example of such a product. In the process of creating the production model however, it was decided to forgo using CF aluminum die-casting in its manufacture.